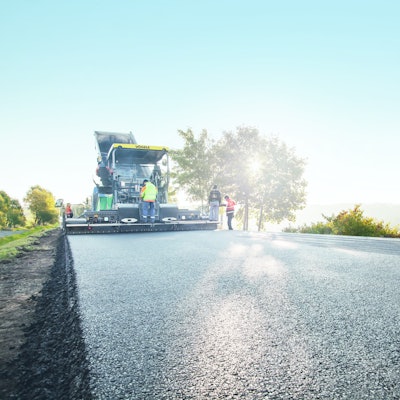
While the paver and rollers are essential to asphalt paving operations, the screed is crucial for both the quality and density of an asphalt road. With this in mind, owners should choose a screed that not only matches their paving program but also includes new features that improve the entire lifecycle of the pavement.
“Improvements in both pavers and screeds have led to increases in quality in the Superpave era of performance-graded asphalt pavements, and screeds with pre-compaction are part of it,” Laikram "Nars" Narsingh, manager, commercial support and development with Vögele says. “The quality of today’s asphalt surface is much smoother, with an overall improvement in surface texture consistency and joint quality. Also, the deterioration of the surface now takes much longer, due to improved paving processes such as reduced mass and temperature segregation and higher joint density.”
The Screed & Pre-Compaction
Upgrades in screed technology help crews achieve the highest pre-compaction right behind the paver where it matters most – when temperatures are at their highest.
Pre-compaction can be defined as the density achieved only by the screed, prior to rolling. The initial turnover and seating of the aggregate in the mix by the screed structurally places the material and provides initial smoothness. During this process, air is driven out of the mix to initiate the process of achieving density.
“As material flows under the screed, air is squeezed out of the mixture as density changes to what we call ‘off the screed density’,” says John Mooney, paver product manager at Volvo Construction Equipment. “The weight of the screed and vibratory excitement of the material will produce roughly 85% or better material density right off the screed. The rollers will then provide another 5% to 12% reduction in air voids.”
So it’s important to maximize pre-compaction with the paver and screed to achieve greater density in the finished mat – which results in a longer-lasting pavement. Maximizing pre-compaction also reduces the number of required rolling passes needed, which leads to reduced wear and tear on the rollers, lower operating costs and increased production throughout the job.
“In general, more than one adjustment is typically needed to increase pre-compaction,” says Jon Anderson, global sales consultant at Caterpillar Inc. “It is usually a combination of settings and/or configurations. Increasing screed weight, increasing amplitude (stroke) of the tamper bar, or decreasing paving speed are all inputs; however these need to be adjusted per the job parameters, always making sure to keep mat quality acceptable.”
Paving Speed Matters
Generally there are three compaction compoents available on paver screeds:
1) Vibratory-only Screed
2) Vibratory and Tamper Bar (single & dual) Screed
3) Vibratory, Tamper and Pressure Bar Screed
“The selection of the type of pre-compaction element varies based on material being laid down, thickness, quality/density specification requirements and type of job being done such as mainline paving, airports, container terminals etc.,” says Vijayakumar Palanisamy, product marketing manager for Dynapac.
In the United States, many contractors use vibratory-only screeds for their paving needs as they are equipped to pave at higher speeds and in the lift thickness required by most DOTs.
“The vibratory-only screed operates at zero to 3,000 vibrations per minute,” says Tom Travers, sales and marketing manager with Carlson Paving. “On the slow side, you can pave 35 fpm and up to 60 fpm with a vibratory only screed.”
Vibratory-only screeds have an eccentric shaft acting on screed plates at right angles to the direction of paving causing the "V" screed to vibrate. The heavier the eccentric weight, the more effective the vibration system will be.
The compactive force of the vibratory-only screed is generated by offset weights as they spin around the central shaft and applied to the hot mix as it passes under the screed.
Some screeds also have tamper bars that strike off the hot mix as it passes under the screed to provide more initial density. However, adding a tamper requires the paving speed to drastically slow down so that the tamper bar has enough time to tuck the material under the screed.
