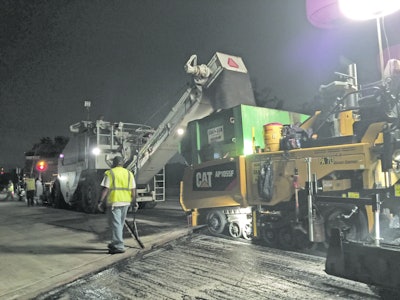
Ingevity continues to participate in numerous projects demonstrating how warm mix Stone Matrix Asphalt produced with Evotherm can eliminate the need for fibers. But what if you’re a contractor or agency trying to use Evotherm for the first time? What does the process look like? What are some of the challenges in making this change? The state of Maryland has some answers.
In late May 2017, Maryland Paving wanted to use Evotherm on a SMA project on Interstate 195 (I-195) in Baltimore. I-195 is the main connection between terminals at the Baltimore/Washington Thurgood Marshall International Airport and highways like I-95, I-97 and Maryland 295 that lead to the cities of Baltimore, Annapolis and Washington, D.C. Prior to this project, Maryland Paving had tried a small portion of fiberless SMA with Ingevity’s Evotherm in 2016.
Maryland Paving has been supplying hot mix asphalt services since 1964. The company operates six asphalt plants across Maryland, plants that continue to be recognized by the National Asphalt Pavement Association with the “Diamond Achievement Commendation.”
Although MDOT was a pioneer in the use of SMA across the United States, they were still new to the capabilities of warm mix additives in SMA. For Maryland Paving the challenge was if they used Evotherm in the SMA mix to remove the expense and hassle of fibers, the mix would require less liquid AC. But the state was requiring SMA mixtures be at least 6.5 percent liquid AC. Maryland Paving worked with the DOT to demonstrate how warm mix was a more cost-effective alternative for SMA mixtures, which would require changes to the specification.
Compared to a standard SMA mix requiring 6.5 percent binder and 3/10ths fiber (by content volume), the warm SMA allowed complete binder coverage with only 6.2 percent AC.
Maryland Paving
According to Jeff Graf, general manager and vice president of Maryland Paving, the MDOT SMA project was a 6,000 ton informational pilot program to determine how well the warm mix would stand up to a heavily traveled interstate artery serving the Baltimore/Washington D.C. area.
“The existing section of roadway was in good shape and we approached this particular project as a lane improvement project by applying a two-inch overlay to 2-1/2 lane miles and shoulder,” Graf explains. “We did an original investigation of warm SMA for MDOT on I-83 shoulder back in 2012-2013. We experimented with temperatures ranging from 310 to 270 degrees F on mix designs using PG 76-22 and PG 64E-22. Typically, a hot mix design would leave the plant at a 325 to 335-degree range. A standard warm design can leave the plant at 275 degrees.”
The reason a warm mix SMA design does not require a fiber component is because the asphalt cement binder remains at a cooler temperature. Fiber is not used to help fill the voids of the mix, but rather to hold the binder in place.
“It was a challenge to provide a cost-effective SMA mix before Evotherm,” explains Graf. “Adding Evotherm allowed us to eliminate the use of fibers and decrease the amount of AC needed. That’s a cost savings right there. Plus, we were able to reduce paving temperatures by using warm mix. Then our conversation with the DOT became less about not meeting the specification, and more about why changing the specification to enable the use of an additive like Evotherm could be better overall.”
“We were able to produce a fiberless SMA mix with Evotherm at temperatures as low as 270F,” reports Mike Harris, Quality Control Manager at Maryland Paving. “The mix ran great while at the plant.”
“The gauge technician was skeptical that the mix would compact at lower temperatures,” explains Pete Truncale of the field applications engineering team at Ingevity. “Even as temperatures of the mat decreased, compaction numbers on the gauge rose. Maryland Paving saw densities of at least 96 percent.”
“An SMA mix design is very gap graded design with very little fines used,” Graf notes. “On a standard SMA mix you would have to keep the rollers tight to the paver to achieve compaction on a polymer modified 76 binder. We had ample time to achieve density with the warm SMA design. We were able to achieve compaction at 250 to 260 degrees, when a standard mix would only allow final compaction at 275 degrees.”
With the Evotherm liquid additive blended at the refinery with the AC binder used on the project, the Maryland Paving crew achieved 95 percent optimum density on the project.
Graf is not surprised about MDOT’s pursuit of a warm SMA mix, considering the fact that the state agency has been a pioneer in specifying the mix since the 1990s.
It’s unfortunate it was not a larger project for test results, but Graf estimates an energy savings of 10-12 percent in going from a hot to warm SMA mix design.
“We also saved on the cost of not having to assign another person to maintain the fiber supply at the plant during production,” Graf says. I know as MDOT has an opportunity to fully evaluate the project after it has been exposed to traffic for a period of time, they’ll want to pursue larger projects.”