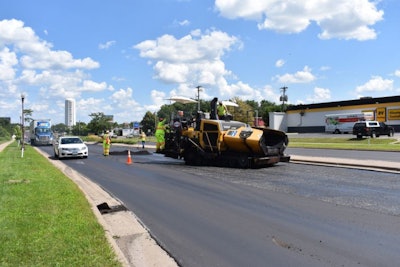
As agencies continue to try and do more road work with less money, contractors are tasked with finding ways to make those dollars go further. Recycled asphalt pavement or RAP made up nearly 39% of all asphalt pavement mixes produced in 2017, a key indicator that asphalt producers are working to be more resource responsible as they apply technologies and innovations to make long-lasting asphalt pavements.
In order to boost sustainability and the life-cycle of these high RAP mixes, additives are introduced back into the recycled content to restore old asphalt to near its original properties and create a pavement that is long lasting and less susceptible to cracking or rutting.
One such additive was recently installed on a test section of roadway in Hopkins, MN. The product, Cargill’s Anova Asphalt Rejuvenator, is not only allowing the Minnesota DOT (MnDOT) to save money by using more recycled material, but also reducing their carbon footprint with this bio-based material.
Anova in Action
Developed nearly five years ago, the Anova Rejuvenator was developed to address the need of incorporating higher amounts of RAP into a high performance hot mix asphalt application without sacrificing durability.
“When asphalt ages, the fractions in the pavement start to change and cause an imbalance in the chemical makeup that has implications in terms of the performance and especially the durability of the material which can lead to cracking and failure,” Hassan Tabatabaee, technical manager for Cargill’s road construction business says. “When high amounts of recycled or reclaimed asphalt pavements are used in new pavements without treatment, those issues are carried on into the new mix.”
Anova, a chemically modified additive from bio-renewable plant-based sources, rebalances those fractions in a targeted way and replenishes them with a bio-based version of those missing fractions to bring it back to the performance of a lesser-aged asphalt binder and restore performance and durability.
The product is added at the asphalt plant facility, similar to the way an anti-strip additive would be introduced in-line with the virgin asphalt binder.
“The introduction of Anova doesn’t change the process for the plant producer or the paver in any way and that’s by design,” Tabatabaee says. “The contractor doesn’t need to change anything. They see a mix that works well, compacts well and doesn’t give them any difficulty.”
On a 1-mile test section of Excelsior Boulevard in Hopkins, MN crews installed traditional asphalt mix on the eastbound lanes of Excelsior between 11th Avenue and Church Lane.
In the westbound lanes, crews stripped off the current layer of asphalt, injected it with Anova and immediately reused it. In this case, 125 tons of asphalt normally destined for the scrap yard was put right back on the road.
“The conversation started with MnDOT wanting to try innovative solutions and try to improve the sustainability of their roads,” Susan Listberger, Cargill product manager says. “The project in Hopkins centered on all aspects of sustainability. Making sure the product performed very well and that we could increase the recycled content without sacrificing performance.”
Typically, a MnDOT standard mix would contain about 30% RAP, but with Anova, the mix used 45% RAP. For the test section, nearly 5,000 tons of mix was produced. And using recycled content saves big money.
“By using recycled content, often contractors can save some money,” Listberger says. “The intent with Anova is that contractors continue to save money while getting higher performance and higher durability. The cost in use will be lower with Anova then a conventional mix today.”
The additive has been used on parking lots and other commercial applications but this is the public roadway where Anova is being tested.
“In this application, we’re using 45% RAP but in different plants we’re producing 50%, 85% and even 100% RAP mixes,” Tabatabaee says. “With the right design and the additive incorporated, we’ve demonstrated that we produce a 100% RAP mix without a compromise on quality.”
Cargill is also working with NCAT and MnRoad to install further test sections to see results in even the most extreme conditions.