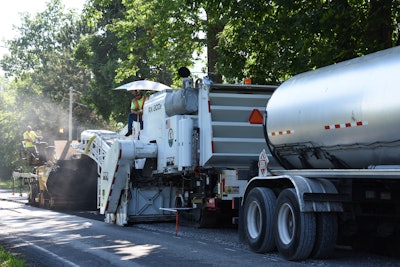
For over one hundred years, the Gorman Brothers of Albany, NY have been true to their firm’s inception as a company of preserving roads. Now three generations later, that mission has not changed, they have just been raising the bar as time has progressed. The firm has put the company ahead of the curve of their competition by incorporating technological advancements while instituting innovative improvements to existing equipment and methods while staying true to their beliefs.
Continually taking the bull by the horns for better control over their fate through necessity and desire for a better method and cost effective product to their customers, company employees along with owners, Mark and Tony Gorman, have successfully simplified and shortened a Cold-in-Place Recycling (CIR) train. CIR is a process of extending the life of roads by many years while utilizing 100% of the existing road through recycling.
It may be altruistic to think recycling should be implemented more, but Mark Gorman feels it should be increased for the planet, as well as being a more cost effective means to states or municipalities with tight funds and deteriorating road infrastructure. Yet, recycling and road preservation is not new. Our forefathers have been acting on this concept since inception of roads and trails, or because of limited means.
What has become current is the simpler form of the CIR process with improvements and scientific implementation from that technique since Gorman’s initial recycling train in the 80’s, one of the first on the east coast. Staying true to the company mission of maintaining high standards within the company as well as to the end user, (the commercial and traveling public), a new Roadtec RX-900e milling machine equipped with bolt-on packages used for Cold-in-Place Recycling has been added to their equipment fleet. The packages allow for more utilization of the machine when not used for the standard milling road surface procedures.
All actual and scientific data reflect a significant cost savings with CIR when enhancing and rehabilitating roads in need of repair compared to a mill and fill application or just overlaying the existing damaged road. Up to 50% can be saved in this technique when applicable over cracked (fatigue, block, reflective or longitudinal) roads, potholes, or rutting and raveling failure. It is savings in actual cost for raw materials, and savings in time and cost when there is no need for hauling asphalt to a paver since this is done in-place by a train of several pieces of equipment. There is also greater cost savings in its longer shelf life as a better road before additional repairs need to be made.
The energy savings are even admirable by not needing hot temperatures required for the newly laid mat but by utilizing ambient temperatures of the existing recycled road once ground with the milling machine and rejuvenated with emulsion or other chemicals in the same equipment prior to lay down by a paver as part of the train.
The reasons for its cost savings are logical, but the benefit to deter cracks from coming through the newly laid road is impressive, very impressive to officials who are looking at the bottom line in a never ending need to maintain and upgrade crumbling roads throughout their territory. The material being recycled becomes a binder grade same depth pavement with a future “sealer” over the new asphalt layer. That could be a simple chip seal process or thin hot-mix overlay (HMA) preventing rain or water intrusion.
“The benefits to municipalities or even urban regions are two- fold," Mark Gorman says. "One is the cost benefit being less expensive. Two is its longer life as a good road. It’s better because it’s cold mix, therefore it’s much more flexible. You can put a hot mix over it, but because there is this flexibility underneath the hot mix, the cracks don’t come up. Probably 90% of the time the cracks don’t come back. Cracks could come back in a year or two under different applications, this method would take about five years or more to start having cracks come back.
“It’s also an unbelievable process over old concrete roads that have been resurfaced with asphalt. When we recycle everything down to the concrete with the flexible base recycled layer between the concrete and surface hot mix layer, the cracks coming up from the concrete get diffused because the base course is so flexible. It gets dispersed before they get to the top, since there is no straight line to the surface,” Gorman explained.
When the Roadtec RX-900e is used in the recycling phase with emulsion package for cold-in-place recycling, the pavement preservation specialists at Gorman have made the technique into an art form while maintaining high-tech labs that develop mix designs for their road construction projects from a plethora of customized emulsions at their three million gallon storage capacity facility in Scotia, NY.
The cold-in-place recycling process is as John “Doc” Dearborn, quality control technician with the recycle trains, stated that they have modified the Roadtec RX-900e milling machine to grind about four inches of pavement, normally twelve feet wide. With the RX-900e, it can be brought down to narrower widths when needed, particularly on winding county roads, which gives them the ability to do wide typical lane roads in towns or smaller mountainous roads in New York or Pennsylvania.
“In this case, we have the Roadtec machine in a down cutting-head rotation so that the RAP (Reclaimed Asphalt Pavement) has a finer gradation, because the teeth come down on the road and cut little pieces instead of the machine up cutting which can produce large blocks of RAP. It improves the control of material sizing. An additive spray bar is mounted on the cutter housing to inject emulsion or foamed asphalt into the cutter housing. This additive is then thoroughly blended with the milled material by the cutter drum. After mixing it, the material is conveyed to a standard lay down paver (with Roadtec’s attached conveyor) and the road repaved immediately,” “Doc” explained.
