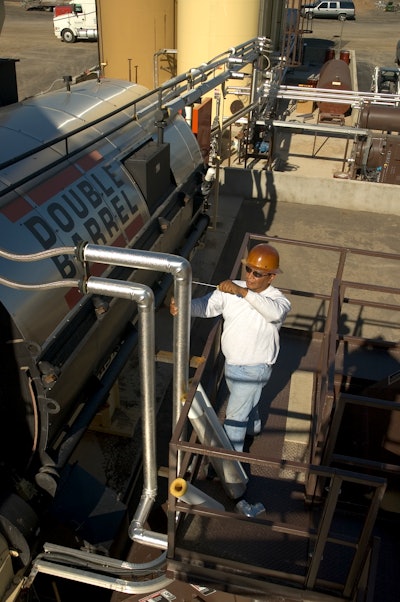
During the winter months, your company should be optimizing plant downtime by completing a myriad of preventative maintenance tasks. A winter repair regimen for asphalt plants consists of checking on those 'trouble spots' that have accumulated over the course of the paving season that you know need to be addressed while business is slower.
Here are five key areas you should focus on during schedule downtime at your asphalt plant.
1. Check the Drum
The drum is the heart of your asphalt plant and this component should be checked on regular basis during the paving season. However, during schedule plant downtime, asphalt plant owners should make sure these service checks are completed on the drum:
- Check drum shell thickness for wear.
- Clean, check and tune the burner.
- Change oil in drive reducers.
- Check the baghouse to ensure bags are in good shape. Also ensure cleaning and fines-return systems are working properly.
- Check trunnions for excessive wear or uneven wear and check the bearings for excessive play.
If there is excessive wear or reduced thickness along the flighting or shell, the material should be replaced. Repair and replacement of these components will help minimize fuel consumption and maximize the life of the dryer shell. Specifically, the combustion flights can make a significant impact on both the fuel combustion efficiency and emissions.
The trunnions should also be repaired or replaced if they have experienced wear beyond the hardening point or have severe metal flaking.
2. Monitor Batcher/Silo System
The batcher and silo systems are two of the most important pieces of equipment on an AC plant when it comes to battling mix segregation and safely storing your mix.
The silo cone should be thickness-mapped on an annual basis, at a minimum, and perhaps more depending on the amount of tonnage. Thickness gauge readings should be taken all along the length and circumference of the cone section and up the silo sidewalls, depending on how the silo is operated, how much it is filled and pulled down below the cone level on a daily basis. This measurement and mapping should be done for each silo on a routine basis to closely monitor how much wear has occurred.
Often, when a batcher unit has problems, its gates are chained open to ensure the job moves forward. HMA quality suffers, but the price of a shut-down for repairs to the batcher are deemed excessive and as long as the mix is accepted. With a little foresight, this whole scenario can be avoided by following these tips:
- Inspect the batcher's sides and cone for thin spots. Mark for any plating that may be required. Look closely at the gates and their pivots. Are they loose? Do they need to be greased? Mark for repairs any abnormalities you find.
- Examine the air actuation system. Failures here are the primary cause of batcher problems.
- Check the air cylinder(s) for excessive wear. Substandard air hoses should be slated for replacement.
- The same inspection protocol is used for the storage silos as for the batchers. Check the structural thickness, especially in the cone area. Mark any thin areas for repair or replacement.
3. Finesse the Dryer & Mixer
Entire articles could be written on the subject of dryer/mixer maintenance and dryer flighting and mixer tip condition is imperative for adequate aggregate moisture removal and thorough HMA blending.
Conditioning, showering and combustion flights need to be inspected for wear or damage. Replace or repair as needed. Inspect each and every flight and mixing tip for the following problems:
- Excessive wear
- Heat curling
- Impact bending
- Cracking or absence
Mark for replacement any flight that exhibits these problems. Obviously, any that are cracked can be welded, and those that are worn or missing must be replaced. Mixing tip wear needs to be evaluated periodically or when blending quality of the asphalt mix appears inadequate. These mixing tips are reversible to allow increased service life. Drum buildup removal should be performed in conjunction with rotating mixing tips (paddles).
4. Combustion System Tune-Up
The main burner and hot oil heaters make up your combustion system. Burner maintenance/cleaning and periodic tuning are important to utilize every BT) the fuel has available. Test, evaluate and tune your burner as needed to optimize performance. Having a properly running burner can also help to stay within State and Federal EPA guidelines. To do this:
- Examine all fuel and propane lines. Schedule for replacement any that raise a question in your mind.
- Look at the propane bottle for signs of leakage or damage.
- Check the fuel pump and drive mechanism.
- Mark any frayed belts, worn couplers or leaking seals.
- Schedule the fuel filters for replacement, regardless of how long they've been in place.
- Check the piping and valving from the supply tank.
- Verify that shut-offs do, in fact, work. Don't take them for granted, it may come back to haunt you.
- Inspect the tank's filling apparatus. Note any leaks or unsafe conditions.
The maintenance on these burners will depend on your fuel type. If you are burning a fuel oil or gas, you will want to inspect and clean the fuel delivery system. This would also be the time for an inspection and cleaning of the pilot assembly and burner nozzles. If equipped with electric heat for your hot oil, you will need to confirm your electrical connections and controllers are working properly.
5. Solidify Screening System
Scalping screens are vital in removing (rejecting) oversized aggregate for both batch and continuous mix asphalt plants. To verify that your screening system is up to par, follow these steps:
a. Start with an external inspection. Look for missing parts, such as lid hold-downs, and for signs of dust leaks. Look at the skirting seals under the units. Are they there or long gone? Examine the top covers. Are they worn out where they rest on the frame or other lids? All these conditions should be addressed.
b. Check to see that the screens move freely. If they don't, look for a buildup of aggregate under the drive end.
c. Check the size of the material. If it's a useable size that normally goes into a hot bin the accumulation could point to leaks in the oversize discharge, exacerbated by screen flooding and carry-over.
d. Remove all the lids and side covers. It's a good idea to take a hose and clean the accumulated fines off the screen frames and springs to makes it easier to find damaged and cracked components. Caution: Remember to open all the gates below and provide a way for the water to escape from under the plant. Once the unit is clean you should inspect it for broken springs and cracks in the framework.
e. Closely inspect each screen cloth. Look for excessive wear and broken wire.
f. Check the screen trays. Are they all tight? Is the screen cloth secure? It's good insurance to stock a complete change of screens. When stored in a custom-built rack on the screen deck, they are ready for installation with a minimum of fuss. Don't forget to keep a supply of the appropriate bolts handy.
g. Examine the screen drive and eccentric. Follow the manufacturer's recommendations as to periodic maintenance. In general, you should look for damaged components, worn sheaves or belts and broken motor mounts.
Proper plant maintenance can be instrumental to the performance of your plant next season, but it’s also important that you hire experienced plant personnel that are trained to spot warning signs for potential problems in plant components during the production season. Faulty parts on a plant can be costly if not addressed when first seen and can lead to troubles that are difficult to repair, even in the off season.
Remember, all maintenance actions should be performed in accordance with the manufacturer recommended procedures and intervals. Follow all OSHA Lockout/Tagout and confined space requirements prior to beginning any inspection or service on your plant.