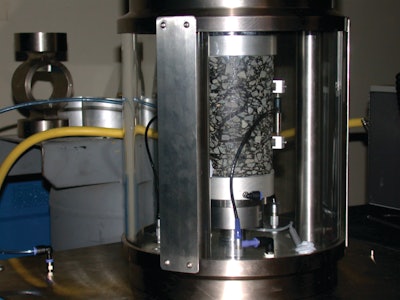
Warm mix asphalt (WMA) continues to gain momentum in the industry. As a result, tests are continuously being completed throughout the country to monitor the results of WMA compared to hot mix asphalt. Matthew Corrigan, P.E., an asphalt pavement engineer with the Federal Highway Administration, travels throughout the country testing WMA. The testing completed has helped put together a frame work for both hot mix asphalt (HMA) and WMA as well as emissions and environmental issues.
Operating out of a mobile trailer, the Federal Highway Administration completes several types of testing on WMA. "Our mobile asphalt testing laboratory trailer supports industry and stakeholder initiatives to provide solutions and support of new materials, new test equipment, new devices, test procedures, provide training in those areas, and support quality assurance and quality control initiatives," Corrigan says. "A combination of those programs came together to provide resources on the warm mix front."
The testing completed ranges greatly. "We can do anything from typical or traditional asphalt mixture and binder tests which almost any laboratory in the country can run for acceptance or quality control," Corrigan says. "In addition we have many advanced pieces of equipment and more advanced testing we've been working with for several years. Many of those technologies are ready for implementation across the country. There are more state DOTs and contractors purchasing and using that equipment."
One benefit to using such equipment is being able to test innovative materials. "The advanced testing devices give you more flexibility to use innovative materials like warm mix," Corrigan says. "You can evaluate its performance properties within the mixture itself or binder itself rather than relying on some sort of recipe or spec that dictates the quantities. You can actually measure performance properties with that specific mixture whether it is WMA, Reclaimed Asphalt Pavement, Recycled Asphalt Shingles, etc. These kinds of equipment bring a lot of value to evaluate how these different materials and innovations act if it was a pavement under traffic conditions."
Results of WMA testing
With 30,000 tons of WMA, Yellowstone National Park was one of the first big warm mix testing projects. "It had two warm mix technologies and a hot mix control that was being evaluated for long term performance," Corrigan says. "We continue to do testing and evaluation on projects like that around the country in order to support the industry."
Corrigan says that the findings of these tests are used by the Federal Highway Division offices as well as the state Department of Transportation where the project is being built. "They are using our testing data to support their look at technology to see if warm mix has equal or better performance than hot mix," he says.
Currently, there are few drastic differences between the two types of mix. "When it comes to many of the traditional volumetric type of tests used for hot mix, in most instances those are comparable with warm mix," Corrigan says. "There aren't too many differences unless you get into a highly absorptive aggregate source or a low production temperature — then you can see differences between hot mix and warm mix volumetrics."
When looking at the mechanical properties or engineering properties of the mixtures some differences do appear in laboratory performance testing. "The differences that show up are driven by how low a production temperature the warm mix uses in comparison to the hot mix," Corrigan says. "If you use a warm mix technology as a compaction aid at hot mix temperatures, than everything else is equal. If you just drop the temperature and don't make any other changes to the mixture to accommodate that drop in temperature, you tend to have an initially less stiff mixture out of the production plant because you didn’t heat the mixture to hot mix temperatures."
This material is exhibiting a softer response. However, where material produced at a lower temperature encounters less aging, the tests results generally show that warm mixes aren't performing as well as the hot mix in a laboratory test setting. "Most, if not all, warm mixes we've evaluated on the mobile laboratory show laboratory performance test results that indicate the WMA does not provide equivalent test results to hot mix," Corrigan says. "But all of the warm mix pavements placed in the field have performed very well."
To better complete tests on warm mix, they are now trying to find ways to simulate more accurately what type of aging conditions warm mixes are encountering in the field. "The standardized mixture conditioning procedures for performance testing we conduct in the lab provides warm mixtures that don’t perform as well in a lab setting, but warm mix performs equal to hot mix in the field," Corrigan says. "We see it as an opportunity to gain a better understanding of how mixtures age in the field and doing a better job replicating it in the laboratory."
Best practices for producing mixtures
Corrigan stresses the importance of following best practices with all types of mixture including hot mix and warm mix. "You have to understand what is needed to provide quality material and quality production," he says. "There are a lot of best practices that have been developed primarily for hot mix, and those are equally, if not more, important for warm mix."
Some of the best practices include stock pile moisture management or plant baghouse,exhaust gas, fumes, and other air emissions management best practices. In addition it is important to understand how plants are set up to operate and produce the most efficiently by having heat loses minimized and burners tuned and optimized to run at specific temperature ranges.
"For example, as part of the national research that has been completed we've tried to quantify and bench mark the actual emissions and energy savings," Corrigan says. "What we've found is when burners are tuned to operate efficiently at hot mix temperatures, it provides a significant amount of savings when it comes to energy fuel usage as well as reducing emissions to have the burner optimized to operate at that temperature. Similarly, use of warm mix requires changes to the plant to operate efficiently at the lower temperatures."
While best practices remain important for both WMA and HMA, warm mix production will not cure production issues. "You need to have best practices already occurring for hot mix to realize all the benefits warm mix can provide to a producer," Corrigan says. “Savings associated with a properly maintained, insulated, and tuned plant can far outweigh the savings associated with only the usage of a warm mix technology.”
Corrigan is encouraged by the continued success of WMA throughout the country. The partnership of several organizations has helped form a place for WMA in the industry. "A lot of cooperation as an industry with contractors, producers, federal agencies, state agencies, and academia comeing to the table to talk about the issues, the correct way to handle materials, the correct way to use warm mix—that has been a great partnership," he says. "We are able to make sure we are doing the best we can to get equivalent performance out of warm mix which has allowed us to implement it in an accelerated fashion. Faster than we typically would with a new technology in our industry. It has been great to have that partnership and collaboration across the board."