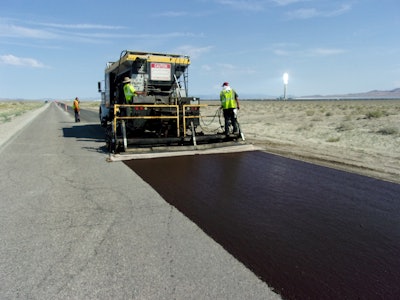
Gabbs Road is an old county road located in a remote area outside of Tonopah, NV, about 190 miles northwest of Las Vegas. An 11-mile stretch of this two-lane, 28-foot-wide roadway was in need of rut filling and micro surfacing, and American Pavement Preservation was tasked with the job.
Gabbs Road leads into the Crescent Dunes Solar Energy Project, a 110-megawatt net solar thermal power project located near Tonopah. In order to return the road to its previous condition after damage from the construction of the solar project, the Gabbs Road project had to be built to Nevada DOT (NDOT) and NYE County Nevada requirements.
Project preparation
According to Eric Reimschiissel, president of American Pavement Preservation, in order to prepare for the project, a sampling of the emulsion and aggregate was sent to a qualified testing laboratory for mix design properties.
“We also had multiple meetings with the client for clarification on the scope of work and specifications for the job,” he says.
Adhering to stringent specifications, American Pavement Preservation identified ruts with 0.5-inch-plus depression for rut filling as well as any surface scratch coat profiling which needed to be addressed.
The tire ruts were filled with micro surfacing material utilizing a 6-foot rut box.
Reimschiissel points out that rut filling is not typically done much anymore because today’s asphalt mixes are designed to be more rut resistant and stable.
“Once the rut filling and scratch coat profiling was completed, we started placement of micro surface treatment along the 11-mile section of roadway,” says Reimschiissel.
The material used for this project consisted of 3% latex modified (LM-CQS Emulsion) Type 2 for the rut fill /scratch coat profiling and 3% latex modified (LM-CQS Emulsion) Type 3 for the final wear course.
“These micro mix designs not only met but exceeded the project specifications producing a high quality product,” says Reimschiissel.
Challenges
The three-week project presented several challenges. For example, the location of the equipment staging area was changed mid-stream of the project. “The location we had was the only area we could use due to the narrow edge of the road and shoulders,” says Reimschiissel.
Because of the remote location of the project, there was also a limited water supply. And public traffic had to be accommodated full time with a one-lane pilot car.
Testing and inspections were also a recurring event on the project because of the stringent specifications.
“Client and local government inspections were conducted on a full time basis as well as daily sampling and on-site testing of the materials used throughout the project,” says Reimschiissel. “Constant communication was a big part of making this project successful.”
Constant communication meant daily crew meetings in the mornings and good organization and planning. “We couldn’t talk much during the day become of the limited, remote location,” he says. “All parties involved with this project were great to work with, which made success for all of us that much easier.”