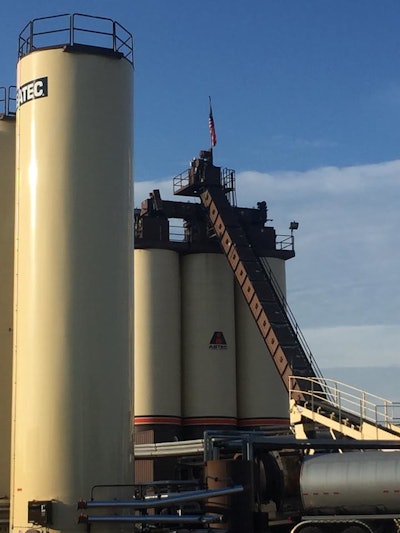
Heat Transfer Fluids (HTF) are designed and rated to maintain consistent temperatures for material movement throughout the asphalt plant. Problems occur when there is a sudden loss of fluid from the system causing it to shut down. Because delivery schedules need to be kept, some asphalt contractors will “top off” a system with any oil that happens to be on hand just to keep the operation moving. However, this is not a best practice and can be detreimental to your operation. Learn more from Paratherm sales engineer Steve Beward:
Q: What is the importance of a heat transfer fluid system to an asphalt plant?
A. This is the life blood of the process, it allows the liquid asphalt to stay liquid. Without proper care the heat transfer fluid can shut down the operation and impact cost
Q. If this system fails, what issues can occur at the asphalt plant?
A. Regarding heat transfer fluid related failures, the worst case would be fire. If carbon is allowed to build up on the walls of the heater coils, stress fractures can form on the coils and ultimately pinhole leaks can occur, allowing combustible fluid to leak into the firebox and can/will lead to a fire.
Failure to properly maintain the heat transfer fluid can also lead to piping blockages, pressure drops and flow issues in the process piping. Lack of maintenance can also interference with safety controls such as the low level switch in the expansion tank. All of these can impact safe and efficient operation and process uptime.
Q. What are ways plants can help prevent heat transfer system failure?
A. The best way to avoid failure of the heat transfer system at the asphalt plant is to perform annual fluid testing. This will monitor acid, viscosity and carbon buildup. Companies like Paratherm can provide corrective measures to prevent further buildup or help to reduce the sludge and carbon in the system.
Q. How can a hot oil fluid analysis help improve asphalt plant operations?
A. A hot fluid oil analysis can help improve efficiency by allowing the system to operate at the designed set temperature. Once the acid is allowed to increase, it is the main producer of carbon. As the carbon increases so does the viscosity. These increases make it difficult to keep the set temperature thus causing the operator to increase the set point and burning more fuel to the heater.
Don't Skimp On Quality...or Training
In asphalt plants with thermal oil heaters, safety and performance are greatly improved through proper maintenance. A program of routine checks keeps systems running at their best. This is why Beward says plant owners should be sure the following maintenance items are completed each year:
- Conduct an annual fluid analysis. Use a clear glass container and take the sample from a “live” part of the system such as a blow down valve on the Y-strainer or a low drain point. Allow a couple quarts to flow into a separate container; this will assure a representative sample. Then take the sample when the fluid is between 180° and 230° F. Examine the oil, look for particles suspended in the oil. Second, check the viscosity. Higher viscosities are produced when oil is oxidized or contaminated. Third, send the sample out for a fluid analysis.
- Keeping the Y strainer clean will prolong the life of your fluid charge, and help the system run smoothly.
- Use proper start-up and shut down procedures. To save on fuel costs, some plant owners shut down heaters at night, on weekends and during cold seasons. When starting up, bring the heater outlet gradually up to 200°F and then continue, up to operating temperature. This will avoid overheating the fluid. When shutting down leave the combustion air blower and the circulating pump running until the fluid temperature is down to 200° F
- Check insulation to see if it is wet with oil. Soaked insulation can spontaneously ignite. Using closed cell insulation or removing insulation altogether from potential leak points is recommended. Smoke is a sure sign that fluid is leaking.
- Check the low level switch to make sure it is functioning. Sludge can build up in the expansion tank causing the float switch to hang up. This can allow the system to continue to operate with a dry tank causing severe degradation of the fluid.
- Remove water by draining a small amount of fluid from the bottom of the expansion tank.
- Drain the catch container or Buffer tank. Never put oil found in the catch container back in the system.
- Check the stack temperature versus the heater outlet temperature. If the stack temperature is higher than normal, you either have soot buildup on the outside of the coils or coke buildup inside the coils.
Q. What are some other key maintenance issues plant owners should be aware of with their heat transfer system?
In asphalt plants with thermal oil heaters, safety and performance are greatly improved through proper maintenance. A program of routine checks keeps systems running at their best. This means you should not ignore leaks or smoke as leaking fluid can lead to catastrophic issues if not addressed immediately. Needing to add make up fluid is another indication that fluid is being lost somewhere in the process.
As a best practices, follow proper system start-up and shut down procedures to prolonging fluid lifetime. Routine observation of the system/operation, taking note of temperature set points and system pressures is also important. Changes in these conditions over time may indicate problems
Proper use of insulation – some parts of the system should not be insulated for both safety and fluid quality reasons
As a part of a comprehensive maintenance program, plant owners should make sure the following is done annually:
Q. What type of damage can a low-cost oil do to the transfer system?
A. Low-cost fluids, or fluids otherwise not explicitly designed for high temperature heat transfer systems can degrade prematurely, and/or foul heat transfer surfaces. Care should be taken to ensure a proper fluid is used that will maximize efficiency while meeting the demands of the application.
The damage that can be done to a system in the long term makes using low-cost oils a bad decision. Motor oil, turbine oil, hydraulic oil, R & O (Rust and Oxidation) lubricants and common base oils are simply not designed to perform under the continuous high operating temperatures of a heat transfer fluid system. These oils along with “multi-purpose oils” sold by some companies as HTFs can be unreliable because the additives in them are designed for the needs of other applications.
Q: What role does education and training have in preventing system downtime?
System operators, technicians etc. who have been trained on proper operation and maintenance of the heat transfer system will be better prepared to handle issues when they do arise. In addition, they will be aware of what to look for, listen for or otherwise be cognizant of if/when abnormal or upset conditions occur.
Ensure plant personnel are trained on the proper fluid to add to the system and ensure the fluid containers are clearly labelled and protected from contamination. If possible, dedicated equipment should be used when charging the system with fresh heat transfer fluid.
Knowledge of proper operation can help to recognize a problem early on, potentially preventing a shutdown scenario.