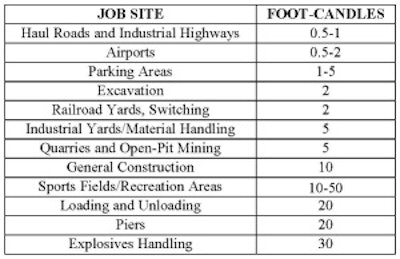
Safety issues are always a concern for contractors. When darkness or other difficult conditions exist, these concerns multiply. With so many construction zones occupied by workers at night, a good source of light is needed for crews to get their jobs done safely and efficiently.
Portable light towers provide the perfect solution for these situations. But lighting a construction area involves more than simply putting up a tower. That's because proper lighting of a construction area does not only concern the safety of workers. It also affects the welfare of anyone encountering a jobsite at night, including drivers on a highway. Identifying key lighting safety issues helps protect all individuals affected by nighttime work, and also helps provide the conditions necessary to keep projects moving forward.
Getting It Right
Before powering up a light tower, the correct amount of light needed to work safely and effectively in a construction zone must first be determined. If the light is not bright enough to thoroughly cover the jobsite, progress on a project could slow or workers could be at risk of injury from unseen obstacles.
The Illuminating Engineering Society, a group of lighting industry experts, has established a set of guidelines (see chart at right) to help contractors determine how many foot-candles of light a particular jobsite requires. A foot-candle is the intensity of light per square foot of surface area. By calculating the size of the area to be lit, the correct amount of light needed can be determined.
The level of illumination required also depends on the type of project being performed. For instance, is lighting needed on an area containing black soil, concrete or asphalt? Because soil and asphalt absorb light, more light towers may be needed to reach the optimal foot-candle measurement when on these surfaces. Concrete may not require as many towers, since this material naturally reflects light.
Weather conditions can also become a factor when determining the light needed on a site. If the sky is cloudy, the number of light towers required to reach the desired illumination level may need to be increased to counteract clouds blocking the moon's light.
By determining the size of the area to be lit, following lighting guidelines and considering outside factors that may affect lighting, contractors can determine the amount of illumination necessary to provide a safe working environment.
Proper Positioning
After establishing the correct level of lighting, the next factors to consider are where the light tower should be placed and how its fixtures are positioned.
The ground on which a tower is placed is vital to the unit's stability. When settling on a location, seek a surface that is flat and firm, as a portable light tower could potentially fall over if placed on rocky or sandy soil or an uneven grade. Overhead obstructions, such as power lines and trees, may also inhibit the use of towers in a particular location. Since a tower can be deployed as high as 30 feet, the unit must be free of anything above the ground that may damage the tower and subsequently risk the security of workers and others around the site.
The positioning of the tower's fixtures is the next safety factor to address. If light towers are not positioned correctly, the direction the light shines from the fixtures may reduce visibility for passing motorists. Operators must find the right balance between creating the best possible lighting scenario for the site and protecting drivers from unnecessary distractions.
Fortunately, operators have an infinite number of positions, angles and directions in which light fixtures can be positioned. The key is to arrange the units to light up the job site safely, but not blind or obstruct traffic.
The best option is to place the light towers in such a manner that they shine away from oncoming traffic, as this positioning creates optimum visibility for drivers traveling through the construction area. In addition, tilting the fixtures down 20 degrees increases the efficiency of the light tower by focusing the light on the jobsite and minimizing the amount reflected skyward. Another important technique places the light towers on each side of the site so they face each other. This helps reduce shadows and eliminate dark areas to increase construction site visibility for workers.
While advances in technology have made a significant difference, some portable light towers may still produce a small amount of glare, which can temporarily blind motorists, compromising the safety of both drivers and construction crews. However, glare can be easily corrected by angling the light fixtures down while employing a visor. This curved piece of aluminum attaches to each fixture to prevent light from traveling in an undesired direction. In addition, a visor can reflect light back to the ground to increase its intensity on the site. This tool's benefits are two-fold: it decreases the driver's possibility of being distracted by light while increasing the efficacy of the light itself.
The Next Level
Following the tips above will help create a higher level of safety for workers and bystanders alike. But as safety around construction zones continues to improve, so does the technology going into light fixtures themselves.
Today's towers are engineered to help eradicate common lighting challenges contractors have faced for decades. For example, light fixtures are now designed to help eliminate "hot spots," an area that receives a high concentration of light while another location is left in the dark. These fixtures distribute light more evenly to cover a job site more efficiently. Some manufacturers are also producing light fixtures developed with strategically positioned reflectors that maximize the light produced by the lamps, further increasing the safety of crews operating under the stars.
Automatic lighting sequence and command control systems have also improved job-site safety and security. These systems automatically turn lights on and off at a set time, eliminating manual operation. Photocell sensors start the unit's power at dusk and shut down the tower when the sun rises. This removes the need for a person to take time away from a job to turn the light tower on and off, while lowering the risk of accidents caused by operators crossing busy construction areas.
Light towers are easier to transport from job to job, thanks to units designed to withstand the rigors of travel. This engineering reflects how today's light towers are created with portability in mind. Instead of modifying permanent stadium or parking lot lighting, portable towers offer the durability necessary to stand up to the demands of a job site. These advances in technology and design have not only made portable light tower usage safer, but have also created better lighting for work environments.
Allmand Bros. Inc., established in 1938, is a leading manufacturer of a wide variety of portable light towers, jobsite heaters, compact tractor loader backhoes, Port-A-Lite™ light stands, and solar arrowboards.