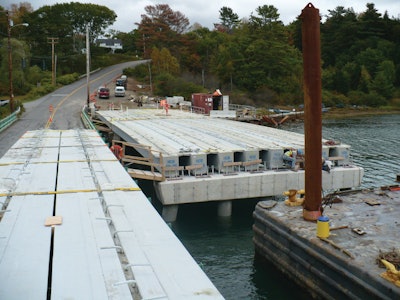
The Challenge:
Replace the 535-foot-long timber Knickerbocker Bridge with a material that could withstand close tidal waters and the harsh marine environment.
The Players:
Harbor Technologies
HC Bridge Company, LLC
Calderwood Engineering
Teng & Associates, Inc.
Wyman & Simpson
The Process:
The 32-foot-wide, eight-span, 540-foot long Knickerbocker Bridge in Boothbay, Maine, was built in 1930 and underwent a major superstructure rehabilitation in 1983. The existing Knickerbocker Bridge was comprised of a 38-span timber bridge approximately 535 feet in length. The two-lane highway bridge carries Barters Island Road over the Back River in Boothbay. It is very close to the tidal waters with only 4-feet of clearance at high tide.
For this project, the preliminary design report recommended replacing the existing bridge with adjacent precast box beams. The solution was then changed to hybrid composite beams (HCB) manufactured by Harbor Technologies in Brunswick, Maine. Developed by HC Bridge Company, LLC, a firm specializing in the development of hybrid-composite structural alternatives, the lightweight beams are made using fiber reinforced polymer. Used in conjunction with concrete and steel, the beams make a stronger, longer lasting bridge with an installed cost that is comparable to the traditional materials used to construct bridges. Since the existing bridge had a low load rating, it could not be used to transport or off-load the heavier precast box beams, thus it would have necessitated a trestle or large barge and crane.
Calderwood Engineering of Richmond, Maine, prepared the construction documents with assistance on the HCB design from Teng & Associates, Inc. Eric T. Calderwood, P.E., chief engineer at Calderwood Engineering noted that corrosion and long-term durability were key factors of design since this structure is over the salt water and there are times that the water is very close to the bottom of the beams.
"We have a good history of the use of composites in a marine environment here in Maine as there are boat yards all along the coast today that use composites so it is a material that we have confidence in for this kind of exposure condition," he said. "Further, HCB was attractive because the weight of the beams during erection would give them a considerable advantage over precast."
In order to comply with the hydraulic criteria for the new bridge, the HCBs were designed to match the recommended 33-inch depth box beams in order to maintain the required vertical underclearance. The HCB framing system was limited to two 60-foot end spans and six 70-foot interior spans resulting in an eight-span bridge with a total length of 540 feet. The beams were also made continuous for live load with negative moment reinforcing steel cast over the piers in the 7-inch concrete topping slab. According to Calderwood, the design was impacted at the substructure units because the dead load was significantly less than the original precast design; however, the engineering team had to design for significant wave action.
Construction began in the spring of 2010 with the installation of seven pile bents comprised of concrete-filled pipe piles with rock anchors tensioned into bedrock. Each bent was constructed with only one row of piles to allow for deflection under temperature loads. Only one bent was constructed with two rows of piles to provide longitudinal fixity. The only expansion joints are located at the abutments. In the fall of 2010, prior to completing the substructure construction, the general contractor, Wyman & Simpson, began erection of the HCB units. Using HCB, the contractor was able to drive the trucks with the beams on the existing bridge and off-load them using the same barge and crane needed for the substructure. With the HCB, the contractor was able to ship the beams across the existing timber bridge even with the posted load restrictions. In general, the HCBs were erected at a rate of approximately eight beams per day. After setting the first four spans of the bridge, the contractor placed the concrete for the arches in the HCB units. By placing a hopper with a steel tube into the tops of the beams, it was possible to fill each beam in approximately 20 minutes. Again, the contractor was able to place all of the concrete compression reinforcement in one span within one day.
"Each of the 70-foot long beams for the Knickerbocker Bridge weighed only 5,000 pounds," said Kim Suhr, vice president, Wyman & Simpson. "We were able to erect the beams using a small crane instead of mobilizing a 200-ton crane."
Once the beams were filled, the contractor began placing reinforcing for the deck pour. With top flange widths of 4 feet, the beams were placed tip to tip so that no deck forming was required. Scupper details, screed rails and reinforcing details were no different than those for a comparable precast concrete bridge. The first half of the deck was cast in October of 2010. After working through the winter to complete the remaining piers, the contractor completed installation of the second half of the HCB superstructure in April of 2011. The bridge was officially opened to traffic on June 11, 2011.
"What makes the Knickerbocker Bridge unique is not only the HCB framing system, but the fact that this will be the longest composite vehicular bridge in the world, the first to be made continuous for live load, and the fact that this has been accomplished with a structure that was no more expensive than a conventional concrete box beam bridge," said John Hillman, HC Bridge Company president.