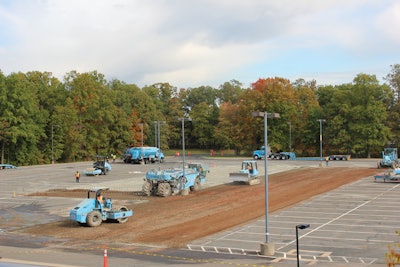
In today’s construction world where “preservation” and “sustainability” have become essential facets of many pavement projects, one East Coast contractor has been ahead of the game and is seeing significant growth in a process that both preserves and sustains existing parking lots.
Ruston Paving has been offering a full-depth reclamation (FDR) option to commercial and industrial clients for more than 20 years. And partly through their own educational efforts and partly as a result in a change in buying habits FDR is increasingly becoming a go-to option for property managers.
Full-depth reclamation is a recycling process in which the entire thickness of asphalt pavement and a predetermined thickness of base material is pulverized, blended and stabilized using some type of additive.
Tim McConnell, Ruston Paving’s pavement and soils specialist, says that while FDR is more commonly used on roadways, it works just as well on parking lots for the same reasons. “It’s very expensive to dig out and haul off all that material whether you’re getting down to subgrade or not,” McConnell says.
Lang Butler, Ruston Paving’s vice president, says Ruston Paving offers a variety of paving and maintenance options to help customers match their budgets and pavement needs. “It’s important people know what they’re getting. Some options are more expensive than others and they need to know what their expenses will be in the future based on the option they select in the present.”
He says FDR is a repair option Ruston Paving can turn to for pavements that have failed, worn out or simply expired. “The bottom line is that we use the full-depth reclamation process regularly when it’s appropriate for the job. It’s one option we can offer,” he says. “It’s another tool for the toolbox.”
McConnell says the company starts thinking about suggesting the FDR option when they’ve figured out how many “box outs” – remove-and-replace repairs – are needed. “When the pavement requires a lot of box-outs, the full-depth reclamation option can really save the customer some money while providing a better product,” McConnell says. He estimates there’s roughly a 30% - 50% cost savings using FDR over complete pavement reconstruction, but cautions that the savings can vary considerably based on pavement condition and size of the project among other factors.
“When we’re bidding a job, we don’t necessarily specify FDR on every lot,” McConnell says. “For us to recommend FDR, the parking lot has to have issues with structure where we need to get stability back in that lot. It comes down to the condition of that pavement and its supporting layer.”
“Full-depth reclamation is important to many property owners because it’s utilizing existing onsite material, material that owners of these properties have already had capital expenditures on,” Butler says. “And if you’re an owner who has parking lot failure and you have stone underneath and have already spent money on that stone it’s disheartening to see it get torn up and hauled away. It’s smarter, greener and more sustainable to re-use the material and make it better. It makes everyone happier.”
Education Leads to Acceptance
Don Barry, director of business development for Ruston says, “Our biggest challenge is educating the consumer. They’re just not used to seeing FDR proposed as an option and they don’t know what it is.”
He says in most cases contractors come in and quote a full remove-and-replace solution, so when Ruston Paving suggests the less-expensive FDR option they need to make sure the customer understands what it is. To that end Ruston Paving conducts seminars for engineers and property owners as well as “lunch & learns” with continuing education credits for engineers. Ruston Paving also relies on its website (RustonPaving.com) and videos to teach people about the FDR process.
“You can really see people understand the value in the process once we explain it to them,” Barry says.
From Driveways to Parking Lots
Started in 1943 in Syracuse, NY, as a driveway paving company, family-owned Ruston Paving is now run by President Mark Ruston, representing the third generation. In the 1960s Mark Ruston’s father, Larry, assumed control and transformed the company from residential to commercial paving. Today Ruston Paving serves only the commercial and industrial marketplace. “No highways and no driveways but everything else is fair game,” Butler says.
Since 1943, Ruston Paving has grown to more than 150 people and expanded geographically with operations in three states: Syracuse, Rochester and Watertown, NY; Manassas and Richmond, VA; and Durham and Greensboro, NC. Services include asphalt paving and site work, stormwater systems, new construction and rehabilitation of existing areas.
“On new construction, we generally provide the pavement structure from subgrade up. This includes stone, curb/gutter, grading and paving. But, if you’re expanding an existing pavement area, we have the ability to do turnkey in that situation too,” Butler says.
Don Barry says Ruston Paving has been offering the FDR option on commercial and industrial lots for more than 20 years but not to the extent it’s offering the service today. McConnell says that has a lot to do with the machinery. “The machinery and horsepower it takes to do the FDR process has improved substantially in the last 10 years,” McConnell says. “Grinders, spreaders and even compaction have improved significantly to make the FDR process even more effective.”
“The process today with the compactive effort you really need, the ability to meter the material you’re putting down and the ability to control what’s going down on the ground has improved significantly,” McConnell says. “There is a science to it and it is important that it’s completed to meet the specifications using the right machinery.”
