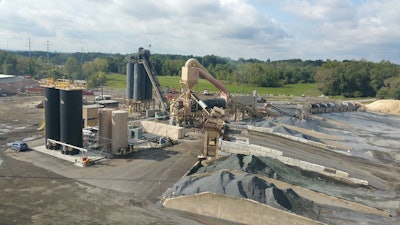
Changing your plant configuration is not a decision you take lightly. Not only is buying new equipment costly, but any lapse in production means you’re also not making any money. However, when your plant is no longer producing to a level that keeps you competitive, it’s time to make a change.
Laurel Asphalt, located in Laurel, MD, owns and operates two asphalt plants that cater to the small contractor as well as large, and is certified to produce materials for the State of Maryland and all surrounding counties.
Their location in Laurel, MD was a 3-ton batch plant dating back to the 1970’s and was starting to cause challenges for the company.
“Over the years, Laurel had changed components on the plant, but the general guys on it dated back to the 70's," Chris Rumer, General Manager of Laurel Asphalt says. “The plant had been letting the company now and some major costly repairs were needed."
Laurel Asphalt operates in the cold Maryland climate and they were trying to squeeze as much as they could from this plant during the short paving season, putting a lot of wear and tear on an already worn out plant.
"We really needed to increase our capabilities," Rumer says. "We had a very hard time running to meet our customer needs and demands. Plant parts were getting harder and harder to find just to fix the old components of the plant."
Plus, Rumer says the crew was sometimes required to work 16 hours a day to get the material out the door and repair the plant, driving up costs and frustration.
“The company took down their aging plant components,” David Garrett, sales manager with Meeker Equipment says. “Laurel Asphalt chose Meeker Equipment Company to replace the aging Dryer with a new one. They also added a mixing drum which gave them the increased capabilities they were looking for.”
Today, after a three-month overhaul, the company is now able to produce material consistently and reliably with less time spent fixing problems so more time can spent making material for their customers.
Component Overhaul
While the plant overhaul included new storage for their increased production, replacing two old horizontal storage tanks with two vertical tanks, they also needed to overhaul their electrical and plant controls.
The company completely upgraded their electric service coming into a new control room and replaced all of their motor controls with a new motor control center.
“Laurel had a lot of challenges with their electric, it was very old.” Garrett says. “They added an unloading pump, asphalt metering skid, calibration tank and they installed new process controls and Liquid Vision for the valve control and tank monitoring.”
The Meeker Liquid Vision System was installed to help better control their production without having to manually switch the tanks.
“The Liquid Vision was installed with their actuator valves on the storage system,” Garrett says. “Now when they want to switch tanks from one liquid to the other, no one has to go out and manually turn a valve. The Liquid Vision controls the actuators so they select their tanks from the control room. They can also see the levels on all the tanks without having to go out to the tank farm.”
Laurel Asphalt also upgraded their process controls to a new Libra System. “The company still had their Libra Generation III Controls on their silos and they were using that to control their batch plant," Garrett says. "They upgraded to Plant Wise system based on their familiarity with the controls.”
Marrying Old with New
When you’re making upgrades, not every single component will be in need of an upgrade. This is where Laurel Asphalt encountered challenges during the switch.
“One of the things that’s always challenging is marrying the old with the new,” Garret says. “They put in a new dryer and a new mixing drum, but they reused their existing Hauck Burner. However, the new dryer had a RAP collar so we had to extend the nose on the existing burner in order for it to fit.”
The company used what they could while replacing what they wanted. They kept the baghouse, but changed the duct work. The drives on the cold feed bins were changed to be variable frequency drives, but the old bins and feeders are still there. They also extended the existing aggregate conveyor to feed a scalping screen and scale conveyor.
“In the past, the company didn’t have to weigh their aggregate and their RAP because it was going in to a batch plant,” Garret says. “With the new drum plant, they need to know what’s going in there so we had to add belt scales.”
Another challenge was working around those hard fixed points that the company did not want to have to move.
“They had existing silos and drag slats that we weren’t going to move,” Garret says. “So in that case, the discharge had to hit that point perfectly and on the other end, we didn’t change the RAP or the cold feed bins so all the materials coming in to the plant had to hit those perfectly too. You have all of these fixed points and you’re working in the middle trying to make it all fit back together and it all came together very nicely.”