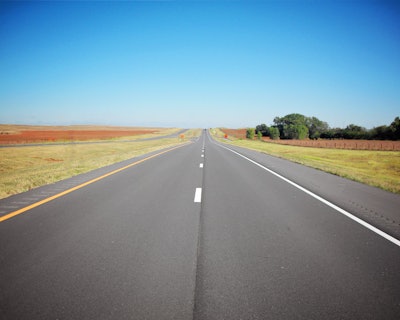
Contractors work on impactful projects everyday and seldom get the recognition they deserve for their hard work. However, state and national asphalt pavement associations have award programs to help celebrate these projects and give contractors the credit they deserve.
This year, the Oklahoma Asphalt Pavement Association (OAPA) announced their 2021 award recipients and Cummins Construction Company was awarded as winner in three of the six categories. In the Full Depth category, Cummins won for their work on US-183/US-270, a five-mile stretch of roadway in Woodward County.
US-183 is known as the Western corridor for truck travel coming from Kansas down through Oklahoma to I-40. Current traffic estimates on these highway segments is 4,900 vehicles per day with a 2038 projected traffic of 7,200 vehicles per day, with 33 percent being trucks.
The project scope of improving the highway to a four lane divided highway with a median was originally proposed in 1998 but was re-opened in 2016. The two-lane highway has been in the process of widening to four lanes since then and this stretch is one of the last segments to be upgraded to four lanes. Cummins bid the project and began construction in late 2019.
In With the New
The existing highway had several segments with two 12-foot paved lanes with 10-foot paved shoulders and has other segments with three and four 12-foot paved lanes with narrower paved shoulders.
Cummins broke the work into three phases. Phase 1 included completing drainage structures, adding new lanes and detouring traffic. Phase 2 featured construction of the two new lanes and Phase 3 featured reconstruction of the old lanes and additional drainage work. Construction included removing 316,000 cu.yds of earthwork. During Phase 2, Cummins completed the two new lanes first. They used cement soil stabilization on the new lanes and paved everything but the surface. They then opened those lanes up and began the work on transforming the existing lanes.
“By completing the new lanes first, we were able to keep traffic moving in both directions,” Jack Marshall, paving operations manager at Cummins says. “This significantly helped reduce delays and kept our crews out of moving traffic.”
In Phase 2, a 4% cement soil stabilization was used to set the base before paving. The subcontractor for this phase placed 165,000 sq.yds of soil stabilization subgrade for the two new lanes.
Paving on the new lanes then began. Cummins used two BOMAG CedarRapids pavers on the project. Their main paver, a CR462, was outfitted with a custom drag ski made by the Cummins team.
“We run a 60-ft. drag ski on all our machines with a Topcon sonic averaging system (SAS) on top of that,” Gary Sharp, equipment manager at Cummins says. “All the crews are pretty much pulling the 60 foot skis wherever they can to get the ride out of it. By doing that with the SAS, it stretches any kind of deviations in the road out over 60 feet instead of 24 feet. This obviously makes the road ride a lot better.”
Cummins worked with their central lab to create the mix design for this project, placing four lifts for each side of the project.
Lift One: S364 - 65,200 tons
Lift Two: S376 - 18,087 tons
Lift Three: S476 (Surface) - 14,370 tons
Shoulder: 7,000 tons
Out With The Old
Next, Phase 3 began and Cummins got to work cold milling the top 2-in. of the old pavement off on the existing lanes. Cummins also needed to remove two 10-ft shoulders.
“The road had two 10-ft. shoulders on it obviously when it was a two lane,” Marshall says.”We took the inside shoulder from 10-ft. to 4-ft. using a Wirtgen mill and took all 6-ft. foot of the road and came back to make it a 4-ft. inside shoulders, so there was quite a bit of removal there.”
Cummins removed 75,000 square yards of asphalt just to get the shoulder changed. Full-depth repairs were also needed along the existing roadway in several places as well and the crews worked to ready the roadway for paving.
Cummins used material transfer vehicles (MTV) on this project for several reasons; to keep the trucks from impacting the pavers, for remixing of the material and mainly for production reasons.
“We don’t have to run an MTV except for the top two lifts, but we always do,” Sharp says. “We can get as much as 100 more tons per hour put down using an MTV versus without using one.”
In all, over 98,000 tons of asphalt was placed to widen and repair this stretch of roadway. The company used a combination of BOMAG and Dynapac rollers to achieve compaction, a breakdown, pneumatic and finish roller. The Cummins team was also in charge of quality control using Troxler gauges.
People, Production & Paving = Success
None of this work would have been possible without the dedicated crew members at Cummins.
“We are employee-owned and the people that are out there paving have been here so long and knowing that they're part owners of the company, they take so much pride in every job,” Mike Beier, area manager at Cummins says. “They will always go that extra mile to get a good ride.”
And Cummins keeps their employees and equipment operators top of mind, investing in the equipment the crews are comfortable with. In fact, Cummins has 11 BOMAG pavers based on the request of their teams.
“We’ve been using BOMAG (CedarRapids) pavers for years,” Sharp says. “The crews are comfortable with the machines, they understand every part of them and feel they are more operator friendly than any of the other pavers out there. If anything were to break on these machines, they know exactly what needs to be done to get it back up and running.
“We take into consideration the value of the equipment, but we listen to our operators as much as anything,” Dennis Taylor, superintendent at Cummins adds. “These pavers have consistently shown their value for us.”
Not only did they win the 2021 OAPA Full-Depth award, they also won for Rural Overlay for US-412 in Woodward County and Urban Overlay for SH-3 in Blaine County. They were chosen as Runners-Up in two other categories as well.
“The BOMAG screeds lay down a great mat and our crews are very conscientious about making sure every job is done to the best of their abilities,” Sharp says. “We are always trying to stay current with the trends in the industry and the BOMAG machines keep up. We upgrade our operations to stay ahead of our competition and to keep our crews operating at peak performance.”