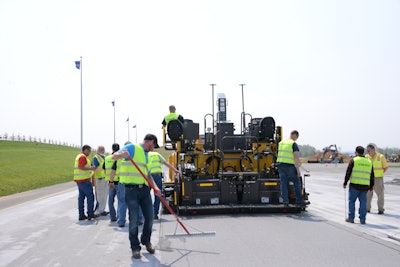
Paving has long been recognized as a job molded on precision. From temperature to speed to head of material — every team member on the paving crew influences the final product, and every mistake made is amplified further down the line.
With regular, hands-on training, however, every team member on the paving crew can gain not only an understanding but also experience making small changes that lead to a better paved road, and a well-tuned team.
“My favorite part of teaching courses is watching aha moments happen during hands-on training, especially when that’s from a student who’s been paving for 20, 25 years,” Wayne Tomlinson, compaction training specialist with Volvo Construction Equipment, says. “I know these guys are busy and getting away for training is tough, but a few days’ time in the scheme of how it impacts a crew’s bottom line are so impactful.”
Tomlinson says that while every class member comes to training with specific goals in mind, the sessions focus on some of the most common mistakes that hands-on training can help rectify.
Common mistake #1: Not controlling the head of material — More than 95% of all material faults are due to improper head of material in front of the screed. One of the most common operator mistakes is allowing for fluctuation. Chances for speed bumps and waves in the mat are increased by even an inch of fluctuation in the head of material.
The training solution: Many of the latest machines are equipped with sensors to control head of material. While this is an easy solution to the problem of fluctuation, many operators either choose not to use them or haven’t been coached on how to set them up properly. Hands-on training can give operators confidence in using these tools already at their disposal while reducing the risk for material faults.
Common mistake #2: Turning the depth cranks too much — Needlessly adjusting the depth cranks throughout the paving process can cause waves in the mat, ultimately requiring milling or repaving to meet smoothness specifications.
The training solution: To break this bad habit, operators should be trained to set the depth cranks effectively. Aside from the occasional minor adjustment for elevation changes, depth cranks shouldn’t be moved often.
Common mistake #3: Changing speeds or paving too fast — Inconsistent paving speed not only has a negative impact to uniformity, but it can also throw off the timing of the entire paving train. Rollers are also often faced with the pressure to catch up, so another common mistake is paving too fast. If the vibratory compactor impact spacing isn’t adequate, it can cause a washboard effect as well as density problems.
The training solution: Most pavers are equipped with speed limiters. Operators can limit the issues surrounding inconsistent or high speeds by using this tool. Many operators, however, either choose not to use the speed limiters or haven’t been properly trained on how to use them.
Common mistake #4: Not using auto grade and slope control systems — If there’s any chance to reduce the amount of guesswork in paving, an operator should take it. Auto grade and slope control systems help reduce operator mistakes and lay a smoother mat. Still, there are operators who choose not to utilize them or have had a bad experience with them due to setup issues.
The training solution: If auto grade and slope control systems are properly configured, they can be fantastic tools for operators. If, however, the systems aren’t properly matched to the paver’s electronics, the readings won’t be accurate. Proper training on how to set up these systems is vital to ensuring the effectiveness of the tools.
Common mistake #5: Stopping the compactor straight on — Another common mistake is to stop the compactor without turning at a slight angle. When stopping squarely, the resulting indentation will be much harder to level out on future passes. In fact, it can even get worse with each subsequent pass.
The training solution: The simplest fix to this mistake is to train an operator to stop at a slight 20% to 30% angle. Indentations made by a roller stopping at an angle are much more easily smoothed on future passes than those made by rollers that stop squarely.
Perhaps Henry Ford, the man who created such a strong opportunity for road building in the first place, summed it up best: “Anyone who stops learning is old, whether at 20 or 80. Anyone who keeps learning stays young.”
Take a look at the training opportunities available this coming year — and stay youthful.