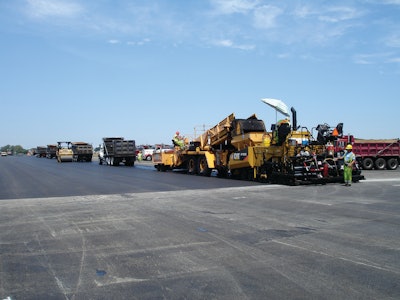
“Continuous paving is a key factor to achieving consistent density and is paramount when it comes to smoothness with the P-401 WMA mixture,” states Kevin Riley, Quality Control Manager for Aggregate Industries Northeast Division, when talking about the company’s recently completed rehabilitation of Runway 15R-33L at Boston Logan International Airport.
Aggregate Industries produced and laid down 61,000 tons of polymer-modified warm mix asphalt (WMA) during five phases that started mid-July and ended mid-September 2012. The Massachusetts Port Authority (MassPort), the owner and operator of Boston Logan International Airport, has been specifing WMA for runway and taxiway rehabilitation since 2008. An additional 18,000 tons of P-403 hot mix asphalt was produced for runway shoulders.
The P-401 WMA mixture is produced using 5.4% asphalt cement modified with latex and Sasobit wax additive. The mixture contains 20% RAP and 1% lime for anti-strip. Nominal maximum aggregate size is 3/4” (19 mm). Plant output temperature is controlled at 270o F (133o C). The asphalt plant, located in Saugus about 15 miles north of Logan, produces around 275 tons per hour.
“We know quite a bit about production of warm mix in general and the P-401 mix in particular”, Kevin Riley goes on to say. “And we’ve learned the workmanship it takes to get acceptable mat and longitudinal joint density. The trick is managing the laydown and compaction processes so certain key elements – paving speed, mat thickness, rolling patterns and mat temperature – have no significant variation.”
Planning for consistent paving
Ed Bisnette is the paving superintendent with primary responsibility for production planning and the paving process. Bisnette says planning was excellent because of the cooperation between the three management arms of the project. “We have a strong relationship with the owner and the prime contractor,” Bisnette explaines. “MassPort and (prime contractior) Barletta Heavy Division helped so much in their execution of phasing and closures.”
Bisnette is also adamant that before discussing the paving process, he has to acknowledge the role of the milling division, which milled 200,000 square yards during the project.
“On a runway project, when your fills (paving depths) are based on the grid, the milling has got be done right. We had three crews from our milling division working ahead of us. They made as many corrections as they could. The grid they cut for us was excellent. We had some deep fills in the first lift but most of the corrections we made were in the quarter inch to half inch range.”
That meant that paving depths were consistent as the paving crew hit the grades. “By the time we were paving the top lift, we made few grade corrections and those were in eighth inch to quarter inch range," says Bisnette.
The crew set up the grade control system to create a fast screed response in order to make grade corrections, if needed, within the 25-foot grid stations. Grade sensors on both sides were positioned just ahead of the auger shaft. Right side grade control made grade corrections. Left side grade control matched the longitudinal joint height.
Consistent mat thickness, which the crew handled well, is one of the key elements to high quality results mentioned by Kevin Riley. Another factor is consistent paving speed. That factor gets a lot of attention.
“There are many challenges when it comes to getting a steady flow of mix to the paver due to delays caused by security inspections, escorted travel within the restricted area and the normal rush hour traffic in and around Boston from the production facility to Logan”, says Riley. “As a section of the airfield was paved to full width each day that meant backing up and taking off 12 times per day -- material delivery was calculated around that process."
Bisnette goes on to say, “When we start a pull, we pave at one speed and never stop." Using a material transfer device (MTD), in this case a Blaw-Knox Mobile Conveyor, permits non-stop paving – as long as there are enough trucks to allow completion of a pull. How does Bisnette plan for enough trucks?
"Let’s say that we’re making thousand foot pulls during a shift," he explains. "One pull will take eight trucks worth of mix to complete.”
Ed’s calculation is based on 1,000 feet length, 12.5 feet width, and 2.5 inch loose depth. Each truck hauls roughly 24 tons.
“For that shift, I order 24 trucks," Bisnette says. "The rule of thumb is to have three times the number of trucks that it takes to complete one pull. Then, we never start a pull until there are three trucks in front of the paver and at least two at the gate waiting to come in. Each truck has GPS so I know where the next three are located."
Those five trucks will provide about 20 minutes of paving time. If the crew has to wait for more trucks due to traffic conditions or long waits at the security gate, what does the crew do before starting a pull?
“If we have to wait for trucks, we mark grades or we clean the paver,” Bisnette answers. The grid laid is laid out in 25-foot by 25-foot squares. Since paving width is 12.5 feet, the crew measures and marks the grades to reduce the grid width to match the paving width. Machine cleaning during the shift is important, too, because the polymer-modified mix is very sticky. End gates are constantly cleaned to assure that they’ll float and not hang up.
“We pave 35 feet per minute every pull and we don’t stop until the end of the pull,” Ed continues. “We made hundreds of pulls on this project and never stopped to wait for trucks. The only delay we had was the plant shut down during one shift. That was it.”
Constant paving thickness and constant paving speed were under control. What about the last two of Riley’s key elements – rolling patterns and mat temperature?
Planning the compaction process
Based on past experience with the polymer-modified P-401 WMA, the quality control team at Aggregate Industries knows that the mix passes under the screed with about 12% to 13% air voids. Their target, according to Riley, is to compact the mat to 5% air voids (allowable range 3.0 – 7.0%) and to compact the longitudinal joints to 8% air voids (allowable range 3.0 – 10.0%).
