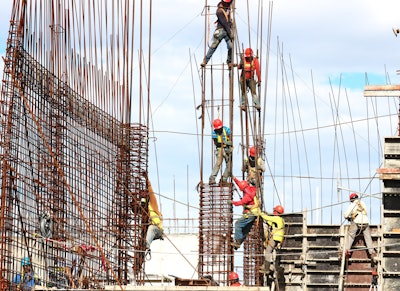
The construction industry is a dangerous place. This is why companies have made safety their priority, implementing procedures and technology that continually helps to protect their workers. The problem is that worker adoption of safety practices is low and even the most complex safety programs in the world are of little to no use if employees don't buy in and see the value.
If you are like most employees, you've probably undergone some form of safety training that you found silly. If so, maybe your mindset was part of the problem. A new study by McKinsey identifies the five mind-sets are particularly pervasive in organizations that struggle to improve their safety outcomes.
1. "Reporting an Incident will Cause Punishment"
In attempts to keep employees from getting hurt, management establishes safety rules and sanctions for breaching them. However, one of the unintended consequences of doing so is that employees may end up underreporting noteworthy incidents for fear of being penalized. When incidents aren’t reported, management and workers lose the opportunity to learn from near misses and low-severity events.
McKinsey reported that at a large transportation company, more than 60 percent of surveyed employees expressed concern about the consequences of reporting an injury. Upon joining field teams, new employees learn both from peers and supervisors the difference between a “true injury” and a “bruise”: the former should be reported and the latter should not. The message is clear—regardless of what these employees learned in their training sessions, it is best not to report too many incidents.
To reverse this mindset, involve the workforce in determining how infractions are treated. This can help employees perceive penalties as appropriate. Second, and even more critical, create an environment in which employees are immediately rewarded or recognized for making safe behaviors and reporting incidents or near misses. This environment encourages reporting and gets people talking about not only unsafe acts to avoid but also desired behaviors.
2. "Safety is Not My Job"
In organizations that struggle to improve their safety performance, the lack of empowerment is often felt by employees. It’s apparent in leaders who say that if employees followed the rules, they wouldn’t get injured; in team members who claim that incident rates would decrease if management invested in new equipment; and in safety specialists who complain that no one listens to their advice.
To increase employee empowerment, organizations can take a “managed” approach to safety as opposed to “regulated”. That is, management can trust employees to use their own judgment in instances when strict compliance with safety rules either wouldn’t be enough to ensure safety or could introduce risk. This approach is most important in environments with significant variations in operational conditions, which is often the case in industrial settings. To overcome employees feeling like they have no control over safety, it is also important for leaders to provide positive feedback to teams that take it upon themselves to improve safety.
More thorough investigations can discover potential factors behind the bad decision which caused the incident, such as fatigue or distraction. An even better approach takes a broader look at causes of injuries and incidents to identify structural levers that managers can use to make better decisions.
3. "Being Safe Means Being Less Productive"
Safety and productivity are often perceived as antagonists. Most employees come to work to “get things done” and feel satisfied when they hit their targets. Unless management signals that safety is the priority, employees may conclude that it is acceptable to focus on productivity at the expense of safety.
One way to combat this issue is for leaders to develop clear safety standards that take existing processes into account while integrating safety and productivity requirements. When these dueling processes aren’t integrated, employees can sometimes end up juggling incompatible requirements as they try to do their work.
4. "Injury is Part of the Job"
A review of a European basic-materials manufacturer’s safety culture revealed that the company had a high tolerance for risk. Some operators said that 100 percent safety was impossible and that risk was part of the job. A maintenance operator explained that he sustained cuts and bruises on the job regularly but didn’t report them because he considered them normal.
For most employees, having a "zero safety incident" precedent creates a learned tolerance to risk. If employees don't believe this goal is achievable, they give up on it and focused their efforts elsewhere. Make sure you set clear safety goals and communicate them often and effectively. With the right context established, people will commit to the goals and generally exceeded them.
5. "Safety Isn't a Priority"
Change doesn't happen overnight, but when it comes to a life or death situation, it should. A change in perspective can have a big impact like when a manager has to inform a family that a loved one died in a work-related accident. Those managers are likely to start talking about safety with a greater sense of urgency. However, managers can’t and shouldn’t wait for this kind of event to find personal meaning. Managers should work to find their own reason for why safety is important to them and their company, and it’s this perspective that would make them an effective promoter of change.
By identifying these mind-sets and harnessing approaches to overcome them, companies can achieve rapid, sustained change when it comes to safety adoption.