The addition of a pressure bar gives additional weight on top of the screed plate providing further pre-compaction, but will also impact paving speed and cannot be used on thinner lifts.
“A pressure bar compacts the mat after the screed trailing edge,” Anderson says. “It helps add some additional compaction before the asphalt compactor. Dual tamper bar screeds will also help increase pre-compaction over single tamper bar screed, however increasing screed weight in conjunction with the second tamper bar is key to increasing overall compaction.” (see Heavy Hitters sidebar)
“The dynamic effort is determined by the use of any one pre-compaction element [vibration, tampers and pressure bars],” Palanisamy says. “Manufacturers pay close attention to the balance of the paver and screed weight to ensure proper paving results. When the screed weight cannot be increased any further, technologies like the tamper and pressure bars help to further increase the pre-compaction effort. The analogy is similar to having static roller versus vibratory roller.”
While pre-compaction is important, asphalt contractors should always remember that smoothness, texture, mat profile and minimizing aggregate segregation are all critical in creating a high quality and long-lasting asphalt mat. Other screed elements can help in achieving those.
Achieving the Smooth Ride
Though the principle of the free-floating screed has remained unchanged since inception, screed mat quality has improved for a number of reasons.
Electric Heat:
At the start of a paving shift, the screed is much colder than the mix being laid. To keep the asphalt from sticking to the screed, it must be heated.
“Prior to its introduction, nearly all screeds in North America utilized fossil fuel burners to heat the screed plates,” Travers says. “The usage of fossil fuel heat, while cheap and readily available, had serious draw backs including uneven heat that lead to warping of screed plates, smoke and fumes, and constant maintenance. By the mid-1990s electric heat began to be introduced, utilizing electric heating elements in direct contact with the upper surface of the screed plate.”
The heating elements are placed above the screed plate to help heat the screed uniformly without hot spots.
“The benefit to new heating elements integrated in screeds today means longer lifecycle and more even heating,” Travers says. “New elements reduce maintenance in the long run, lowering the cost per operating hour of the screed platform.”
Head of Material Control:
The head of material is the depth of material being evenly spread in front of the screed by the auger. Controlling this is the most important factor in laying a smooth mat.
“The road building industry recognizes that the leading cause of future road surface failures can be directed back to poor head of material control,” Mooney explains. “In best practices, industry professionals all teach that the amount of material in front of the screed and extension must remain constant to deliver the best long-lasting mat.”
Material deflector plates and strategically positioned auger flights allow for better material consistency in front of the screed. Non-contact auger sensors and potentiometers (instead of flow gates) controlling material delivery to the augers -- coupled with digital display of the material height – give operators more control.
Paving Speed:
Nonstop paving at a uniform forward speed results in the highest quality and smoothest pavements and should be the goal of every paving crew.
“Quick starts and stops will take the screed out of balance causing it to rise and fall,” Narsingh says. “If you increase the forward speed, the screed will drop, and if you slow down, a pile of material will appear in front of the screed and will pile up, causing the screed to climb.”
This can be eliminated by a hydraulic system that automatically holds the screed in the paving height when the paver stops to wait for asphalt delivery.
“This hydraulic lock keeps the screed from sinking in the mix due to its weight,” Mooney says. “Then when paving speed is returned, the lock or hold position must release over a short distance to prevent mat marking. This feature is very important on all pavers that expect to achieve IRI requirements for smoothness.”
Crew Comfort & Maintenance
While screeds have evolved over the past couple of decades, most of the new developments in screed design have been geared toward the service side. These include design changes that reduce the hours needed for preventative maintenance for the platforms, thereby lowering the cost per operating hour.
“Ease of operation has dramatically improved with recent technology,” Narsingh says. “This reduces operator tiredness, allowing him or her to perform more efficiently during long work days typical of the paving industry.”
“The screed is also a major source of noise, Palanisamy adds. “Having properly sound insulated screeds is of high importance to the operators and the environment. Furthermore, a low screed design helps the operators to have a good view on the amount of material in front of the screed and helps ensuring a good paving results.”