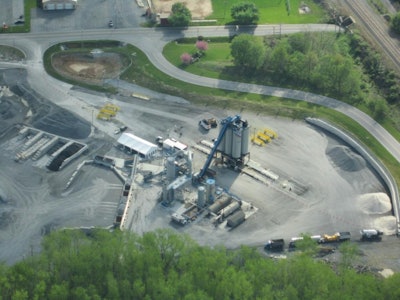
Pennsy Supply Inc. , a Southcentral Pennsylvania supplier of aggregate, concrete and asphalt, has opened a new, state-of-the-art asphalt plant in Lebanon, PA. The new facility was built from the ground up and took two years from conception to making the first mix, says Derek VanDerslice, vice president of the Asphalt Division for Pennsy Supply.
"When we made the decision to build a new plant, there was some concern," says VanDerslice. "It was the height of the recession. We knew it would take a year or two to finish the project, so we hoped that the market would stabilize by then and our investment would be worth the risk.
"Our industry has been hit hard," he continues. "We're showing to the market, our customers, and our employees that we're committed for the long haul."
From batch to drum
Pennsy Supply was founded in 1921 as the Pennsylvania Supply Company by Walter Mumma to provide quality building materials to contractors in Dauphin and Cumberland counties. Over the years the company expanded by acquiring quarries in new territories and increasing capital investment of existing production facilities.
In 1993, Pennsy Supply became a member of Oldcastle Materials Inc. and eventually formed the Mid-Atlantic Group of companies along with Slusser Brothers, Tilcon Delaware and Pioneer Concrete. Oldcastle is a vertical integrated supplier of aggregates, asphalt, ready-mix concrete and paving services in the U.S. and is one of four divisions of CRH plc, the international building materials group.
Pennsy Supply produces various asphalt mixes, including warm mix asphalt (WMA), utilizing both reclaimed asphalt pavement (RAP) and recycled asphalt shingles (RAS). The new asphalt plant located on Prescott Road is able to produce up to 400 tons per hour, allowing the company to keep up with the increasing asphalt demands in the region.
"It was becoming more and more difficult to meet the needs with our older plant, which could produce at about 270 tons per hour," says VanDerslice. “The new asphalt plant will allow us to meet the existing needs, as well as continue to grow in the future.”
The biggest change for this new Pennsy Supply plant was switching from batch to drum technology. "We really took the time to think this through," says Vanderslice. "We needed to look at our customer base, past, present, and future, and determine which plant type would best meet the diverse product demand that is prevalent in this market.
"The main question that arose during this evaluation – How do we maximize our supply efficiencies to highway work without losing our ability to effectively service the non-interstate market segment?" he continues. "Currently, in light of the recession, 60% to 70% of asphalt demand in this region is driven by PennDOT. However, we anticipate demand patterns to reflect more balance as the economy stabilizes. With the new plant we've increased our production capability from 250,000 tons per year to 300,000 - 450,000 tons per year, ensuring we can meet all our customers’ demand regardless of their size."
Given the benefits demonstrated with this new plant, the company plans to eventually replace all of its batch plants with drum plants; the next one slated for install by 2013, says VanDerslice.
In addition to the 400-tph Gencor drum mix plant, the Prescott facility has enough cold feed bins for seven different stones; RAP, RAS and WMA capabilities; five 300-ton silos with the ability to add three more; and two truck scales that allow for different orders to be loaded simultaneously.
Pennsy Supply has been using recyclables (RAP and RAS) in its mixes for the past 10+ years, and having the ability to be flexible with mixes and increase the amount of recyclables was an important consideration for the new plant.
"We wanted to be able to have the maximum use of recyclables in our mixes," says VanDerslice. "We can effectively use up to 40% RAP in a mix with this new plant. PennDOT limits are currently set at 15-20%, but we wanted to be capable for higher percentages because we foresee that as an area of focus by PaDoT in the future. Given the various stakeholder benefits realized, it's rare to have any mix today without some type of recycled material in it."
