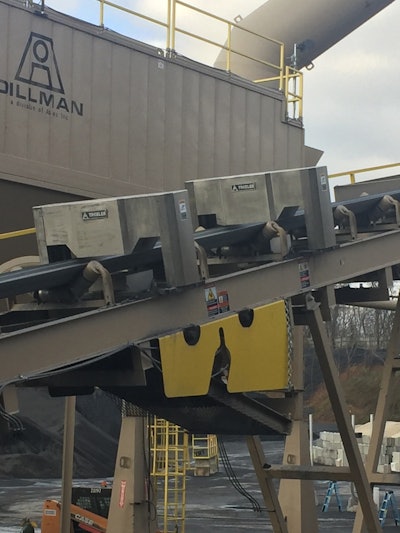
The eventual quality of the roads we drive on start with consistency and quality at the asphalt plant. Excessive moisture in the aggregates can lead to serious issues with the mix. Unless all your stockpiles are completely sheltered and your feeder systems are covered from the elements, moisture will impact your asphalt content.
To help combat these moisture issues more accurately, asphalt plants have started to install moisture measurement systems or MMS devices to help avoid mix deviation and maintain consistency.
“Deviations in asphalt content can lead to reduced payment and nobody wants that,” Michael Worden, vice president of quality control at Pennsy Supply says. “Deviations in stockpile moisture contents combined with other variations can substantially reduce accuracy.”
His company installed a MMS system in 2016 and has seen improved product quality ever since.
What is a MMS?
Using nuclear moisture and density technology, moisture measurement systems measure the moisture in an aggregate blend moving on the virgin aggregate conveyor belt. Unlike microwave probes that require contact with the material in the bin or in the stream of aggregates on the belt, the MMS is situated above the belt with the sources below the belt meaning there is no need to have physical contact with the aggregate mix or the belt.
"Before we installed our MMS, our technicians could only rely on the conventional method of using oven dried stockpile samples for obtaining and monitoring stockpile moisture contents,” Worden says.
The problem with this process is that it’s not only time consuming, taking a few hours each test, but it can be unreliable, especially after rain events, as readings are typically only taken two to three times a day.
“The current standard best practice for measuring stockpiles is very inefficient,” Worden says. “Techs have to get in their trucks, drive to the quarry, get a sample from each pile, bring that back and test it.”
On top of the time it takes to collect the samples, the information can be unreliable as once a sample is taken, that pile is already drying out, further changing the data.
“Your moisture can change throughout the day as piles are continually drying out and you have to be able to account for those changes during mix production,” Worden says.
With an MMS system, measurements can be taken every second. In an 8-hour day, you could get up to 30,000 measurements, dramatically increasing the likelihood of catching any significant changes in the moisture contents of your aggregates.
Improving Mix Consistency
The asphalt content of the asphalt mix produced in a drum plant is directly affected by how much moisture is in the aggregates.
“We know that better control of the moisture content in our aggregates directly impacts the asphalt content in our finished mix,” Worden says. “By better understanding these numbers, we can directly improve the consistency and quality of our mix.”
Therefore, it is crucial that the plant be given accurate moisture content for those aggregates about to go into the drum and the MMS does just that.
“If the moisture of your aggregates is higher than what you’ve entered into the plant’s controls, then you’re going to be evaporating away a greater mass of moisture than the plant is accounting for, and you’re going to have too high of an asphalt content in your finished mix,” Worden says. “Conversely, if the aggregate is dryer than what you’ve entered into the plant’s controls, you’re going to be under asphalting that mix.”
By taking these measurements more frequently, plant operators can better detect issues and control the quality and consistency of the mix.
“This device can help you better understand any deviations in moisture content, therefore improve quality,” Worden says. “The lower the standard deviations of your data, the more consistent the mix is, the higher the quality it is and you can’t maintain high quality without maintaining consistency.”
Worden says another unexpected benefit of the MMS device has been increased communication between the QC technicians and plant operators, so keeps them more highly engaged as a team.
“When we initially bought it, we thought we’d be saving time from not having to go out and test samples as often,” he says. “However, we’re now testing the samples more to verify the MMS is reading correctly. Our plant operator is also watching the MMS’s read-out like a hawk to make sure the moisture content readings are consistent, and is now able to immediately contact the technicians if there are any significant changes noted in moisture readings. That couldn’t happened before, as the plant operator could only rely on the two or three daily moisture contents given to them by the lab”
Driving Better Bonuses
Like any new system, the cost can hinder industry acceptance but Worden says that wasn’t going to keep them from trying it, especially with states adopting Percent Within Limit (PWL) specs for payment and bonus processing.
“Now that PWL seems to be the direction that most state agencies are going, you can be either penalized for high standard deviations or rewarded through bonuses for low standard deviations and asphalt content,” he says.
Lower standard deviations means increased consistency and increased consistency is one key to increased quality.
Since MMS devices can be fully integrated into the plant's control system for full automation plant manufacturers can write programming for the devices that can act as a failsafe if the MMS system were to ever fail.
“We wrote in our programming that if the MMS’s measured moisture contents drift too far from what’s expected, the plant will automatically default to the manually entered moisture content data determined by our daily stockpile moisture tests,” Worden says. “The system will alarm us if this happens, and we then work with the MMS manufacturer to get it back online.”