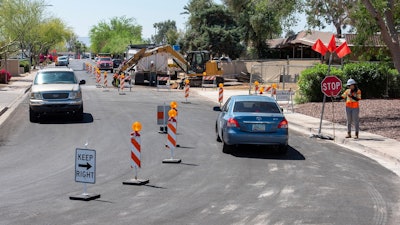
There are so many details involved in running your asphalt business, and on any given day, if one of those details gets away from you it could mean the loss of production, a customer, cost overruns, or even damage expensive equipment. All of those outcomes pale in comparison, however, to what can happen when jobsite safety isn't prioritized and someone on your crew gets hurt, or worse.
Proper training, awareness, and planning all go in to ensuring the safety of your crews is protected. Protected from what, though? In every work zone there are individual, equipment, and external safety factors. There will always be unexpected and uncontrollable elements at play, of course, but if you take the necessary steps you can reduce the chances of permanent or serious harm. Additionally, it's important to note that avoiding such scenarios also means avoiding negative liabilities and financial risks to your business, as well.
The statistics on work zone safety have been trending in the wrong direction when motor vehicles are involved, and since the end of 2020 it's gotten worse. By the very nature of what our industry does, we work everyday in the primary environment of cars. The safety measures you take are meant to protect your people, your employees, but they are designed to communicate to drivers. The problem is that many of today's drivers are distracted, not paying attention to signage, lights, or flaggers.
According to the National Work Zone Safety Information Clearinghouse:1
"Over the past 10 years, work zone fatalities have increased from 619 in 2012 to 956 in 2021. This equates to nearly three persons per day being killed in work zones in 2021. Approximately four out of every five work zone fatalities involve a driver or passenger of a vehicle. Meanwhile, estimated injuries in work zones have also increased, from 31,000 in 2012 to 42,000 in 2021. In 2021, this equates to approximately 112 injuries per day in work zones. (Source: NHTSA FARS, GES, and CRSS)"
According to a report by The Center for Construction Research and Training, road maintenance workers died on the job approximately four times more often than the average American worker, and nearly twenty times more than administrative, engineering, or office workers.2 Even parking lot pavers should take for granted their safety just because they're off the road. Near the end of the 2023 season, I saw a post on social media from Royal Pavement Solutions owner Kenny Roy, where a distracted driver plowed right through their cones and tape, and were lucky that no one was injured.
Sharing a workspace with drivers is dangerous, whether on roads or parking lots, but there are important steps that can be taken wherever asphalt is paved.
Building A Better Plan: Recognition and Empowerment
Whether or not you already have a safety plan in place, taking the time to review your policies and their effectiveness on a regular basis, is just as important as getting one on the books. If you are starting from scratch, know that everyone takes a different approach to it.
"One of the things we talk about the most is situational awareness," said Justin Baskin, National Safety and Environmental Director for
The central tenet of Baskin's methodology is that the people doing the work are the literal frontline of safety, because they are in the thick of it. They are on the site, using the tools, and are the first line of defense when it comes to improving things.
"Part of my job is to create an environment where if someone on site feels unsafe in a situation, they know to go to the project manager, to come to me," Baskin said. "I want them asking how it can be done more safely, or how they can mitigate the hazards. Then, I want them to act on that, because they're having a shared experience out there. What is endangering to one person will endanger the next, and so we want to break that pattern."
Baskin noted that in this line of work, one of the biggest hurdles to this first step can be a sense of machismo or an anxiety about speaking up when people feel that something isn't safe. That definitely can be an issue, and the only way to overcome it is with company culture change.
"Since I came in last year, I've noticed my [crews] are paying better attention," Baskin said.
As an example of a positive scenario Rose Paving has recently seen turn into a new safety practice, they had a crew doing a pavement repair for a U.S. Mail distribution hub. In one particular area, they had a lane of traffic closed off, and the adjoining lane was still open to limited traffic. Despite having cones and signage, some of the crew felt nervous about it, and decided to take action.
While anyone was working with their backs to the open lane of traffic, one spotter was positioned between them to stand watch and keep an eye on how far they were unknowingly backing up while focused on their task. This allowed the guys working on the pavement to stay focused on the job without fear, keeping them safe, and the job on schedule. The danger was identified in the moment, addressed, and a quick but effective solution put into place immediately.
If all other options on site are exhausted, and things still don't feel safe to an employee, Baskin said that there is still one final thing he makes sure all Rose employees know. They can call or message him directly, twenty-four hours a day, seven days a week.
"They all have my direct number," Baskin said. "That's what they have in their back pocket all the time. We want them to know is we have their back. Also, it's a major key to the growth of the safety culture at Rose Paving is our Assistant Safety Managers at each location being our safety champions and support from our executive leadership."
Getting Outside Support When You Need It
Not every company has the available resources to hire a full-time position dedicated solely to job site safety management. In many cases it's a role being filled by someone who is pulling double-duty or wearing multiple hats. If that sounds familiar, then you are probably aware of hard it can be to try to:
- Create new safety policies and standards
- Daily management multiple jobsites
- Execute correct permitting requirements
- Implement new safety technologies where needed
This can especially be the case when you are in a situation where you're trying to either overhaul or establish a new company culture of safety.
"Our goal is to ensure every team member, their safety and well-being every day, in addition we also try to maintain a strong and trusting customer partnership," said Seth Walpole, VP, Integration & Transformation at AWP Safety. "We want to bring innovative tools to contractors through our fleet monitoring and analytics, where a driver's habits aren't just recorded, but predictive software can offer guidance on ways to prevent unsafe situations."
Additionally, AWP Safety has automated flaggers and signaling trailers that can safely direct the flow of traffic while communicating with each other, and trigger GPS systems to notify drivers using the system that they will encounter construction on the road. The integration of cutting-edge technologies are a great next step for contractors who've made improvements to their company culture, but would welcome high tech tools to eliminate further risks.
One of the biggest hurdles, which we've mentioned here already, is navigating and filing for the proper permits in a given locality. This is a huge deal, and it can be an even bigger headache if not taken care of.
"Part of what we do is take that off the plate for clients," said Walpole. "If a contractor brings us in during the planning phase of the process, and we can see where all the needs are going to be, taking care of the permitting is always important. We can bring to the table by doing that for them."
You can set a good example for your crews by asking for help in these areas when you need it, just like you want them to speak up and identify areas that they might need help or assistance in making things safer. The important part, however, is that you can't expect a high degree of safety if you wait until the last minute. Whether that means putting together safety plans just internally, or if you intend to seek outside expertise like through the services AWP Safety provides, the earlier you get started the better.
"We've definitely had clients call the night before," said Walpole, discussing how contractors can shoot themselves in the foot. "They'll want to know if we can have flaggers, automated lights, or whatever they need, and we want to be able to get that to them. However, it's much more difficult to pull that off on short notice, and you don’t want to leave safety to chance."
It all comes back to taking a proper inventory, and you don't want to be doing that on-the-fly. While doing your due diligence might take time and resources, in the end, protecting your employees, and ultimately protecting your business, is worth every dime and minute spent.