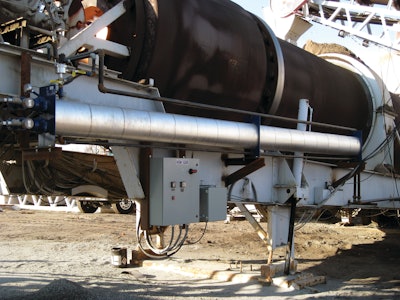
Ashmore Bros. has provided quality construction services to the upstate South Carolina area for over 80 years. The company provides asphalt paving services, site preparation, curbing, stone base, and crushing and recycling for a variety of projects. It also has three asphalt plants located in Greenville, Anderson and Spartanburg.
The plants in Greenville and Anderson both run on natural gas, but because of its location, the Spartanburg facility couldn't get natural gas piped in, so the plant ran on #2 diesel fuel. When recycled fuel oil (RFO) became cheaper than #2 diesel, Ashmore Bros. decided to switch to #4 RFO, which was about half the cost. The company added an inline fuel oil preheater to its system to help insure complete combustion.
"Typically our heaters operate with temperature control," says Rick Jay with Process Heating Co. (PHCo). "The temperature of the oil is raised to reduce the viscosity (thickness) of the oil. Much like the thermostat in your house, plant operators set the temperature, and the heater is controlled to output the oil at that temperature.
"One of the unique features about burning waste oil is that the burner doesn't 'care' what temperature the fuel oil is," continues Jay. "It's the viscosity of the oil that's important, and most importantly the oil should not be too thick. Unfortunately waste oil being what it is – and every batch being different – the relationship between temperature and viscosity in not a constant and will change from one batch of oil to the next. To overcome this, users typically set the temperature a bit higher than is likely needed to be sure the oil is thin enough. This can amount to wasted energy."
Viscosity control
Ashmore Bros. chose PHCo's Electric Pre-heater with a Brookfield AST-100 viscosity sensor to correct the viscosity of the RFO to a point which it can be used in a combustion process and better insure complete combustion.
There are many issues which make viscosity control to the burner important, says Steve Cicchese with Brookfield Engineering. "A major one is that if the fuel does not burn cleanly, it will contaminate the bag house, which filters the exhaust gases from the kiln," he explains. "Unburned oil from incomplete combustion can plug the filter bags."
Poor combustion can be caused from fuel that is too viscous or from oil that has been pre-heated to too high of a temperature, causing the 'lights' to flash off, says Cicchese. "Replacing these filters is a large expense. The cost to replace the bags is up to $40,000. This is the best argument for the viscometer, as payback is quick from even one change. Typically this happens once a year, and the cost is even more when counting downtime."
As mentioned, keeping the pre-heat temperature above the set-point to achieve a proper SSU viscosity is common. Setting the temperature higher insures there will be less of chance for a combustion problem, but it can also waste energy.
"In the past, all pre-heaters were controlled by simply heating the RFO to a predetermined temperature at which the oil viscosity would be around 90 to 100 SSU," says Chris Kittrell, PHCo's rep in the South Carolina area. "This predetermined temperature was usually an average based on the make-up of the supply RFO.
"Unfortunately, every load of RFO is different; therefore the viscosity was always slightly different per load of fuel delivered to the plants," he continues. "Now, with this viscometer, we can control how much we heat the RFO based directly on the actual viscosity value. The viscometer is directly in-line reading the viscosity value and through the controller increasing or decreasing the heat input as needed. The advantage is the heat input is exactly the amount of heat needed. The previous method very easily could have the viscosity value off from the desired value."
Selector switch adds versatility, prevents downtime
Ashmore's heater also featured a selector switch built into the control panel to allow the operator to switch from viscosity control (new method) to temperature control (old method). "The unit was 'dual' in that Ashmore can select to control the oil output by either temperature or viscoscity," says Jay. An additional benefit to the dual controls is visual monitoring in real time of the RFO temperature and viscosity as it exits the heater.
The selector switch also proved to be beneficial in preventing downtime. One of the advantages of the dual nature of the viscometer is if there is a failure, then the operator can simply switch and continue with production using temperature control.
"Two years after operating using the viscometer as the primary control method, Ashmore's heater began to 'act-up'," says Kittrell. "Unsure of the problem, the operator switched over to temperature control and avoided a production shutdown. We later found the problem to be a faulty controller. Nevertheless, production kept going, allowing the problem to be found without going into panic mode to find a fix."
Malcom Vest, production manager with Ashmore Bros., says the PHCo system was installed in 2007 and has been running for the last four years.
"With this system, we get peak performance," says Vest. "We're getting the best production rate and best return for our money. We're also not wasting fuel and not putting things out of the stack, so we're meeting emission requirements."
Vest says the plant receives several thousand gallons of RFO a week. "With the old method, we had to get a sample, calculate the viscosity then check the temperature of the preheater to match the viscosity," he explains. "With this system, we don't have to sample and calculate – it does it all on its own, which takes the guesswork out and allows us to use our time better."
Vest says installation of the component took Ashmore's electrician only a few days with support from Kittrell and PHCo. "As an asphalt plant, we can't afford any downtime," says Vest. "This viscometer is making us more competitive and has definitely paid for itself already."