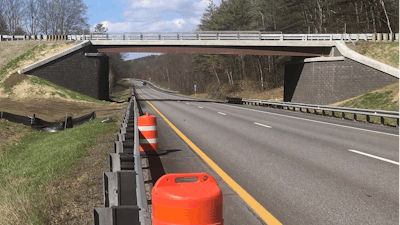
In 2017, during a routine assessment of the TH 41 Bridge 37D in Hartland, which traverses Route I- 91, bridge inspectors with the State of Vermont Agency of Transportation (VTrans) observed areas of heavy saturation, cracking, and efflorescence in the deck and pier caps. This evidence of deterioration led them to classify the deck and joints as being in “poor” condition. However, the superstructure and substructure were in “good” and “fair” condition, respectively. Rather than replace just the worn portions, VTrans ultimately found it was more economical to replace the entire bridge using the innovative Geosynthetic Reinforced Soil-Integrated Bridge System (GRS-IBS). For the reinforced abutments, engineers specified pinned segmental retaining wall units, for their durability, ease of installation, and centering system that would help keep the courses running straight.
“We knew that going with the GRS-IBS solution would save them significant dollars versus maintaining the existing bridge– on the order of $3 million –which helped to get the project pushed through."
—Chip George, Commercial Business Development, Belgard Commercial
Constructed in 1965, the existing TH 41 Bridge D37 structure was a six-span, cast-in-place deck on rolled beams, approximately 359 ft. in length and 24 ft. wide. It carried TH41 in Hartland over the heavily traveled Interstate 91. The inspection warned of the potential for full-depth pop-outs, as well as risks of concrete falling onto the interstate. The report also pointed out areas that could be improved upon, such as the bridge not being an optimal width for the state plow trucks.
VTrans evaluated several alternatives to preserve and extend the service life of the bridge. The results were outlined in an initial engineering study in June 2017 which assessed the proposed design criteria for lane and shoulder widths, safety criteria, and maintenance of traffic. After considering several alternatives including taking no action, concrete deck patching, deck replacement, superstructure replacement, and a new structure, the study ultimately recommended superstructure replacement. This meant everything above the piers need to be replaced, including the steel girders and the decks. VTrans brought in Gill Engineering Associates, Inc., to design the bridge project.
Built in 1965, the TH 41 Bridge 37D (Hartland, Vermont), evidence of deterioration led inspectors to classify the deck and joints as "poor condition" due to heavy saturation, cracking and efflorescence in the deck and pier caps.Vermont Agency of Transportation | Cold River Bridges LLC | Belgard, Oldcastle APG
Preliminary cost estimates indicated that the GRS-IBS technology would reduce the project cost from the originally considered superstructure replacement while improving the life of the bridge. Geosynthetic Reinforced Soil (GRS) consists of alternating layers of compacted fill and closely spaced geosynthetic reinforcement. The Integrated Bridge System (IBS) consists of three main components: the Reinforced Soil Foundation, the GRS Abutment, and the Integrated Approach. This robust system blends the roadway into the superstructure for a jointless interface.
For the Hartland bridge, the entire existing structure was replaced with two single-span bridges using the GRS-IBS structures in the median and for abutments. Each bridge spans one barrel of the interstate and is supported on GRS-IBS abutments with an earthen embankment in the median between abutments. With this approach, VTrans eliminated 190 linear feet of structure that would require future maintenance.
“If we were to only replace the superstructure, we would have added only another 40 years of life to this bridge,” explains Mahendra Thilliyar, structure’s project manager with VTrans. “By replacing the entire bridge with the GRS-IBS system, we have extended its life to 100 years.”
Instead of replacing the worn portions the State of Vermont Agency of Transportation decided it was more economical to replace the entire bridge and use the Geosynthetic Reinforced Soil-Integrated Bridge System - a first for the state.Vermont Agency of Transportation | Cold River Bridges LLC | Belgard, Oldcastle APG
Vermont also benefited from additional funding by choosing GRS-IBS. The U.S. Department of Transportation, Federal Highway Administration (FHWA), supports this technology and provided an additional 5% funding to VTrans for utilizing it.
“FHWA has design guidelines that include the use of GRS-IBS and it is being used across the country, where appropriate. We were fortunate the Hartland project was a good fit for this technology,” says Thilliyar.
This was also a first for installer Cold River Bridges LLC. “This was a totally different process from what we were used to,” explains Billy Labadie, superintendent with Cold River Bridges. “Representatives from Anchor came out to the job site to help get us started, which really sped us through the learning curve. It was then a very fun project and easy for the laborers because every course followed the same straightforward process.”
Vermont Agency of Transportation | Cold River Bridges LLC | Belgard, Oldcastle APG
In total, over 10,000 blocks were placed.
Though a new process for Cold River Bridges, the GRS-IBS was installed without specialized equipment; standard construction equipment like excavators, loaders, plate compactors, and rollers were used.
“Because the blocks each slide onto a pin, there’s very little movement allowed and, even though the pins aren’t meant to provide structural support, it feels like they do hold things in place. This keeps blocks from slipping out of line while we’re building the next course,” says Labadie. “The finished bridge looks fabulous; it’s really satisfying to drive by and know we built that.”
Casting a new abutment could take two years. Using the GRS-IBS system, everything was replaced within one year and in only one project instead of over two phases. Despite COVID delays, the work was completed in one construction season–six months, from May to November—and the bridge was closed during that time. Traffic was detoured off Town Highway 41 through a privately owned gravel pit after safety upgrades were made to its road. “It was critical to get the project done by winter when we would lose access to the gravel pit,” explains Spera. Some final clean-up carried over the following spring.
Vermont Agency of Transportation | Cold River Bridges LLC | Belgard, Oldcastle APG
“We knew that going with the GRS-IBS solution would save them significant dollars versus maintaining the existing bridge– on the order of $3 million –which helped to get the project pushed through,” says Chip George, Commercial Business Development, Belgard Commercial.
“We now have more confidence in the technology and will consider it on any other project where it is suitable and the conditions are right,” says Thilliyar.
About the author
Don Armstrong, PE, is a National Engineer for Oldcastle Architectural Products Group and provides technical support for the design and construction of segmental retaining walls and unit concrete pavement systems. He regularly presents to the engineering community the design philosophy, methodologies, and best practices that are the current standard of practice in the design of segmental retaining walls and interlocking pavement systems. In addition, he is part of the forensic team for both Anchor Wall Systems and Oldcastle in investigating issues related to the performance of retaining walls.