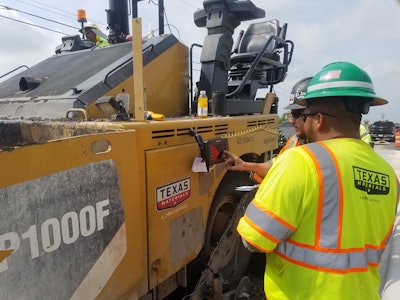
Managing your material costs is one of the most important things you can do as a project owner to manage expenses and material overruns can make or break your profit margin. This is why it’s important to properly calculate your yield so you know how much material you need in advance.
While having proper calculations in advance is necessary to control costs, technology today is allowing contractors to manage how much material they’re using in real-time so adjustments can be made to prevent costly overruns.
“One of the most important elements of the entire paving process is the one that is rarely openly discussed, yield control,” John Hood, owner of MultiFit LLC says. “Sure a tremendous amount of information has been discussed and made available regarding quality in pavements, from the design of the mixes, best practices regarding the paving and compaction processes and ways to address segregation of the mixes but rarely do we see any information regarding control of the amount of material utilized on a project.
“Frankly, material usage is one of the most important elements of any paving project for the sustainability of the paving company. Specification and smoothness bonuses are nice, but a company can directly address project costs, profitability and long-term sustainability of the organization by controlling material usage.”
Therefore Hood, an asphalt industry veteran, recognized the potential and secured exclusive U.S. distribution rights for the Mat Manager from TF Technologies of Fredensborg, Denmark.
“The Mat Manager product was developed to help contractors address and track actual material usage on individual and or collective paving projects in real time while the project is ongoing so corrections can be made during the project,” he says.
The Mat Manager System tracks planned material usage compared to actual material usage at every step of the project and displays the usage on the screen throughout the project. The paving crew compares the two for a real time evaluation throughout the job.
The crew knows exactly where the material consumption is throughout the process via the Mat Manager display home screen. The information displayed on the home screen allows the paving crew to address any material consumption issues during the paving process, greatly reducing excess material usage during the project and providing the ability to control planned material costs on the job.
Benefits of Real-Time Data
With the material usage information displayed throughout the project, the crew can make corrections to the process that might go unnoticed during the job. The simple, intuitive display is very easy to input the project criteria and the crew can be off and running.
“If the plan of the project were to pave a lane 12 feet wide and 2 inches thick, yet the actual pavement was being placed at 12 feet, 2 inches wide and 2-1/8 inches thick, a substantial amount of material over the planned amount would be used,” Hood says. “Actually nearly 60 tons of material over the planned amount would be used per lane mile at these simple overages. Based on the costs involved of materials and trucking alone the project costs can get out of control quickly.”
Rather than attempting to evaluate what went wrong after the project is complete and the damage is done to the profitability of the job, the Mat Manager provides the crew the ability to address the issues during the project and in real-time.
Not only is the information available on the Mat Manager display in real-time, the data is available to upload to the online Mat Wiser Analytical software system. The Mat Wiser provides a user interface to view the project data in a summary as well as multiple additional analytical reports including full statistics regarding the entire paving operation. All project criteria are available to view via the summary.
Key information such as paving speed and trucking requirements are recorded and displayed in the Mat Wiser. Information such as a map of the project is also available to review which shows loads, stops and GPS locations for validation and verification purposes.
“One very effective element of the analytics is that an efficient paving time and overall efficiency of the operation is provided,” Hood says. “These are key visuals to address improvement of the operation, not just the paving crew but trucking, material logistics, stops, etc. “The best way to improve the process in to accurately measure it and overall operating efficiency can be improved by reviewing this data.”
The Mat Manager system is connected to the machine via a hard-wired network of sensors that feed pertinent information to the Mat Manager operating display. The display is generally removed daily, but the sensors always remain on the machine. The display simply plugs in each morning prior to the beginning of the paving process in less than two minutes.
Hood says the initial installation process generally takes approximately four to six hours on most paving machines. The company also offers a comprehensive training process for the system which can vary in time, but generally takes about three to four hours to complete.