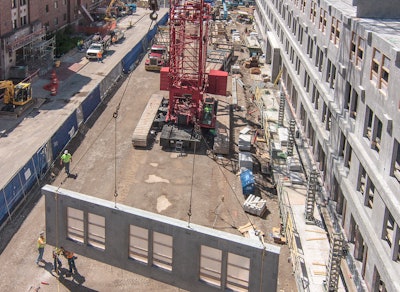
Precast concrete components and prefabrication are lean-construction keys to general contractor Walbridge’s efforts to counter declining U.S. labor productivity and boost job profit.
Walbridge’s experience on two recent projects – which the company shared at the 2016 AGC IT Forum – demonstrates that smart use of precast concrete structural components can make projects leaner – faster, more efficient and more profitable. As can standardizing and prefabricating repeated processes, such as building bathrooms for a university residence hall, assembly-line style.
Lean construction disciplines contractors to focus on activities that add client-recognized value, on reducing wasted time and materials and on improving quality in repetitive work.
“Value changes shape, form or function – if what you’re doing advances project shape, form or function, that’s the value add that the customer is willing to pay for. The customer doesn’t care about waste,” says Remo Mastroianni, engineering manager with Walbridge. “We have control over the waste, and it makes up 90% of our process. Our profit opportunity is in the waste.
“Building Information Modeling and simulation can take so much waste out of the process up front,” Mastroianni adds. “If we do it right the first time with technology, we’ve got a hell of a better chance of doing work without having to take things out and redo them at the end.”
BIM technology also provides contractors the tools to assemble building modules in a controlled off-site environment with accuracy that makes assembling prefabbed modules on site efficient. Improved quality, speed and timing that Walbridge has gained in prefabbing easily overcame the cost of moving modules into position on site.
A benchmark Walbridge building involving prefabrication involved gutting a University of Michigan residence hall constructed in the 1920s. To satisfy the university’s need to put the residence hall back in service within one school year, Walbridge built 120 modular bathrooms off-site.
“When these units were being constructed, the building was still being demo’d,” says Mike Haller Jr., superintendent of the Walbridge prefab shop. “They were still taking down walls, and prefabricated bathrooms were ready to be brought into the building.
“We used new stairwells to get units into position in the building,” Haller adds. “BIM modeling helped us figure out if routings would work. Units were literally clearing beams by less than an inch. Some had to be shortened half an inch just to get units into position.”
The project settled some arguments against modularized construction.
“We proved that by being able to limit the number of people on site we were justifying the cost to haul [prefabbed bathrooms to the site],” says Haller. “And it made the timing for the schedule – something that you can’t put a dollar amount to.
“We saw increased production from working in a temperature-controlled building. The local tradesmen that built these bathrooms didn’t have to deal with working in a building with no roof on it, and we didn’t have materials getting damaged by weather.”
Prefabbing bathrooms on a warehouse floor also advanced safety.
“A lot of the work that guys normally do from ladders, or carrying materials up stairs, was done on the ground,” says Haller. “We eliminated having to hoist materials up another floor, and worry about fall protection and tie-off points.”
The project’s success brought the University of Michigan back to Walbridge to construct a new residence hall.
“They were very impressed with what we had shown in the previous project,” says Haller, “And they wanted us to expand on that.
“We came up with precast panels. Even though it was the customer’s bread and butter to build steel structures with cast-in-place decks, we did the entire building structure in precast. We also did modular bathrooms and modular pipe racks.”
The $131-million Munger Graduate Residence Hall required more than 1,000 precast panels. Sixty were delivered each day.
“The precast was brought in from Grand Rapids – about two hours away – and none of the panels were ever laid down, because of the restrictive size of the site,” says Haller. “We staged the trucks off site. They were brought in and each piece of precast was picked right off the trailer and set in place on the building.”
Assembly discipline cut more than a month from the schedule, compared to building with steel.
“The tricky part was the modular bathrooms,” says Haller. “Thirty-four craft workers created 730 of them at a nearby facility. We needed to be able to ship 106 for one floor every month. So over 30 calendar days, we were producing just over three complete bathrooms per day.
“The modular bathrooms were fully tiled, floors in place, accessories, shower curtains, everything that you could think of was in place and completed before it left the prefab site,” says Haller. “The only thing that was left to do was to set the toilet once it was on site.
“We set up using Henry Ford’s idea of the moving assembly line,” says Haller. “Workers never moved from station to station to station, or room to room to room. The rooms moved to them.”
Bathroom ceilings and walls were bench-built in sub-assembly areas, with all of the mechanical components in place.
“Craft workers were not getting up on ladders or scaffolding, having to worry about handing material up to one another,” says Haller. “At the end of the assembly line, all the walls would be brought to the last station. The bathroom was assembled with the ceiling hoisted up on top of the unit and all the electrical and mechanical components inside of it. We reduced our solder joints by 86%. There were only five solder joints that had to be done while up on a ladder.”
There were 96 apartments designed with individual suites – sleeping rooms with private bathrooms – around a main hallway. Plumbing, fire protection, HVAC and all other mechanical systems were installed in modular pipe racks. After a pipe rack was lifted into place in the hallway, each mechanical craft could quickly come in and connect their components to the building infrastructure.
“So in each hallway – all 96 of them – we saved three-quarters of a day doing it this way,” says Haller. “With modularization, we saved about 15% of the time compared to stick building in place with traditional methods. We could have built 106 more bathrooms – enough for an additional floor – with the material we saved just by having the suppliers cut the drywall and studs before they shipped them to us.”
When Walbridge showed the U.S. Green Building Council how much was saved in the process, it helped elevate the project from LEED Silver to LEED Gold.
“The client’s very impressed,” Haller reports. “They’re talking about building more this way just because of the amount of time it saved them. They saw how much money it saved them.
“We actually modularized our prefab facility,” says Haller. “We can take it anywhere.”