The project designed emulsion is stored in a tractor trailer that is being pushed ahead of the milling machine with a push bar completing the current train. When the Gorman Company first started this process back in the 80’s, the train of equipment was as long as 300 feet with four different specifically used units. It has been simplified to about 75 feet for the whole operation, making the process more maneuverable through town streets or over winding narrow roads. The power of the RX-900e has not been a problem at all for the train to move forward while recycling the asphalt acting as a crusher, with designed emulsion or foam evenly blended for a unified recycled cold mix.
With the upgraded RX-900e model machine, more controls for better emulsion and foam delivery have been instituted along with a more consistent flow meter. Doc further explains: “There is a computerized spray system that brings the emulsion back from the tanker. The computer regulates the amount of emulsion to the mix at the cutter head, according to what depth you are cutting, speed you are going, and the percentage of emulsion you set into the computer which has been derived by the lab testing.”
He continued, “We lay out a certain percentage again, according to specs and according to what the lab tells us to bring the gradation of that material up to a binder spec. In most cases in NY, that would be 20% of a number 2 or 1 ½” stone, which we lay out on the road in a calibrated way, so that it is exactly the amount needed at all times. The stone supplements what is incorporated within the cutter head with the material being ground (RAP), along with the asphalt emulsion sprayed and mixed thoroughly to get the best binder possible.”
“By making the operation smaller, it gives us the availability to do smaller projects, or get into towns that have shorter runs along urban or residential streets. They may be as short as 600 feet long and 30 feet wide, like we did in the town of Colonie, NY, a suburb of Albany. It also helps when in the urban areas with businesses. Traffic flow is quicker and businesses less inconvenienced,” Dearborn continued.
The company’s RX-900e machine has been modified through a long relationship with Roadtec and their engineers. Just this past year, the relationship has included a new dealership to the group, Tracey Road Equipment of Syracuse. Scott Collins, VP of Tracey Road, explained that the company has been involved with asphalt and road building for over 20 years, so the dealership will make it easier to solve any problems being so close to their customer base. Roadtec in the past has been dealing with the customer directly, with an excellent parts inventory, and respective problem solving association with field personnel, as well as great service through their field representatives.
But with the newer computer controls and modifications to the spray package, close working relationships with company and dealer networks help customers like Gorman Bros. increase their productivity, while still getting the results needed and expected. Crews working out in the field everyday with the equipment also have a better understanding of what should or could be done with minimal tweaking, or having something incorporated by Roadtec later while enhancing the bottom line for all involved.
One of the findings Doc Dearborn has centered on during the CIR process is that the paving screed operator should be aware of laying down the mat properly. He has to be cognizant of what is being ground and sent to the screed without running out or having too much mix and still try to correct the road grade, particularly when the original road had deep ruts or potholes, shoving or damage.
“That’s why we have a large hopper to carry a lot of material or surge, so we have recycled material to fill a dip, and when we go over a high spot, we have room in that hopper to fill up. We try to correct grade and slope as we go, creating a smooth even mat,” said Dearborn.
One road being rehabilitated in the foothills of the Catskill Mountains was Clouberwie Road (Route 36) in Middleburg, NY. “The road was 19 feet wide. We are able to reduce our cutter head size down to 10 ½ feet wide which gives us an overlap on each pass, making sure we don’t miss anything in the center. The county wants about a finished 21 foot wide road. We are still able to put the centerline back where it belongs at 10 ½ feet, supporting the cross section and the crown in the road. This is particularly important during the winter with snow crews and trucks blading the roads in the central New York region.”
Virgil Pangburn, Schoharie County Public Commissioner with 40 years of experience said that the last time the road was paved probably was 15 years ago. The roughness and degradation of the road meant that there should be a four inch depth to be recycled which included the widened area. Two inch stone was supplemented ahead of the train and in the range of 2% emulsion added to the entire mix. The recycled mat will be the binder with a two inch thick type 6 hot mix (HMA) over it, laid by the county’s own equipment and crews for the 2.15 mile project in both directions.
“I have been using this method throughout the county for at least five years with great results. Life expectancy for the street through the Kits Program is anticipated to be at least ten years,” he explained.
The Roadtec RX-900e will be tracked by Gorman’s maintenance personnel through their GPR or Gorman Process Reliability program. About eight years ago, with the help of a consultant and his Total Process Reliability software, Senior Vice President Kevin Nichols at the Gorman Group turned a deficit of over a million and a half dollars in the maintenance shop and equipment inventory to breaking even over a six year span. Consolidation, duplication elimination, equipment standardization, a NAPA store in their facility, streamlined personnel, and better equipment with operator/supervisory inspection all were large factors into better control over costs. So now they are running “best in class” in their maintenance operation with only 2% in break down rate. Looking at it the other way is even more impressive. Their up-time rate is now 98%!
“It helps with our bottom line, and our production. It made us more profitable because our production went up and we were running more consistent every day, so our margin increased. Our 2011 Roadtec milling machine RX-900 has done well for us. We will be looking closely at the new Roadtec milling machine in the same light as it works in the CIR process with the new emulsion packages,” Nichols says.