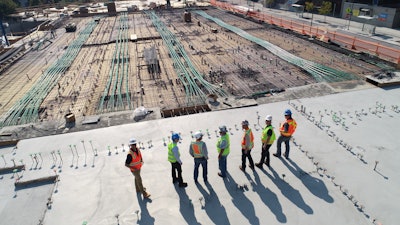
Construction risk management is a process of identifying and evaluating the unique risks that each project presents. Crucial to the evaluation is developing methods to mitigate the impact of risks to the project, your business’s, success. Here are the macro risks that all of construction faces in 2022.
Satisfying contract requirements, ensuring workers' safety, securing materials or dealing with natural calamities are growing risks that make construction risk management a requirement for any contractor. Rising expenses and increasingly complex projects in the context of an ongoing pandemic raise the stakes on creating detailed processes in advance to help detect worsening trends and action plans to help turn them around.
Basic risks at the construction site
To create your risk plan, you'll need to first figure out which elements are most likely to threaten your initiatives. The following are some of the most common sources of construction-related risks:
- Safety Risk: Any dangers or hazards on the job site that could result in worker injuries
- Financial Risk: Factors that affect your cash flow such as declining sales, economic issues, unanticipated cost increases, and heightened competition
- Legal Risk: Potential legal issues over contract compliance
- Project Risk: Project hazards such as poor resource management, time underestimation, absence of proper policies, or misunderstanding of project deliverables
- Natural disasters: Floods, earthquakes, and other natural disasters that can devastate construction sites and render work inaccessible.
How to manage risks
The process for developing a risk management plan is divided into the steps:
- Identify the hazards: Risks should be identified during preconstruction to allow time to plan for them before they are accepted.
- Prioritize dangers in order of importance: Risks should be prioritized based on their potential consequences to your organization, and the likelihood of their occurring
- Decide on a reaction strategy: Devise a response strategy for each risk.
- Choose members of the team to involve: The design team, owner team, and contractor team are the three essential participants in the construction process. It's critical to investigate their procedures and, where possible, identify and eliminate hazards.
- Create contingencies and revise: For risks you decide to accept, come up with a contingency plan – a backup strategy for completing the project if the hazard materializes.
Here are some examples of predictable dangers whose impact could be reduced with planning:
- Materials not delivered: Before contractors are hired, a different design might be produced, or bulk or specialized materials could be pre-ordered.
- Lack of qualified workers: This might be addressed by setting up a site labor camp or bringing in workers from other countries.
- Unavailable plant and equipment: Plants such as piling rig and spares could be ordered during the design phase, before engaging a contractor.
- Illness: This could be addressed by insurance coverage for critical staff.
- Failed information and communication technologies: Duplicating facilities, developing backup procedures, and maintaining uninterrupted power sources could all help to limit this risk.
- Power outage or a lack of water: Duplication of supplies, uninterrupted power sources, or the availability of standby generators could all help to lessen this risk.
Why is a contingency plan important?
In a real estate building project, there is a lot of pressure to finish on schedule, on budget, and to specified quality and craftsmanship standards. You need to ensure that the project's schedule and quality obligations are met. This is where construction contingency comes in. It's there to help the construction crew deal with the unexpected in an efficient and planned manner. All while sticking to tight deadlines and keeping high quality standards.
Even though everyone involved in project planning conducts a detailed analysis of what it will take to finish the project, numerous factors contribute to the need for contingencies, such as:
- Deadline
- Budget
- Timeline
- Design plan
- Resource schedule
In the event of unforeseen additions, the construction contingency serves as a form of an insurance policy. Having a construction contingency allows you to plan for the unforeseen, keeping your project on budget and on schedule.
The plan should include all forms of construction contingencies required for the project. Typically, a construction contingency account is set aside for 5% to 10% of the total building expenditure. A construction contingency budget should include a well-drafted method for accessing contingency funds, what situations do and do not necessitate the use of money. In addition to the actual monetary amount, it also outlines a clear system for notices, paperwork, and approvals.
Construction contingencies are divided into three categories:
- Contractor
- Owner
- Design
Construction contingencies are required for every project, regardless of which type is used.
1. Contractor contingency
Everyone is aware of the following:
- Price increases
- Unexpected problems
- Mistakes
A contractor contingency allows the contractor to manage cash when unexpected problems arise. A contractor contingency is the amount incorporated in the contractor’s projected price for the project. This amount goes beyond the schedule of values and is set aside for unexpected costs or other challenges for which the contractor is responsible.
2. Owner contingency
However, contractor oversight or error is not usually the cause of project changes. Occasionally, the owner may choose to make changes to:
- Project and staff scheduling
- Resources
- Design
The owner contingency in this scenario is an amount set aside to cover any adjustments requested by the owner. With GMP (guaranteed maximum price) contracts, owner contingencies are frequently used.
Most owners will request that any unused owner contingency assets be applied to improve the project, such as:
- Replacing elements that were deleted due to financial constraints
- Adding products to the wish list that were previously "on hold"
- Improvements to materials or supplies in general
3. Design Contingency
Before a project begins, designers try their utmost to generate detailed designs. However, design aspects may be altered throughout the project for a variety of reasons, including:
- Unavailability of material
- Scope creep
- Required upgrade
When these concerns arise after the project has started, the designer may decide to use the design contingency to pay the expenses of these issues that are not covered by the "as-bid" plan.
The purpose of the contingency plan is to soften the impact of risks that occur. Without it in place, the risk's full impact could have a significant influence on the entire project. The contingency plan is the final line of defense in the event of a disaster. A project manager should have a contingency ready for implementation rather than having to create one as the risk grows.
The contingency is just another tool in a project manager's inventory of tools for ensuring project success. Contingency planning is a must in today's project management world because of the timing when a contingency must be executed.