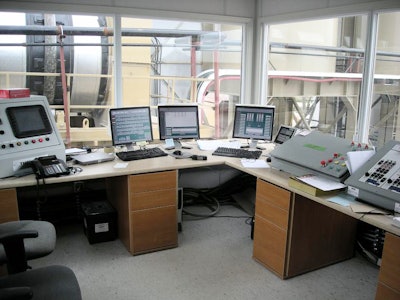
Implementing technology at your asphalt plant is really no longer an option but a necessity to keep your operations running smoothly and your customers happy. Automation control systems help streamline everything from ticketing to mix quality and plant owners can’t afford to skip this technology.
“Technology is changing at such a rapid pace with new automation processes happening everywhere in the world and the asphalt industry is by no means immune to that,” Ted Christian strategic account manager with WEM Automation says. “We face the same challenges and needs to adapt as any other industry out there. Those producers who embrace this mindset and understand it are going to be far ahead from those who resist it.”
From the demands of a quality mix to the ever growing desire for sustainability, asphalt plants need to have every tool at their disposal to reduce costs and grow profits.
Improving Plant Efficiencies
Since plant control systems were introduced nearly two decades ago, their use has evolved drastically. What they were mainly designed for however, to improve plant operations, has remained constant.
“Automation has already significantly improved plant efficiencies over the last two decades but there are always new features being developed,” Pierre Vidaillac group CEO at MINDS, Inc. says. “As electronics and computers are more and more reliable, the downside effect of more sensors and other systems having an adverse effect on overall reliability is not an issue anymore.”
This means automation can help plant owners avoid any unforeseen errors that tend to occur with a complex system like an asphalt plant, preventing downtime and lost production capacity.
“Automation is “watching” the plant all the time, alarming the operator of potential issues before they become full-scale problems,” Ken Cardy, president of Libra Systems says. “Automation can track the run-time of each piece of equipment and alert the operator when preventative maintenance is due. By proactively maintaining the equipment (rather than waiting for it to fail), plant downtime is greatly minimized. The extensive use of graphics is also a key component, as the human brain can process information from a dynamic picture much faster than assimilating numbers.”
Plant controls also allow operators to get the most out of their plant and help ease the sometimes intense working conditions associated with a stressful plant environment.
“Operating an asphalt plant manually while achieving modern performance targets isn’t possible anymore,” Vidaillac says. “It isn’t just about human errors, but also about the capacity of a human brain to monitor and check so many variables and process values. Human errors are not totally prevented but automation systems act as an operator’s assistant.”
Regulations Drive Adoption
Speaking of modern performance targets, the requirements for meeting mix specifications and government benchmarks have become more stringent in the last decade as quality can be measured immediately during the paving process. While automation has already significantly improved plant efficiencies, increased regulatory initiatives are really what will drive the technology adoption as plant owners are being tasked with creating higher quality mixes.
“Today, we’re getting much faster feedback on the quality of the workmanship out on the jobsite,” Christian says. “Therefore the product needs to be on target going out the door and automation is critical to delivering consistent mix quality. You don’t have the time to make the corrections that you may have had in the past and the penalties for not meeting mix specs are only getting greater.”
Through automation, you can virtually guarantee achieving pay factor bonuses by knowing exactly what is going into your mix and at what rates.
“It is the main goal of the automation system to monitor and pilot the process of making asphalt to make sure it is as good as expected,” Vidaillac says. “In other words, if the raw material is good and if the process is good, the result will be good. By qualifying the process rather than waiting for sample analysis, a good automation system can detect faulty conditions and prevent the waste of hundreds of out of spec tons of asphalt.”
While obtaining data instantaneously is a huge asset, correcting those errors right away is an even larger asset of automation.
“Automation is not just about consistency, it’s about data,” Christian adds. “Any deviations that might occur that deter the mix quality can be caught right away. By using the data you’re receiving instantaneously from the plant automation, adjustments can be made immediately to correct errors from virtually anywhere.”
Protecting Plant Investment
The asphalt industry is notorious for not wanting to take on a lot of technology willingly both because of the lack of comfort with it and the costs owners associate with implementation. Manufacturers want plant owners and operators to see automation as protection for their investment and a way to increase profits.
“Resistance to change is a human condition for which our industry is not exempt,” Cardy says. “In addition to meeting with owners and demonstrating how automation can help their business, we refer them to other clients with similar circumstances. These clients are eager to testify about the benefits they realized after installing Libra automation. It is extremely compelling when other asphalt plant owners share the value and efficiencies they experienced.”
And when it comes to achieving those pay bonuses, can you really put a cost on quality?
“Automation leads to less waste, less operator mistakes, more compliance, the ability to control complex plant layouts, better mix quality and more,” Vidaillac says. “In fact justifying the current market cost of automation systems is not a question anymore as many production and mix specifications could simply not be achieved consistently otherwise.”
Of course with any type of technology, return on investment is dependent on the circumstance and what is being replaced, but Cardy says payback is often less than a year and as early as one week.
“Control systems are literally the central nervous system of an asphalt plant and in this capital-intensive business, the cost of the technology and automation is a very small part of the overall investment needed to produce a mix,” Christian adds. “The ROI or cost per ton to implement automation systems compared to the overall cost of an asphalt plant is literally pennies when you look at the life cycle of an automation control system.”
This lack of familiarity when it comes to cost vs benefit is really what deters implementation, Christian says.
“You look at how our industry has been a leader in adopting the use of drones for safety and greater inventory control, with this innovative use of technology it would seem that the next logical step would be to explore similar advancements in plant automation.”