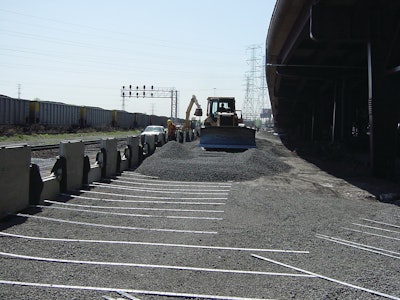
The asphalt paving industry in the United States has matured and improved due to the foresight of agencies, road builders/contractors, academic researchers, material suppliers, and consultants in our business of road building.
The past decade has seen the increased and successful use of reclaimed asphalt pavement (RAP), warm mix asphalt (WMA), reclaimed asphalt shingles (RAS), and ferrous; iron and steel slag (slag). Cooperation and careful planning for sustainability have been key to our successes.
According to the National Asphalt Pavement Association (NAPA), “Cost savings have driven some of these mix-design changes, but the adoption of sustainable practices by the asphalt industry are also a source of pride.”
Ensuring the excellent performance of asphalt pavements while increasing the recycled content (sustainability), and maintaining safety, is the successful measure of these Green Initiatives.
First use of slag
As a virgin product the initial use of iron and steel slag, meets the requirements of Green Initiatives by eliminating the use of additional mineral resources in construction applications.
Slag is a sustainable product that can be recycled and reused multiple times in various construction projects. Using iron and steel furnace slag helps preserve our natural resources, and reduce green house gases. Based on numerous environmental tests, studies, and reviews by governmental agencies, the iron and steel industry, and slag processors we know that iron and steel slag is a safe and valuable resource. We encourage its continued use as a viable, environmentally friendly product for building and maintaining the United States infrastructure.
Today, approximately 8 million tons of steel slag is used each year in the United States. The primary applications for steel slag in the United States are as a granular base or as an aggregate material in construction applications. Origin, current management options, market sources, highway uses, processing requirements, and material properties are explained in a Federal Highway Administration publication (FHWA-RD-97-148).
Additionally, steel furnace slag has been used as a raw ingredient in Portland cement manufacture, fill, and soil amendment to name but a few applications. Its primary use is as premium asphalt aggregate. Thanks to the size of the iron and steel industry in the United States, there are thousands of people employed in the slag industry.
Second and subsequent uses of slag
RAP of any nature (limestone, dolomite, crushed gravel, and slag) comes from the crushing and screening of excavated or cold milled asphalt pavements. This processed RAP contains high quality, well-graded aggregates that have been coated with asphalt. Several years ago, the State of Illinois (Illinois Department of Transportation) and the Illinois Center for Transportation (ICT) at the University of Illinois researched the expansive characteristics of RAP used as base materials.
Their conclusions led to the acceptance of the use of steel slag RAP as pavement base course aggregate and the allowable use of steel slag RAP in all asphalt mixtures; surface, intermediate, and / or base. (Their findings were published as Research Report ICT 09-055 in August 2009.)
Get your materials
When agencies engage contractors to build Hot Mix Asphalt (HMA) projects, quite often they are being built as Pay Within Limits (PWL) projects. With this change to payment schedules, the aggregate supplier has become even more actively engaged in the bidding and building processes.
Consistency of the aggregate materials is paramount to success. Material suppliers will not be paid for an inconsistent product because, as the FHWA states for a Quality Assurance Program, “confidence that a product or facility will perform satisfactorily in service” is the basis of payment. Material found to be non-compliant will not be allowed for use in the roadway, the agency will not pay the contractor, and the contractor will not pay the aggregate producer.
Before an aggregate is considered for use on an agency project, whether it is for aggregate base, HMA, or portland cement concrete (PCC), the quality of the mined materials must go through rigorous agency evaluation to determine a variety of qualitative measures, including:
- Safety – Friction testing
- Angularity – Fracture testing
- Hardness – LA Abrasion
- Durability – Soundness
- Absorption – Specific Gravity.
Slag meets and exceeds all of these quality measures time and again.
We work in an evolving industry that is aware of the need for continual improvement of quality. This is why slag producers meet with clients annually to jointly determine what the producers needs are up front and to ensure that productivity and reputation are not compromised. Slag producers ask their client to become their partner each new construction season.
Sustainability and the future
As we continue to improve our design, manufacturing, and construction processes for HMA, new opportunities present themselves. Reusing materials multiple times is a bustling industry that has grown ever since the first HMA recycling project back in the 1970s. The FHWA policy on the reuse of materials states: “…recycled materials should get first consideration in materials selection … and… Restrictions that prohibit the use of recycled materials without technical basis should be removed from specifications.”
Today there is a renewed effort to grow the asphalt recycling program in the USA because it is economically practical, environmentally prudent, and an engineered product. Agencies are committed to increasing the use of RAP, WMA, RAS, and recycled slag successfully through proper engineering and production controls. As endorsed by the FHWA; volumetric, aggregate, and asphalt characteristics must meet or exceed the current specification requirements.
Typically, to be considered for use by the agency, reprocessed material must exhibit the desired engineering characteristics of consistently satisfying specification requirements, providing an acceptable level of performance, being economically competitive with available materials, and being consistent, much like aggregate from a quarry and asphalt from a refinery. Consistency comes from knowledge of crushing and screening practices, building stockpiles, and load out. Most experienced contractors realize that establishing a top size of ½” assists in accomplishing these goals. These specification requirements and sizing tips will guide the future development and enhancements of the recycling specifications across the nation, leading to expanded use.
Reach your destination
As Deming would say, “Quality is not so much an outcome as a never-ending process of continually improving the quality of what you produce.”
The process of quality control and increasing the use of recycled material in our products is part of the journey to improving the quality of pavements for agencies and our fellow travelers. Slag aggregates are successfully used on roadways and airfields including interstates, heavy duty intersections, and intermodal facilities. Slag is paving the way to a future filled with quality pavement and environmental responsibility and accountability from our industry.