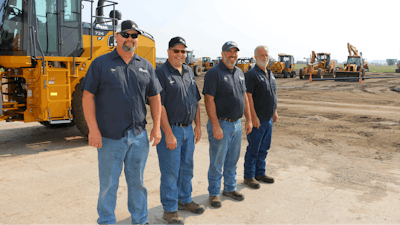
Think back to your late high school years: Did your parents, a school counselor or other influential person encourage you to find a job for life? For many years, this was a pretty common idea – get an education, find a job, put in your years and retire with the company.
This type of career path, the idea of a “job for life,” is becoming less common. In fact, the labor market is more challenging than ever, with more industries finding it difficult to attract, grow and retain workers.
However, there are still stories of people finding a job for life. In the construction industry, it is important to see what can be learned from these people to help solve this longtime workforce issue.
More Than a Century of Service
Head to the city of Grand Forks, ND, to the local RDO Equipment Co. store. Step inside the service shop and it is there, among the work bays, overhead cranes and array of earthmoving machines, that you will find not one, not two, not even three but four “job for life” team members. These four service technicians have more than a century of collective knowledge, experience and hands-on skill between them.
Jason Kouba, Paul Seidel, David Somerville and Mike Sundberg all celebrated 25 or more years of work service within the past year. Perhaps even more remarkable than their quarter-century tenures as service technicians is that all four of them have remained at the same company and in the same location throughout.
When asked what has kept them in these roles so long, they all looked around the room, shared a quick smile and laugh and pointed at each other. “It’s these guys right here,” Paul says with the rest nodding in agreement.
The four of them have built a bond throughout the years, seeing machines evolve, learning new technology and helping to mentor the next generation of service technicians, all while working alongside each other. While that bond has played a central role in their “job for life” career paths, it has not been the only factor.
These long-termers cite industry advancements, opportunities to learn and grow and the ability to have a profound impact on their customers’ business as reasons why they have gone the distance in the equipment industry with RDO. Their stories offer insights to help every company improve at attracting, growing and retaining talent.
The New Reality
We’ve all seen how the media portrays skilled trades jobs: Men in coveralls working in the midst of a big garage surrounded by the roar of equipment and a thick diesel smell in the air. And their primary duty is to endlessly wrench on dirty machines.
Anyone who works in the industry knows that picture is outdated, but the reality is that is still the perception many have. It is that perception that often creates a roadblock to people seeking to enter the equipment industry.
First off, the noise level is about the same as riding a subway. “You used to have to wear ear protection working around heavy equipment,” Paul remembers. Now, machines operate and idle quietly.
Secondly, new engine design and DEF standards mean that those big black clouds are a thing of the past. “Years back, you’d start a loader and you couldn’t breathe,” Dave recalls. This is not the case anymore. Equipment runs clean and virtually odorless.
Third, there are more women getting involved in the industry. According to OSHA, the number of women employed in the construction industry in the United States grew by more than 80% from 1985 to 2007. The number peaked at more than 1.13 million women in 2006, according to the National Association of Women in Construction, and the number again surpassed one million in 2018.
Related Content: Ladies of Sunbelt Rentals Discuss Opportunities for Women in Construction
Finally, while every technician will agree there is still plenty of wrenching on the job, Mike points out that the technology evolution “has changed the way we diagnose, repair and troubleshoot equipment.” In fact, ask any technician what their most valuable tool is and most will agree that it's their laptop.
No longer are technicians lugging around manuals, going back and forth from one heavy book to another. Everything they need to diagnose and troubleshoot is right there in one of the most widely-used pieces of technology that exists. For those who operate and manage machines, technology has changed the way they do their jobs for the better, as well.
Technology Advancements Equal Opportunity
The advancements in technology present one of the biggest opportunities to bring new people into the equipment industry. All four Grand Forks technicians benefited from growing up around equipment. Mike was known as “the guy who fixes everything,” while Dave followed in his father’s footsteps, starting his career as a military vehicle mechanic. Yet, that scenario is becoming less common.
With more people growing up in cities – nowhere near a machine shop – the service technicians, fleet managers and equipment operators of tomorrow are less likely to have close ties to equipment. They are spending their time with computers and tablets, maybe working on bikes and cars, but not often around tractors and dozers.
But, according to Andy Luikens, recruiting program manager for RDO, these skills are highly transferrable. Andy is helping the company tap into a talent pool of those who are tech savvy but unaware of the opportunities available in the equipment industry.
“People are surprised to learn how much technology is integrated into construction machines,” he said. “We are seeing people who are interested in computers, robotics, even video games become interested in machinery because of the technology aspect. People who would have never considered the industry are taking notice.”
Related Content: Gamers Help Rosendin Advance VR and AR Technology on Construction Projects
Companies that continue to meet their talent needs will be the ones that are able to address the misconceptions and successfully tap into new markets.
Doing Work that Matters
Once a company is able to attract employees, there is the tough work of retention and keeping them happy. Research from a 2018 LinkedIn survey showed that it is important to people to work for a company where they can learn and grow. In fact, the lack of learning and development opportunities was cited as the No. 1 reason why people would leave their job.
Jason, Mike, Paul and Dave all appreciate RDO’s support of continuous improvement through various training and learning opportunities. They credit it with helping them stay up-to-date on the latest technology and machine advancements. Especially for younger team members just starting out, the impact of RDO’s investment in learning and development is huge.
Paul can attest to this, as he benefited from it early on in his career, when he got his start as an intern in RDO’s Access Your Future program. “I learned so much in that time I got to work alongside veteran technicians and ride along in a field service truck,” he recalls.
It is because of this early impact and being at this stage in their careers that these seasoned technicians now see it as their responsibility to prepare the next generation, sharing their knowledge and acting as mentors. Certainly, those early career technicians are getting formal training but are also learning every day from shadowing their more experienced colleagues on complex jobs in the shop and out on a jobsite.
That leads into one more key area that matters to job seekers: the fulfillment that comes from skilled trades jobs.
Research shows that it is important to people, especially younger generations, that the work they do matters. They want to know their job has a purpose and is making a difference. In fact, a survey by the New York Times showed that employees who derive meaning from their work are three times more likely to stay in their organization.
“One of the biggest things that surprises people about working in the equipment industry is the impact they can have,” Andy said. “As we know, infrastructure never sleeps and it is our mission to show them that every day they are making a difference.”
While equipment operators can literally see the work they do come to life, the impact of service technicians is realized in a different way. Jason shared his perspective, saying, “When a machine is down on a jobsite and I’m the one who is able to get it going again, that’s really satisfying.”
Industry for Life
The four service technicians at RDO in Grand Forks and their “job for life” story may be somewhat of an anomaly. Their relationship and circumstance would be nearly impossible to recreate at another company, whether out on a jobsite or in a service shop.
Yet, thanks to industry advancements, career potential and the opportunity to make an impact, overcoming the decline of “job for life” is something that can happen within any company. In fact, Andy sees a new opportunity from this change and one where every company, not just RDO, wins.
“We’ve changed the idea of ‘job for life’ to a goal of ‘industry for life’,” he said. “We are striving to give folks the educational opportunities to progress and grow their career, encouraging them to stay in the equipment industry for life.”
As an industry, we can all do our part to build on this “industry for life” concept, ensuring construction, roadbuilding, utility work and all important infrastructure remains strong for generations to come.
Lindsay Paulson is the Public Relations Specialist for RDO Equipment Co. She has worked in the equipment industry for more than a decade, creating content, telling stories and highlighting the machines, people and companies that build and maintain our infrastructure.