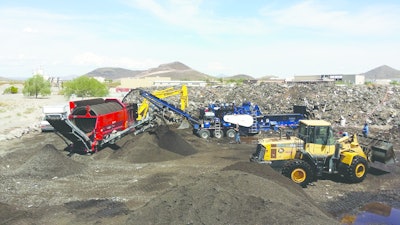
Recycling is more than a buzz word for Jason McCullar, owner of JML Energy Resources LLC based in Brentwood, Tennessee. When it comes to recycling asphalt shingles, McCullar believes he's in the right business.
"The company was founded in 2012, and is a combination of two separate entities. Our name, JML Energy Resources, reflects the diversity of our business," said McCullar. "We do more than just grind asphalt shingles for the asphalt paving community, but that's our niche, and we strive to provide the highest quality recycled asphalt shingles (RAS)."
According to McCullar, the business of grinding asphalt shingles is a profitable enterprise when the right equipment and entrepreneurial spirit combine. Upon seeing a demonstration of a grinder making RAS, the decision to have such a facility followed, and the Tennessee location took shape.
"At the time of the company formation, we had the largest private stockpile of asphalt shingles in North America with just a little over 2 million tons (1.8 million tonnes) and growing every day," stated McCullar.
In addition to the Tennessee location, JML Energy Resources currently has four yards across the U.S. for the collection of asphalt shingles from contractors: Charlotte, North Carolina; St. Louis, Missouri; Oklahoma City, Oklahoma; and Phoenix, Arizona. The company is expanding into Texas and adding a location in Missouri, plus looking to open a facility in Raleigh, North Carolina.
What's the catalyst for McCullar and his company expansion? Look no further than the technology brought to the asphalt grinding industry from Peterson, an Astec Industries company located in Eugene, Oregon.
Surveying the options
JML Energy Resources was an exhibitor at the 2014 CONEXPO-CON/AGG exposition in Las Vegas, Nevada, showcasing its RAS material. While at the trade show, McCullar explored the grinding technology options available for the company's planned expansion.
"After reviewing equipment comparisons, we chose the Peterson 4700B Horizontal Grinder; it was simply the best choice for our asphalt shingle grinding operations," shared McCullar.
The Peterson grinder
Powered by a Caterpillar C18 diesel engine with 765 horsepower (570 kW), the Peterson grinder is highly efficient and productive. The machine has a 60 in x 37 1/2 in (152 cm x 95 cm) feed opening and a hopper capacity of 9 yd3 (6.88m3). The conveyor speed on the discharge system is 450 ft/min (137.2 m/min). The 4700B has a three-stage grinding process with an up-turning rotor and large grate area. According to McCullar, the Peterson grinder with a drum rotor is specifically designed to grind asphalt shingles versus a wood grinder modified to handle shingles.
"The Peterson machine grinds on the upstroke instead of the downstroke, which makes for better quality material," noted McCullar. "Some of the other components we are enjoying include the built-in air compressor, the telemetry feature that allows us to remotely monitor the status of the equipment, and an innovative airbag feature that expels any scrap metal from the shingles before entering the grinding drum."
McCullar continued: "Peterson has an unmatched commitment to the customer in the asphalt grinding industry; they have exceeded our expectations for service and have gone the extra mile; it feels like we have a partner in our business versus just a supplier."
Not your typical RAS
What is the standard for RAS? Normal asphalt roof shingles processed through a normal or average grinder will contain between 18 to 20 percent asphalt cement (AC). JML can produce this typical 3/8-inch-minus (9.525 mm) material on request, but is also delivering an "industry first" product.
"We can deliver negative-asbestos RAS material with a 28 percent AC content," said McCullar. "In addition to the normal 18 to 20 percent AC, and 28 percent AC content, JML can create a material that is a higher percentage than that." How much higher, McCullar won't say. "The asphalt industry has never seen this before; and we are willing to guarantee the quality of the material—also an industry first."
Looking ahead
JML is committed to reusing "green" products and hopes to remove asphalt shingles from the landfill waste stream.
"With the Peterson 4700B Horizontal Grinder, we see ourselves as a forward-thinking asphalt shingle grinding company," said McCullar. "We depend on the reliable performance of the Peterson grinder to continue gaining a nationwide foothold for the production of RAS. Recycling asphalt shingles is just the tip of the iceberg for us; we expect great things as we continue to expand."
Since inception, JML has sold more than 131,000 tons (117,934 tonnes) of RAS material and that number continues to grow. A normal day of grinding yields between 700 and 900 tons (635 and 816 tonnes).
When asked about the future of JML and the addition of Peterson grinders, McCullar shared:
"By the end of year, we will have doubled in size with at least two Peterson grinders; in three years we'll likely have four Peterson grinders and be six times bigger than we are today."