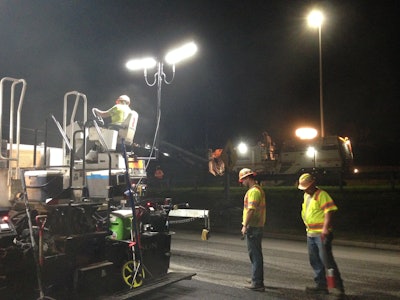
Interstate 395 is a 5-mile-long auxiliary Interstate Highway in the Bangor, ME, area. The western end of the route is a cloverleaf interchange with I-95 near downtown Bangor.
The Lane Construction Corp., based in Cheshire, CT, was tasked with reconstructing this five-mile-long road to provide a smooth and safe surface for the many vehicles that travel its length daily.
“It was definitely time to replace the wearing surface and with some rutting a mill and fill was the right treatment,” says Brian A. Raymond, senior plant manager with Lane Construction.
One of the first challenges the company had to overcome was the traffic volume. “I-395 runs through major areas of both the city of Bangor and the city of Brewer,” says Raymond. “Local traffic levels were very high and special scheduling to accommodate commuter traffic as well as increased traffic due to major concerts and festivals had to be planned into the project.”
Because of this, all work was conducted at night and planning ahead was essential.
“With many different time constraints on different ramps and different days, planning ahead was vital to the project,” says Operations Manager John Byers. “Every night a lot of work went into making sure lane closures were off the road before the specified time due to large amounts of morning traffic and increased fines. Our job superintendents Chris Randall and Adam Laird were well planned out and executed the plan.”
Rut-resistant mix
Lane Construction began milling the two-lane highway on June 5, 2016. Mainline milling included both eastbound and westbound lanes, each 12.5 feet wide, milled 2 inches deep.
After milling, an asphalt sealer was applied to the cracks in the milled surface. Next a shim layer of pavement, which was used a leveling course for the surface pavement, was placed at ½-inch thick.
For the wearing course, a 12.5mm mix with polymer modified asphalt was used.
“The Maine Department of Transportation chose polymer modified asphalt for this project because they feel it has proven to resist rutting better than traditional asphalt mixes due to the higher traffic volumes and lane merging on this section of highway,” says Raymond.
Lane Construction used the Hamburg Test during HMA production. Samples were taken at the plant during production and are prepped for the asphalt pavement analyzer, which runs a wheel across the sample for a determined amount of cycles. This is to test how susceptible the mix is to rutting.
“These tests will be able to show us if there is correlation between the Hamburg results and the durability of the road over time,” Raymond says. “The ride on the project is very good, and we are expecting to receive a bonus for it.”
Improving joint density
While paving the mainline, crews used a Carlson notch wedge centerline joint maker with a sled compactor as a compaction aid on the joint. Maine DOT also took acceptance cores in random locations.
“The centerline joint sled aided in compacting the centerline joint which is often a problem area in pavement failures,” says Raymond. “The sled helped get the compaction in that area and increase joint density to make it more durable and be less likely to fail before the rest of the pavement.”
Other equipment used on the I-395 project included: Wirtgen milling machine; Weiler E2850 material transfer vehicle; Roadtec RP 190 paver with Carlson screed; Hamm HD110 roller, Hamm HD90 roller, Caterpillar CB54B roller, and Caterpillar PS360C pneumatic roller.
Also included on the mainline paving was the Veteran’s Memorial Bridge which spans the Penobscot River. The bridge spanned 1,575 feet and was approximately 54 feet wide on both Eastbound and Westbound lanes.
The bridge was milled full width at 1.5” deep, then paved with the same mix as the rest of mainline.
A total of 29,850 tons of asphalt were placed during the project, which was completed on November 23, 2016.
Ramp challenges
In the 5-mile span that was the I-395 project, there was a total of 29 ramps to be milled and paved. All ramps were milled at 1.5 inches deep and received 1.5 inches of 12.5mm polymer HMA.
“With 11 on/off ramps in the first 2.5 miles of the eastbound side, a lot of work had to go into setting up lane closures to make it safe for our workers and the traveling public,” says Byers.
On seven of the ramps that merged with I-95, an 8-foot shoulder was also added on the right side.
“This included removing curb and overburden then filling with gravel to the correct slope,” says Byers.
Tree clearing and highway light moving was also done in these areas prior to the shoulder widening. The widening received 3 inches of base 12.5mm HMA and 1.5 inches of surface HMA.
“This project forced us to schedule things differently than a lot of projects due to the time restrictions,” says Eric Ritchie, assistant district manager for Lane. “The knowledge we gained from both the lab testing and the centerline joint construction will be very useful going forward.
“The I-395 project would not have been completed if it wasn’t for the hard work of everyone involved,” he continues. “We had many experienced people on this project which allowed us to complete the work in a timely fashion. From the Department of Transportation management, to our dedicated subcontractors, Lane management to crew and traffic control personnel, everyone pitched in to get the job done in a safe manner as well.”