The FDR Process
McConnell says that unlike the “train” that is used when doing FDR on roads, doing FDR on commercial or industrial properties requires a step-by-step approach where each stage follows in order.
Pulverizing. Ruston relies on its Wirtgen 2400 reclaimer/recyclers to pulverize the asphalt pavement, and then blend that pulverized material with the base, typically 8-12 inches deep.
Rough grading. After the pulverized material is blended, crews rough grade the area with motor graders and bull dozers. “We rough grade to the level we need to accommodate the new asphalt,” McConnell says. “That gives us an opportunity to correct any drainage issues in the original pavement surface.”
He says that in most cases, especially on larger projects, crews are able to move the blended material from one location to another to both improve drainage and so they don’t have to haul material from the site. “We are able to compact it somewhat more densely but not always enough to accommodate the layer of asphalt we’ll be placing,” McConnell says. “So sometimes we do have to remove some of the materials and we do that before we add Portland cement so we’re not hauling away treated material,” McConnell says.
Stabilizing the base. Once the rough grading is done a water truck and spreader follows adding Portland cement as a stabilizer, which is blended with the base/asphalt mixture using the Wirtgen unit. McConnell says the computer-controlled spreader applies the Portland cement at a specified rate. The Wirtgen machine then blends the Portland cement and reclaimed material while metering the exact amount of water into the mixture so Ruston’s crews can achieve the level of compaction and strength they’re looking for.
“The reason we typically do FDR is because there’s a poor subbase and we need to add a stabilizing agent (Portland cement) to strengthen the base. We add the water to create a uniform mix of reclaimed material and Portland cement,” McConnell says. “The binding agent you’re adding chemically bonds the aggregate together and at the same time it helps to dry it out. The Portland cement bonds all the materials together into a more stable base that’s stiffer than just a granular base. It also protects the modified base from moisture because it’s bonded together.”
McConnell says that in some cases they might not add cement until the day following rough grading because once the cement is added you have to compact and fine grade the material and then let it set up.
“As soon as we add the Portland cement and water, the job has become time sensitive and we need to get it graded and compacted in 2-3 hours,” McConnell says. “You can see the results of the Portland cement additive immediately. There are situations where our equipment has been buried and once we stabilize the area with Portland cement we can take our bigger equipment in and can drive right on top of it.”
Compaction. McConnell says compaction starts with a sheepsfoot roller in vibratory mode followed by a steel drum roller, also in vibratory mode.
“It’s a very rare FDR job where we don’t use a sheepsfoot roller. It’s a standard piece of equipment on every FDR job we do,” McConnell says. “Typically sheepsfoot rollers are used in clay-type soils but when you add water and cement to this pulverized base-and-asphalt mix it creates a sticky paste that reacts very well to the sheepsfoot roller.
“The sheepsfoot compacts deeper. We’ve got to get the compaction as deep as we can in the blended mix and the sheepsfoot concentrates the compactive effort deeper,” he says. “The finished product is not as solid if you don’t get proper compaction at this stage.”
He says the fine grading affects only the top 2-3 inches and so they finish that off with the smooth steel drum roller.
Preservation not Replacement
“Once we get done with FDR we can open those parking lots up to traffic and they can drive right on the prepared base,” Butler says. He says clients are also concerned about accessibility to retail businesses and offices, so FDR really appeals to clients with those types of concerns. “Clients are very aware of time and that’s a real big thing that helps us. We can get in and get out. They like that we can get in there and knock it out in less time [than remove & replace reconstruction].”
And, Barry adds, there’s no big hole that requires barricading to prevent people from falling or driving into it.
“A big part of it is that full depth removal leaves a hole 1-2 feet deep and, if you get rain during the excavation, it may saturate the subgrade and you may have to go in and remove even more material before reconstructing,” Barry says. “With FDR, we’re never really excavating below the existing surface. People can get right on it because it provides a cleaner, neater and safer work site.”
“We want to get our customers into the cycle where we’ve eliminated the base failure and base issues that can happen with partial box-outs and smaller repairs,” Butler says. “When this process is done, you’re actually getting to the bottom of the issues. You’re getting down deep and correcting the structural problem within the pavement.
“It’s pavement preservation rather than replacement,” Butler says. “Following FDR projects, our clients will either be sealcoating or installing a thin overlay down the road as opposed to full depth patching. It seems a whole lot of clients want to take the sustainable route.”
END
[possible captions]
“It’s not a new process but it’s not something very many contractors are offering,” Butler says. “We can provide a quality job using a less-costly sustainable process.”
From a logistics and sustainability standpoint, traditional remove-and-replace reconstruction is more difficult because the contractor has to move a lot of material in and out of the site. “That leads to other potential problems with having all these heavy trucks going in and out,” says Don Barry. “So there’s more traffic to worry about and also more potential damage to surrounding pavement.”
Tim McConnell says one advantage of FDR is that Ruston Paving can fix the drainage issues using a motor grader or dozer during the rough-grading phase of work. “Sometimes we can take material from high spots and move it to low spots so we can improve drainage. That way, we don’t have to remove it from the site.”