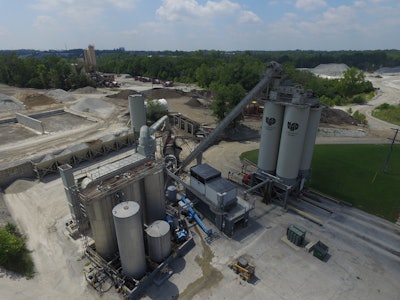
The way that asphalt plant companies do business is changing every day as the technologies to improve daily operations rapidly develop. While this presents opportunities it also brings challenges for plant owners who consistently want to improve their plants by retrofitting and upgrading their components.
Louisville Paving, a fourth-generation run asphalt company with nearly a 100-year history, knows all about adapting to thrive in the competitive Kentucky and Southern Indiana market. The company originally started as a coal delivery business for winter months and added asphalt paving to their services in the summer. Today they are a full service paver-producer with six locations and 65 years of experience in both highway and heavy construction.
Company president John Dougherty is always looking at forward technologies to advance his business operations. So he looked to upgrade their recently acquired Oldham County plant location and utilize new technologies in their existing Louisville and Bullitt County plant locations.
“The Oldham plant, as it existed, did not really meet the needs that Louisville Paving had, so they looked to modify this existing plant to get it up to the capacity and efficiency they needed for their future business as well as to be able to produce the quality of material they want to produce,” Steve Elam with Hotmix Parts/Stansteel says. “In order to accomplish this they used a variety of existing equipment while modifying and upgrading others.”
Always with a focus on producing quality mix, Louisville Paving knew they needed to invest in new control technologies to merge and marry these components.
Tank Troubles
As one can imagine upgrading multiple different components at one location tends to create issues which had not existed prior to the change. Dougherty found that he had a problematic liquid asphalt storage arrangement at this existing plant and thus chose to completely modify the system. The company also moved the location of the asphalt tank farm, made upgrades and applied advanced technology to their tank monitoring and operation.
The Oldham County plant was tasked with integrating a comprehensive control system for their tanks. They worked with Stansteel/Hotmix Parts to implement the Tank Tracker which is their new tank monitoring system.
Over 25 years ago, Hotmix Parts listened to customers who complained about costly plant downtime. The most frequent cause was the hot oil heater quitting overnight resulting in a cold plant. Hotmix Parts created a solution in a monitoring and alarm system called the NiteOwl Plant Alert System which continually monitors relevant components and then contacts the plant and/or management personnel whenever there is a problem. This system was extremely effective and is still a product that serves the industry and Louisville Paving well today.
So Hotmix Parts was ready when customers voiced distress over trying to manage more types of liquid asphalts - which required more tanks, and potentially more issues. All the while the cost of liquid asphalt escalated. Hotmix Parts committed to developing a tank and vessel monitoring system that would address these common problems.
Thus, the Tank Tracker was born.
However they decided to add this technology to other storage equipment including hotmix silos, dust or mineral filler silos, fuel tanks and additive tanks for anti-strip and rejuvenators.
Technology Improves Measurements
The measurement of hot liquid asphalt has certain challenges. Many plant personnel have to physically look into tanks and measure them. That involves climbing atop tanks and physically checking levels, looking into a dark and fume-emitting AC tank.
"The Tank Tracker has the ability to accurately measure and monitor the tank and silo levels in real time and at multiple remote locations,” Elam says. This means that plant operators, managers, accounting and even AC suppliers can see actual inventory levels 24/7. This is an incredible safety tool and time-saver. This real-time information available in the control room is expandable to be viewed remotely via smart phones, tablets and remote computers."
The Tank Tracker can monitor temperatures of the product in the tanks, silo and other vessels. The measuring technology is also non material contacting which means the service life is improved and it is a much safer and easier retrofit installation. The Tank Tracker has alarm configurations and will track alarm events. It can be added to one component or tank at a time as well as integrated into the Tank TrackerManagement System which can automate the entire tank switching and filling logistics process.
At Louisville Paving’s Avoca Quarry location, which is a high production facility, the plant operator, Lonnie Garrett, is particularly pleased with the silo inventory level application. Instead of just relying on the silo’s high/low indicators and speculating on the actual tonnage in the silo, Garrett has been able to accurately measure that quantity in real time. This confidence in the Tank (Silo) Tracker accuracy has enabled him to fill the silo further by approximately 15 tons or over half of a truck load and minimize waste as well.
The Tank (Silo) Tracker helps to better utilize the existing silo equipment they already have to be more productive both at the plant and on the roadway by better inventory management.
“Plant workers often have to “stick” the tank to measure the levels,” Elam says. “Not only may that not be as precise, it’s certainly an undesirable and time-consuming job which increases worker hazard exposure as well.”
Other methods of tank measurement include external tank measurement boards that have a float and provide an indication on the external tank. While they can work well they may not be fully maintained and can become inoperable. These are all individual visual readings that have to be communicated in some manual form at the plant level.
“Plants may have both horizontal and vertical asphalt tanks. When measuring a horizontal tank, one needs to be very precise because of the shape of the tank. Any vertical change is a fairly large volume of product, providing a greater margin of error to readings and thus incorrect inventory," Elam adds.
On top of all that, the tank and silo storage environment tends to be a very unfriendly and harsh environment. These harsh conditions can cause most measuring devices to either not perform properly, or fail prematurely. The Tank Tracker has been ruggedly and intelligently designed to overcome these problems.
By saving 30 minutes to an hour each day for plant personnel, this saves plant operations time while improving safety in the workplace. Having real time inventory information also helps delivery logistics for AC, accounting, processing and inventory management.
Better Material Management
Plant managers know that needing a precise measurement of AC levels is imperative to their day to day operations.
“Liquid asphalt is the most expensive component in the hotmix mixture itself, so managing inventory is both important for inventory cost management as well from a production and logistics perspective,” Elam says. “Since we don't have infinite storage at asphalt plants, we rely on timely deliveries of this product to meet our needs. The ability to monitor inventory more closely will provide critical information for proper planning and communication. Based on new electronic monitoring and reporting of AC Tanker Trucker hours their total hours are even more limited.”
The Tank Tracker can monitor up to eight asphalt plant components at one time and is fully expandable beyond that through a daisy chain of sensors. While the Tank Tracker was designed to monitor AC levels, it can also monitor any type of liquid or solid material such as hot mix silos, fuel, warm mix additives in smaller tanks, anti-strip, rejuvenators, etc. It will also indicate real time dust or lime silo levels accurately.
Tank Tracker technology, by removing the human element from measuring tank levels, has also drastically improved safety.
“With the Tank Tracker, ground personnel and plant personnel don't have to deal with fumes or climbing onto tanks for measurements,” Elam says. “Many companies, because of the increased danger and liability, are trying to minimize the need and type of access for getting on equipment. Obviously not routinely climbing on the tanks cuts down on personnel exposure.”
Louisville Paving recognized that the Tank Tracker, in its simplest form, as a valuable tool to save plant personnel time while increasing safety. It can also be incrementally expanded all the way to a very sophisticated Asphalt Tank Farm Management System to select tanks automatically, monitor a multitude of product inventory and temperature levels, provide offsite viewing and operation and, all the while, improve plant safety and productivity.