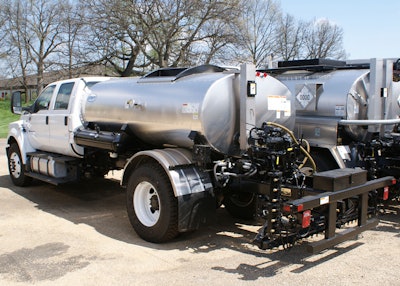
An asphalt distributor’s main job is to apply tack or bond coat to a road surface. When sprayed onto pavement, the treatment functions as a “glue” to hold existing and new pavement layers together. This enhances the bonding of individual pavement layers so they function as a single, unified pavement for improved strength and durability.
Therefore, a tack coat can significantly improve pavement strength, reduce surface-course sliding and reduce top-down cracking. However, if not done in a uniform way, that “glue” you’re putting down won’t develop into a proper bond. Here are three tips to help ensure you’re using, and getting the most out of, your asphalt distributor. Be sure to put the session Best Practices for Safety, Operations and Maintenance of Asphalt Distributors on your World of Asphalt calendar to learn more. The session will be held Thursday, March 8th at 7:30 a.m. during World of Asphalt in Indianapolis.
1. Training
As with any piece of equipment, having an operator that is properly trained is paramount to the success of the project. Not only do operators need to understand the machine they are working with in terms of proper nozzle selection, distributor speed and maintenance, they also need to know how the product they are putting down impacts the performance of the machine and the end-result of the job.
“Distributors in today's world are computer controlled to apply the selected application rate regardless of speed of the truck and spray width (within reason),” Brian Horner, region manager at E.D. Etnyre says. “So the main issue we see on jobs with distributors is that operators do not fully understand the products that are being applied and how to handle them. These products have changed a lot in the past few years and need to be handled differently than in the past.”
Horner says the temperature requirements of the materials will depend on the product being used.
“Product temp is very important to getting the material to circulate and spray properly,” Horner says. “And since the proper temperature range can vary from 150° F to 400° F, it’s important for operators to know what temperature the material needs to be at and keep an eye on it on the machine.
“Distributors have two thermometers to check temperature, one in the belly or low point that displays in the cab and rear control boxes, and another one on the side of the tank. All distributors have a heating system either LPG or diesel fired. Optional electric belly heat is also a great idea if you are keeping material in the tank for extended periods of time.”
2. Proper Maintenance
Like any machine, asphalt distributors need to stay well maintained and checked regularly for calibration in order to work properly. Horner says these are simple tests on the job site to assure application rate is correct (ex: measuring stick, measured shots, longitude tests or weight tests).
Having a clean machine is also key to proper machine performance.
“A clean distributor is a happy distributor,” Horner says. “Cleaning distributors is a process that needs daily attention. Over spray can build up on the bar and valves which will affect the working components of the unit. Many customers are now dry ice blasting their machines to clean them which basically is sand blasting the machine but with dry ice. This freezes the asphalt and causes it to flake off which results in no damage to wires or hoses.”
Proper nozzle alignment is another part of machine maintenance and performance.
“Nozzles are made of brass and tack is a petroleum-based product so they will spray millions of gallons before replacement is needed,” Horner says, but they need to be properly aligned to ensure uniform application.
“Nozzles are aligned in the bar at a 30° angle to achieve triple overlap application and this must be maintained to get the correct coverage of the product,” Horner says.
3. Safety
Asphalt distributors can be potentially dangerous as they are made to heat up and disperse materials up to 400° F. This is why keeping safety top of mind is an important best practice when working with these machines.
“Safety if a huge concern around a distributor,” Horner says. “Operators and personnel around the unit should be familiar with the product being sprayed and what to do if the product is spilled or you get some on your skin. The hotter the product the more danger.”
Horner says the other main safety issue is understanding how a distributor needs to be cleaned out or flushed if different products are going to be used in the unit.
“Safe operation of the burners to heat the product, temperature you are trying to achieve, amount of material in the tank so you can safely heat and the fuels being used for heating the machine all need to be communicated in order to ensure safe operation,” Horner concludes.