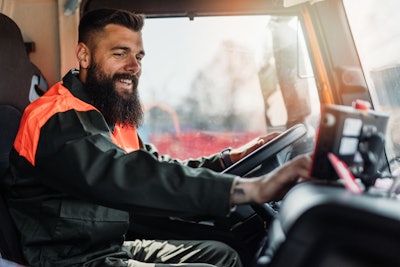
Employee retention and satisfaction is top-of-mind for managers across industries. But this is especially true for the construction industry, as keeping crews happy and productive is key to maximizing ROI. Highway/heavy construction and general building professionals face unique challenges – demanding schedules, tight budgets, and the need for a skilled workforce to operate and maintain a diverse range of equipment. Fortunately, fleet management and fleet maintenance technology offer a powerful solution, creating a work environment that empowers drivers and operators to prioritize safety, reduces downtime, and optimizes equipment utilization.
Streamlining Workflows and Reducing Busywork
Manual paperwork is prone to errors and omissions, and for fleets using multiple solutions, it can be difficult to cross-reference siloed data points. Fleet management software eliminates this risk by capturing data electronically and consolidating data from other fleet and business solutions into a single platform. Digital inspection checklists can include features like photo uploads to document equipment condition and allow you to leave comments, ensuring a more comprehensive record. This data is also readily accessible for future reference, allowing fleet managers to track equipment history and identify potential maintenance issues before they escalate.
Let’s look at a backhoe operator, for example. Previously, their workday may have involved spending 20 minutes at the start of each shift filling out paper-based pre-trip inspections and manually logging equipment hours. By using fleet management software with a mobile app, this entire process can be completed electronically in a matter of minutes. Operators can fill out and submit digital inspections in real time, and inspections can be customized to include detailed instructions that guide the operator through the process, ensuring they don’t miss any critical safety checks. This frees up valuable time for the operator to focus on the actual excavation work, improving overall productivity on the job site.
In addition, subcontractors are heavily used in the construction industry and can often become a point of contention due to a lack of communication and transparency around jobs and hours. Utilization data, first ignition time, and last ignition time can be compared against the hours charged to ensure proper payment and stay on top of equipment maintenance.
The time saved by automating tasks translates into significant increases in efficiency for your entire operation. Drivers and operators can spend less time on paperwork and more time on their core responsibilities, whether it's delivering materials, operating equipment, or completing service calls, translating to faster project completion times and improved driver, operator, and customer satisfaction.
Fleet management software eliminates this risk by capturing data electronically and consolidating data from other fleet and business solutions into a single platform.@KOTO - adobe.stock.com
Arming Crews with Real-Time Communication
Feeling disconnected and out of the loop can be a major source of frustration for drivers and operators. Clear communication and real-time visibility are crucial for maximizing crew productivity, equipment uptime, and, ultimately, your ROI. Fleet management software transcends basic vehicle tracking, transforming your crews into a connected team through the following features:
- Live Location Tracking and Monitoring: Gone are the days of relying on guesswork or infrequent check-ins to know where your crews and equipment are located. Fleet management software integrated with telematics provides a current map view of all your vehicles and equipment, allowing project managers and dispatchers to see the location of each excavator, crane, or dump truck. This empowers them to make informed decisions about resource allocation, optimize dispatching for service calls, and track progress on multiple jobsites simultaneously. For example, a project manager may need to quickly locate a specific excavator for an urgent task on a tight deadline. With real-time location data, they can instantly identify the excavator’s availability and dispatch it efficiently. In addition, this software can track asset status, offering further insight into whether an asset is active, down, or in the shop, minimizing delays and maximizing crew productivity.
- Instant Equipment and Issue Notifications: Eliminate the need for time-consuming phone calls or outdated paper schedules. Notifications can be delivered electronically through a mobile app, ensuring crews receive critical updates instantly. This includes alerts when someone comments on equipment, a vehicle is linked or unlinked to equipment, or when a status is changed by another user. For vehicle issues, you’ll get notified if someone comments on an issue, an issue is assigned to you, or a new issue is created. This proactive communication allows for immediate adjustments and improved coordination.
- In-App Messaging: Managers can foster a collaborative work environment by adopting technology that allows for seamless communication between crews, dispatchers, and project managers. Operators can use in-app messaging or the “mentions” feature to quickly report any issues they encounter on the job, such as a malfunctioning piece of equipment or a safety hazard on the site. Dispatchers and project managers can then address these concerns promptly, providing clear instructions or sending assistance if needed. If, for example, a backhoe operator discovered a potential gas line leak during excavation work, they could use in-app messaging to instantly notify the project manager, who can then take immediate steps to secure the area and ensure crew safety.
Prioritizing Safety and Crew Well-Being
Accidents, equipment breakdowns, and a lack of safety protocols can not only lead to project delays and costly repairs but also contribute to operator frustration and high turnover rates. Fleet management software powered by real-time data analysis allows fleets to see service trends that can help them tailor maintenance schedules based on usage and recurring issues. This ensures critical services are performed on time, preventing minor problems from escalating into major breakdowns. By knowing their equipment is well-maintained, operators can focus on their tasks with greater confidence and peace of mind.
A commitment to safety goes a long way in demonstrating respect for your operators and creating a positive work environment. Fleet management software that integrates with telematics devices can identify areas for improvement in safe operation best practices through driver behavior monitoring. By providing constructive feedback based on data, such as harsh braking or speeding, project and fleet managers can implement targeted training programs to address these concerns. This data-driven approach not only fosters a culture of safety but also demonstrates a commitment to operators’ success by investing in their skill development and demonstrating a commitment to their well-being.
Fleet management technology doesn’t just optimize workflows and equipment – it fosters a fundamental shift in your crew dynamic, replacing siloed information and guesswork with active communication and shared data. Fleet management software empowers operators to become active participants in their work environment, fostering collaboration and mutual support. This connected team approach not only translates into more efficient and successful operations but also builds a sense of ownership and pride within your workforce, creating a company that thrives on a foundation of collaboration and its most valuable asset – its crew.