Environmental considerations
While planning the new asphalt facility, VanDerslice says the company kept an eye on environmental considerations for today and, more importantly, tomorrow. The new plant’s emissions are well below the limits currently in place by DEP.
"We not only wanted to meet current emission standards, we wanted to be far below the established limits so we could easily meet more stringent regulations that are expected in the future," he says. "This way, when the tighter regulations are put in force, we can focus on the quality of our products and service while others in our industry are busy reacting to the tighter emission regulations that they must comply with!"
To help with the goal of significantly reducing emissions, the new plant’s silo storage systems are equipped with vapor recovery kits that capture any residual fumes .
Another example of environmental benefits of the new plant – dust and noise suppression designed in. "We have residential houses that are less than a 1,000 feet from this plant, and we've been told it's the quietest plant ever – you can't even tell its running."
Dust suppression is achieved with various areas throughout the system capturing fugitive dust and pulling it through the baghouse whereby the dust is filtered from the air before it travels out the stack. The plant also has an intricate unloading system specifically designed for the dust silo so that dust doesn't free fall into the air as it is dropped into a truck.
The facility is also paved to help suppress dust, says VanDerslice. And the color of the facility as well as the landscaping were carefully planned to help the asphalt plant blend in with its environment.
Latest technologies to increase productivity
In addition to reducing emissions and suppressing noise and dust, new technologies are used to help increase productivity at the new plant. An RFID (radio-frequency identification) "easy pass" truck system matches trucks and their loads automatically, so there is no signing of tickets to slow trucks. VanDerslice says the load time for trucks went from 5 to 6 minutes down to one minute.
The old push/pull button control system has been replaced with a Gencor PLC-driven control system that runs the entire plant by computer. "There was a learning curve for our employees," says VanDerslice. "It took awhile – about three months – to trust it was doing what it was supposed to do."
Ron Witmer, a plant operator with Pennsy Supply since 1987, has one word for the old control system – "antiquated."
"With the old system, you had to watch and start everything manually, and everything had to be started in the right sequence," he explains. "With the new PLC-driven system, you push one button for the preheat system and everything else starts on its own and in the right sequence. It's a huge time saver. Now we have time to focus on other issues."
Witmer agrees with VanDerslice that there was some trust issues with "being at the mercy of a computer," but that the system has performed exceptionally. Dwayne Zimmerman, another Pennsy Supply operator – on board since 2005 – says the system looked intimidating at first, but once he was trained, it was simple to understand. Both operators agree that training with the Gencor staff helped them feel comfortable with the new system, and now they can't imagine being without it.
"Everything is right in front of you on one screen," Zimmerman says. "Starting and running the plant is simple, and troubleshooting is much easier. The system has a tattletale – an alarm system that will shut down the plant if something is wrong."
New plant helps to meet new challenges
Like other asphalt plants today, Pennsy Supply faces many challenges, and VanDerslice hopes the new facility will be there to help it through. "There's a lot of interesting challenges asphalt producers have to meet today," he says. "The extreme volatility of crude oil prices affect energy costs so the energy efficiency of the new facility will help with that. And the pressure of rising costs on flat state budgets is reaching critical mass with our entire infrastructure crumbling around us and no new funding in sight. Hopefully we'll see more funding soon and our plant, with its increased production capacity, will allow us to be ready when things take off."
VanDerslice notes that another challenge for asphalt producers in this market is attracting new customers. "Before 2008, 40% of the customer base in this market was public/60% was commercial and residential," he notes. "That has completely flipped since the recession. With the new plant, we can now extend our footprint in this market without being fearful that we will not be able to consistently exceed the customers’ expectations; regardless of size and scope. We can now go further – instead of 20 miles, we may go 30 miles – to reach those new clients."
“It takes a village to get that mix from the plant to the paver,” says VanDerslice. "There's a lot of coordination to get a ton of mix to a paver. From the guy answering the phone for the order to the truck driver that dumps it into the paver, everyone plays an important role. The asphalt industry is operating on such slim margins these days that one small miscommunication can erase any profit that was anticipated.
"We might have a shiny new plant, but our people are the true resource," he concludes. "We have a tremendous staff – the best in the industry."