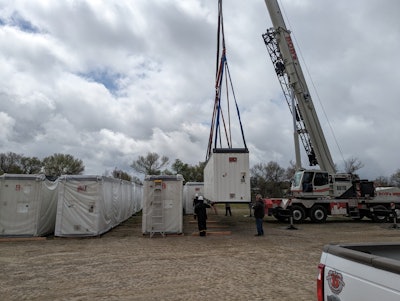
As renewable energy generation continues to grow, the use of battery energy storage systems (BESS) in solar farms has become increasingly important for stabilizing the grid and enabling the integration of intermittent solar and wind power. The permitting process to build a BESS facility often requires a formal plan for site decommissioning and disposal, even if this won’t happen for many years. When a BESS does reach the end of its useful life, disposal can be a complex task that must be carefully planned and executed.
If you are just starting the permitting process, or in the early stages of BESS project development, this article is for you.
The Decommissioning Process
Brian Davenport, vice president of energy at Industrial Process Design, reminded us of Benjamin Franklin’s famous quote: “By failing to prepare, you are preparing to fail”.
Decommissioning a BESS facility is a multi-step process that requires careful planning and coordination. Before the start of work, the appropriate disposition for all materials must be defined. The goal is to maximize reuse and repurposing wherever possible and recycling in full compliance with the local safety and environmental regulations, while properly disposing of any hazardous or non-recyclable components. With a disposition plan in place, and leveraging their practical knowledge and experience, Brian and his colleague Steve Feinberg, president at Bluewater Battery Logistics, broke down the process into five key steps:
1. De-energize
You must de-energize the system by isolating all sources of electrical and mechanical energy. This can include disconnecting the AC grid and drawing down and isolating DC sources like batteries, solar panels, and UPS systems. It can also involve disconnecting fire suppression systems to prevent accidental discharge. Developing a de-energization plan requires site equipment layouts and electrical one-line diagrams. With these documents, energy sources can be identified and a comprehensive lockout-tagout (LOTO) program can be devised.
Isolating and manually removing the battery modules is part of de-energization. Depending on the manufacturer, battery enclosures can have over 300 modules, each weighing hundreds of pounds. This labor-intensive process includes the removal of hundreds of busbars and communication cables and thousands of mounting screws. For liquid-cooled systems, coolant may need to be drained before removal. Modules are palletized, packaged, and labeled for Department of Transportation (DOT) regulation-compliant shipping. Efficient and comprehensive material handling plans are crucial.
2. Disconnect
With the system fully de-energized, battery containers, transformers, switchgear, control systems, panel boards, and all miscellaneous electrical balances of plant components can be physically disconnected and prepared for removal. For example, cables, conduits, and anchor bolts can be cut and ancillary structures like steps, racks, and raceways can be detached.
3. Remove
Once disconnected, everything can be removed from the site. Rigging and logistics plans are needed to ensure safe working conditions and efficient workflow. The size, weight, quantity, and location of components may require specialty lifting equipment like a telehandler, boom truck, or crawler crane. The quantity of vehicles needed to remove the items, typically tractor-trailers, can create traffic issues and bottlenecks. This must be choreographed ahead of time.
4. Disposition
Once loaded onto their respective vehicles, all battery modules, enclosures, equipment, scrap metal, and general site waste are compliantly and safely disposed of in accordance with the disposition plan.
5. Demolition and Restoration
After everything has been removed, the demolition and site restoration phase begins. This includes tearing down any remaining structures, removing foundations, clearing the area, and restoring the site to its original condition.
Planning and Logistics
Successful BESS decommissioning requires meticulous planning and coordination of logistics. Bluewater Battery Logistics
Safety-first Approach
Decommissioning BESS poses significant safety risks, including electrical hazards, fire and explosion risks, and exposure to hazardous materials. A comprehensive safety plan is essential, with proper training, personal protective equipment, and procedures in place to mitigate these risks.
Scope and Fees
Developing an accurate scope of work and associated fees is critical, as BESS decommissioning can be a complex and costly endeavor.
Rigging and Logistics Plan
Carefully planning the rigging and transportation logistics is crucial. This includes determining the number and size of picks required, the need for specialized equipment like crawler cranes, and the number and type of trucks needed for material removal and transport. Access constraints and site conditions must also be considered.
BESS decommissioning must comply with all relevant regulations and requirements set forth by the Authority Having Jurisdiction (AHJ). These can vary significantly from state to state (and from site to site), so a thorough understanding of local rules and regulations is essential.
Disposition and Recycling
One of the most critical aspects of BESS decommissioning is the proper disposition of the various components. It is important to explore all options for reusing, recycling, repurposing, and reselling, to minimize waste and maximize the value of the recovered materials.
The battery modules are the most valuable and complex component. Their disposition is heavily influenced by battery chemistry, with NMC batteries typically having a higher recycling value compared to LFP batteries, which may often incur a recycling charge. The battery's condition and intensity of use in its first-life application also play a significant role in determining whether you recycle or repurpose the batteries.
In addition to the battery modules, other BESS components such as enclosures, switchgear, transformers, power conversion systems (PCS), and cabling/conduit can also be reused, recycled, or repurposed. Careful planning is required to ensure these materials are handled and transported safely.
Challenges
BESS decommissioning often involves unexpected challenges, equipment failures (e.g., pneumatic bander), or the need for improvised solutions (e.g., using a car inverter to charge power tools). Having a backup plan for every step of the process is essential.
The sheer number of components involved, from screws to bus connections, requires meticulous attention to detail. Verifying critical dimensions, anchor points, and container heights is crucial to ensuring a smooth decommissioning process.
Proper packaging and labeling of batteries, especially hazardous waste like damaged battery modules, is required for safe transportation. Coordinating with recyclers and ensuring they are equipped to handle the materials is also a key consideration.
Each BESS site is unique, with its own set of access constraints, traffic flow patterns, and other site-specific requirements. Developing a comprehensive understanding of the site conditions is necessary to plan and execute the decommissioning effectively.
As the adoption of renewable energy and BESS technologies continues to grow, the need for comprehensive decommissioning and end-of-life planning will only become more critical. Preparation, attention to safety, and a holistic approach to utilizing batteries at various stages of their life cycle contribute to the circular economy. Reusing batteries, rather than recycling them, maximizes battery value and minimizes environmental impact.
By learning from the lessons shared, BESS owners and operators can better anticipate and navigate the decommissioning process, ensuring a safe, efficient, and environmentally responsible outcome.