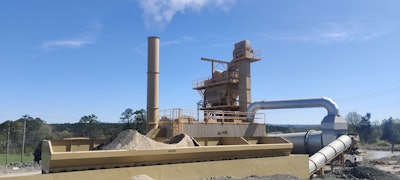
Since 1956, CA Langford has been providing Northern Alabama with aggregate materials from their Guntersville quarry. In the 1960’s, the company installed their first asphalt plant and purchased a White Manufacturing 2-ton batch plant in 1970’s. The company ran that plant for over 50 years until 2021 when they installed a brand new ALmix plant.
“We got very good at maintenance on that plant,” Scott Langford, president of CA Langford said. “The asphalt plant is a great compliment to our quarry and we wanted to be able to provide this service to our customers, but knew it was time for an upgrade.”
Initially, Langford thought the plant would only need a new mixer, screen and tower to make the plant operate more efficiently, but the more they investigated the component upgrades, the more they realized that a brand new plant would be a better investment.
“With the old plant, it was getting to the point where we were no longer able to find the support we needed to efficiently make repairs, parts just weren’t available,” Langford said. “Plus, you pick up the payment on a new plant when you look at downtime and last minute repairs. A new plant just became a no-brainer.”
By going with a new install, the company was also looking forward to finding support all in one place, instead of having to call on several different companies when they had an issue.
Sticking to Batch
The decision to continue with a batch plant instead of making the switch to a drum plant was not something CA Langford took lightly. Since their company supplies mix to many different companies in their area, the versatility of the batch plant made it the right choice.
“We looked at switching to a drum plant but we’ve always sold to different contractors, cities, counties etc. and wanted to be able to easily adapt to the needs of our customers,” Langford said. “With their scheduling, we might not know what customer is coming in and what mix they want at any given time. Batch plants are easier to get cranked up with different mix designs and without as much waste on the front end. We are able to run our customers a ton or two of the mix they need and then change it out to a different mix for another customer. If we have customers that like their mix with more fines, it’s very easy to tweak the mix.”
When looking to make a purchase, they turned to ALmix for support.
“ALmix still has a strong focus on the batch plant and the means to support them,” Langford said. “The concept of a batch plant hasn’t changed over the years but ALmix has added the technology to be able to tweak the mix easily while creating a more consistent product and keep it within the necessary specifications.”
Their new plant has five bins making it even easier for them to accommodate different mix types and the ability to switch from binder to seal to cold mix fairly easily. The technology from ALmix gives the plant operators detailed information about how much material is in each bin and detailed information to help prevent any issues that may happen during production.
“We're also able to run the batch plant just a little bit hotter which a lot of our customers like because most of the work they're doing is in driveways or small parking lots,” Langford says. “Our customers like the mix a little hotter for these projects for a better quality result.”
Support from the Start
Support was a big part of a new purchase for CA Langford and ALmix was on hand to help from the install to the training and beyond.
“ALmix did a great job designing the plant so that we were able to get a lot of it built ourselves,” Langford said. “We had poured the foundation and had about 80% of the plant up before they came on site, but we were glad to have them. We needed their help with the wiring and to get the plant inspected, calibrated and tuned to be sure it was set up correctly. They also helped us get the gas hooked up and made sure we had the proper regulators and valves.”
The crew at CA Langford was also used to using push button switches to operate the plant and relied on the ALmix team to get them up to speed on the computer operation of the system.
“It was a bit intimidating at first, but once you got it going, the system is very intuitive,” Langford said. “They made it operator friendly so that if you know how to run a batch plant, you can figure out how to run this one very easily. Their system makes it almost bullet proof that you’re not going to put a bad drop of asphalt out there.”
The ALmix team was onsite for nearly two months, ensuring the entire CA Langford team had the plant properly set up and felt comfortable with all aspects of operation.
Other Benefits to an Upgrade
Beyond the bonus of a more reliable plant, CA Langford has found the upgrade has given them many more benefits. The company, which produces around 25,000 tons of hot mix a year, has been impressed with the batch plant mixer and the level of consistency it provides.
“The mixer really allows us to customize those one-two ton drops for our customers,” Langford says. “The paddles provide a much better quality product than what we were used to.”
Upgraded belts, feeders and screens have also all made a difference in day to day operations.
“On the belt feeders, you are able to be put in gradation off the feeder,” Langford says. “Then the mix still goes through the dryer through the elevator and the bins. The mix is then segregated to pull out through each bin. This again helps us stay in spec and provide a more consistent mix very easily for our customers. I know I can put out a more uniform mix, day in and day out, with the upgrades ALmix provided with this install.”