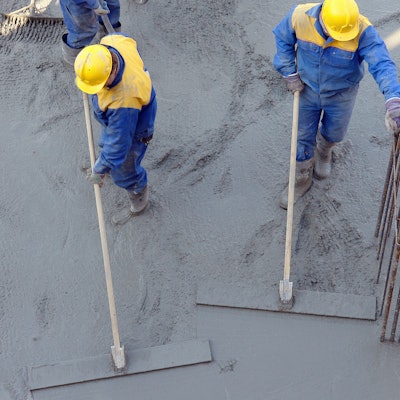
No matter what trade your construction crews perform, you want everyone to install things the same way. When you don’t have standardized field installation systems for crews to follow, each worker will do things the best way they think is right for the situation. And when five different workers install materials five different ways, your production rates will vary and you won’t be able to predict how long it takes to do the work. This won’t allow you to price and estimate work accurately, and therefore eventually cause you to lose money.
Get everyone on the same page
To build an efficient field operation that completes work per the quality you want within the budget allotted for the work, you need standardized systems and procedures for the crew to follow. Having a company standard for work you repeatedly perform in the field will ensure everyone does things the same way.
When every crew member installs things the same way, your crew will improve their speed and field efficiency. This will improve the productivity rate, standardize your cost estimating variances, and give you a training tool to use with every worker on every job.
Years ago we had our own concrete crews with foremen responsible to get their projects built per the plans and estimated budget with their respective crews. As our company grew, we hired more foreman and added more workers.
But as we grew, our quality problems increased. Slab edge cracks and flaking became prevalent on many of our projects. Some structural embeds and bolts were not always installed in the right place in the foundations. And on some jobs, the slab edge was slightly buckled and not built in a true straight line.
We determined that each foreman was building their concrete work the best they knew how based on their past experience and former company training instead of per our company standards and level of quality we expected.
Decide how your company builds
If a concrete contractor who installs footings and building slabs on a regular basis allows each foreman to decide for themselves how to form concrete slabs, each project will be built differently and have potential problems. To solve this challenge, we had to ask ourselves questions and determine which way we wanted to build our projects.
- Should the slab edge form stakes be installed at two feet on center?
- Does the slab thickness matter?
- How often should we brace the stakes with another kicker stake?
- How many nails should the form stake be nailed with?
- Should the crew oil the forms right before they pour concrete or 24 hours in advance?
- What about using a thickened edge or adding slab dowels to reduce cracking?
- How far apart should we install expansion joints?
- Should our expansion joints be cold joints, soft-cut into wet concrete or troweled into the curing concrete?
Lots of things to think about just to pour a simple slab on grade!
For example, concrete contractors want to make sure that footings are installed in the right location with the correct structural embeds at the right height. They also want to reduce to potential for concrete slabs to crack. Standard systems can eliminate these major potential costly problems.
Start by asking each of your foremen to identify a potential problem or quality issue that can occur in your field operation you want to fix and eliminate.
Get your team involved
For each of the standard field installation systems you want to create, get a small team of foreman and lead tradesman together and ask them to come up with the best solution for each area you want to standardize. After they agree on the best method to use, draft a detailed picture of the final approved company standard for this work operation.
As you continue to develop more systems to use in your company, compile them together in a field notebook of how your company builds your work product. I recommend you assign the task of organizing and keeping these systems to an office person or project engineer who can draft them into a clear detailed one page standardized format and placed into company field notebooks for the foreman to use and refer to in the field.
To make sure these company standards are being followed, you’ll need to dedicate time to train your foreman and crews. Hold field training meetings at least once a month and review a few of these systems on an ongoing basis to teach and enforce the company-wide standards.
George Hedley CPBC is a certified professional construction BIZCOACH and popular speaker. He helps contractors build better businesses, grow, increase profits, develop management teams, improve field production, and get their companies to work. He is the best-selling author of “Get Your Construction Business To Always Make A Profit!” available on Amazon.com. To get his free e-newsletter, start a personalized BIZCOACH program, attend a BIZ-BUILDER Wealthy Contractor Boot Camp, or get a discount at www.HardhatBIZSCHOOL.com online university for contractors, Visit www.HardhatPresentations.com or E-mail [email protected].