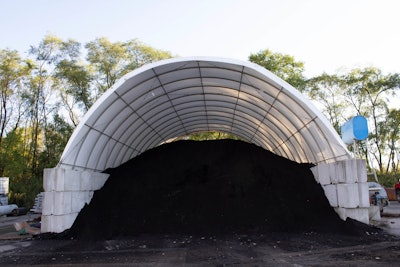
According to the Federal Highway Administration (FHWA), there are approximately 2.8 million miles of paved public roadways in the U.S. Out of all those miles, approximately 18 billion tons of asphalt mixes were used to pave them. And since 99% of all asphalt pavement material that is removed from an existing roadway is recycled back into infrastructure-related materials and products, the industry is presented with a huge opportunity.
The practice of using recycled asphalt pavement (RAP) in new asphalt mixtures has increased in recent years because of its economic and environmental benefits. This means the management of RAP is important because it holds many resources with high value to the end user such as oil and sometimes scarce aggregate types. If RAP is not managed properly, the value of this resource can be easily decreased.
With the increase in the amount of RAP used in modern mix designs, good RAP management practices need to be employed across the entire production and paving processes to ensure the greatest economic benefit from RAP along with the highest quality of recycled asphalt mix.
Mill it Up
Cold milling is an integral part of the construction cycle of any road. Asphalt milling is used to remove an old and worn wearing course or the entire asphalt pavement. It can also be used to improve the surface friction or remove ruts on a wearing course that is otherwise in good condition.
Once those asphalt millings are off the roadway, they become a recycled material that can be put back into future roads. However, best practices for milling should
The speed of the milling machine can make or break both the quantity and the quality of the material milled. In order to achieve a quality milled material, start and stop slowly. Starting too fast will make a dip right off the gate. When starting, move forward at a slow pace so the rear tracks can walk into the cut which allows the hydraulics for all legs to adjust accordingly. When stopping, slow down before coming to a complete stop.
LAUNCH: Interactive Guide to RAP Management
Also be sure to maintain a consistent speed when milling. Milling at high speeds puts unneeded wear on the machine and will create a coarse pattern. This also makes for larger RAP material, which means producers may have to run the material through a crusher before it’s used.
New machines have different drum speeds, which, of course, is different than machine speed. Running a machine in the highest drum speed at a lower machine speed will help achieve a fine texture quality, without the line spacing of a fine textured drum. This also makes for better sizing of RAP material.
Be sure to also mill surface and intermediate layers separately to help control quality.
Once asphalt millings are removed from the road surface, the contractor needs to find a place to store them until they can be reused.
Proper Storage Improves Quality
The transportation, storage and utilization of RAP is always a logistical challenge, but the single most important best practice is to treat RAP the same way you treat virgin materials. This means always keeping the RAP clean and dry before it’s reprocessed and put back on our roadways.
According to that National Asphalt Pavement Associations (NAPA) “Best Practices for RAP and RAS Management,” poor management of RAP stockpiles is commonly cited as a reason agencies are reluctant to increase allowable RAP contents in asphalt mixtures. For production of quality mixes with high RAP contents, excellent material management practices are essential.
When possible, store processed RAP stockpiles under cover, or at least in an area with a sloped surface and good drainage. NAPA recommends paving underneath stockpiles to allow for proper drainage.
Re-use of the RAP material is recommended within two to three month period of time. Longer storage periods may be expected when the material is under cover. Also, avoid driving loaders on RAP stockpiles, which leads to premature compaction of the processed RAP.
Importance of Material Classification
One practice that makes higher percentages of RAP more successful is fractionation of the material. A producer should separate the material into two or more stockpiles based on the size of the RAP particles. It's becoming more common to separate RAP into a coarse pile, with particles of more than ½ or 3/8-inch in size, and a fine pile with particles of ½-inch minus or so. That lets contractors use fine RAP in finer asphalt mixtures and coarse RAP in coarse mixtures.
The most widely used sizes are ½ x 0-inch to 5/8 x 0-inch, however some states also allow producers to used 3/4-minus RAP in subbase and binder.
Another best practice is to crush only what you need for a two- to three-month period since stockpiles of crushed and classified RAP have a short lifespan. After this timeframe, the RAP will begin to gather moisture and re-bond to itself which will result in large chunks and further processing needed before it can be used in the asphalt plant.
Once milled asphalt is crushed and reclassified by size, the asphalt producer can use the recycled material in its new asphalt mixes. This helps the producer save money on new raw aggregate products, as well on purchase of asphalt cement.
Producing High RAP Mixes
There have been few changes in the mix design procedures of recycled mixtures since hot-mix recycling began to become popular in the mid-1970s. However, recycling asphalt pavement back into hot mix asphalt requires some modifications in engineering and process control since another material is being added to the mixture.
Only 99% of pavements are recycled today and rejuvenators present an opportunity the industry is missing. Rejuvenators can help mix producers to reuse RAP in higher value, mix applications and not just base fill as today. Learn more: https://s3.amazonaws.com/creative.acbusinessmedia.com/ACON/managing-your-rap/index.html
A step-by-step mix design process for recycled mixtures is presented in NCHRP Report No. 452. This method follows the Superpave method of mix design, but could easily be adapted to any mix design procedure. As stated by McDaniel and Anderson (2001), the only changes in mix design from an all virgin mix are:
1. Heating the RAP more gradually and to a lower temperature than aggregates are normally heated.
2. Estimating the RAP aggregate specific gravity.
3. Accounting for the RAP binder in the aggregate batching.
4. Reducing the new binder content to account for the RAP binder.
5. Possibly using a lower virgin binder grade or a high-performance rejuvenator to account for the RAP binder aging.
Additives and polymer modifiers are often used to improve the high-temperature properties of asphalt and partnering with different industry experts is essential to make high RAP mixes successful for both heavy-highway and commercial customers.
And while only 99% of pavements are recycled today, rejuvenators present an opportunity the industry is missing. Rejuvenators can help mix producers to reuse RAP in higher value, mix applications and not just base fill as today.
Keep in mind, mixtures with RAP contents exceeding 25% normally may require changes in testing and plant operations. Work with your additive suppliers to determine the best path forward.
Working with the state department of transportation, state asphalt pavement association, municipalities and industry suppliers is essential to bring new technologies to the market that will yield long lasting, sustainable pavements.
View Next: 360-Plant Virtual Tour with Interactive Footage
Pave to Perfection
Once a high quality RAP mix is produced, it’s up to the paving contractors to lay it down. If a RAP mixture is produced correctly, contractors should not have to change their paving process in any way. What they will see is a mix that works well, compacts well and doesn’t give them any difficulty.
State RAP usage rates vary from about 10% to 35%, with the average calling for a mix involving 4 parts virgin material and 1 part recycled material. If we double the amount of recycled materials in the mix, you can double the associated cost savings as well. When this ideal balance is achieved, we not only reduce our environmental impact, we also save money.