Concerning mat temperatures, Kevin outlines their targets phase by phase. “We get our best results for a smooth, dense and uniform mat when the WMA passes under the screed at about 260 degrees (126o C). We try to keep our breakdown roller working in the range of 245 to 265 degrees (118o to 129o C). The density target is 8% in-place air voids for the breakdown phase.”
For the breakdown phase, Aggregate Industries selected a Cat CB54 asphalt compactor equipped with VersaVibe vibratory system. On the test strip, the quality control team verified that two repeat passes with the vibratory system set on high frequency (3800 vpm / 63.3 Hz) and a medium / low amplitude (0.019” / 0.48 mm) produced in-place air voids in the 7% to 8% range.
The Cat CB54 has 67-inch-wide drums and can cover the 12.5 foot paving width in three overlapping passes. The result was a seven-pass pattern. The working speed was calculated and set at 290 feet per minute. That working speed and pattern precisely matches the paving speed, assuming a 90% efficiency rate for the compactor to account for non-vibratory stops and reverses. Therefore, the breakdown compactor works in a consistent temperature zone.
“We selected the CB54 for the breakdown roller for two reasons,” adds Riley. “First, we’re familiar with the VersaVibe system and like the dual frequencies with four amplitudes. Second, it’s the newest roller in our fleet and we want to get the best reliability on the project.”
Riley goes on to explain the pattern that works best for this WMA mixture.
“Standard practice for the breakdown roller is to make the first pass (in vibratory mode) approximately 6 - 8” (15-20 cm) off the joint on the hot mat and then come back over the joint on the proceeding pass with about 4” (10 cm) overlap onto the cold mat," he explains.
Achieving longitudinal joint density is often a problem on airport projects. “When it comes to longitudinal joint density with the polymer-modified WMA mixture, the rolling pattern is important but we have found that good joint construction is of equal importance," Riley advises. "On this particular project, the longitudinal joint was required to be vertical (wedge joints were not allowed) which meant running the end gate tight to the existing surface and maintaining a good feed of material. Additionally, a laborer would manually tamp the vertical edge of the unconfined longitudinal joint in order to prevent the crusting effect that a semi-rough edge tends to produce when the wax additive crystallizes in this material.”
For the intermediate phase, Riley and other on-site quality control personnel keep the compactor working on the mat when the temperature ranges from 200 to 240 degreesF. The target for in-place air voids following the intermediate phase is 94% to 95%. A Hamm 120 Plus VO asphalt compactor completed another seven-pass pattern using high frequency and low amplitude. Its pattern is somewhat different, says Riley.
“The intermediate roller worked from low to high side to minimize the movement of mix away from the joint and maintained a similar overlap between the hot and cold mat," he says. "Due to the relative ease with which mat density was achieved, the QC technician monitoring in-place density had to be careful to advise the roller operators not exceed mat density while at the same time attempting to increase joint density.”
Finish compaction begins, according to Riley, when the mat has cooled to below 160 degrees F. The finish compactor was an Ingersoll-Rand DD130 operating non-vibratory. Riley reminds the QC technician to keep the finish compactor back with limited passes,
“The finish compactor really does not figure into the compaction scheme other than staying far enough behind so as not to impact in-place density and cause the mat to exceed the specification threshold for in-place air voids.”
At the end of the project, Aggregate Industries was justifiably proud of the consistency of densities and grades they produced. “Mat density tended to be very uniform with only minor accommodations due to variances in thickness between base course and surface layers and fluctuation in air temperature," Riley reports. "In-place air voids for mat cores averaged 4.6% (allowable range of 3.0 – 7.0%) over the entire project with approximately 200 6” (16 cm) core samples tested.
“Joint density was much more subject to variance based on air temperature, wind conditions, pavement thickness, and the paving production plan," he continues. "During peak summer temperatures it was much easier to meet joint density targets. During September, we had to limit the length of pull in order to maintain consistent joint density. In-place joint air voids averaged 8.0% (allowable range 3.0 – 10.0%).”
Crew training part of plan
Pre-project planning included crew training. “We acquired a new Cat AP1055E for the Logan project," says Riley. "We ordered the latest Cat grade and slope control technology on the paver. So, not only was the paver new to the crew, the grade control was, too. It was important for the crew to be 100% up to speed with the paver and the controls when they started at the airport.”
In June of 2012, Aggregate Industries arranged for a training instructor from the Cat Paving Products Training Center and a technical specialist from Milton Cat, their local Cat Dealer, to conduct hand-off training to the primary airport crew and to the secondary airport crew. The instructors were also present to help the crews, if needed, when test strips for crew and mix certification were constructed on an access road at Boston Logan.
The Cat training instructor came back for the first week of production paving at the airport. “We thought it would be prudent to do some intense hands-on field training with the new equipment before the airport project,” concludes Riley. “Crew confidence level was extremely high from beginning to end as a result of the training."
Planning, communication and training combined to produce consistently, high quality results. “The P-401 WMA that we produce is a premium, reduced-emissions product”, says Riley. “We set as a goal to produce every ton to the same high quality standard. And to lay down and compact that product to consistently high standards. We met those goals on this project.”
Terry Humphrey works as a training consultant for Seatech Publications, Poulsbo, WA. He retired from Caterpillar in 2008 where he served as Training Manager for the last 10 years of his career. He continues to provide training and consulting services for asphalt paving contractors throughout North America at the direction of Cat Paving Products and Cat Dealers.