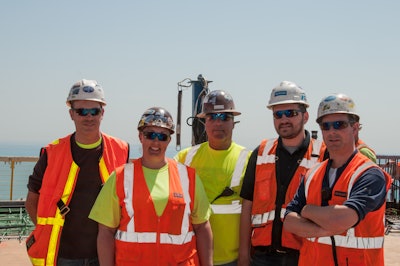
The Vista Tower construction includes a low-rise structure and three towers and is located alongside the Chicago River in the heart of downtown Chicago only a couple blocks away from Lake Michigan. The tallest tower will be 100 stories at 1,190 feet above ground, putting it in the Supertall Category—defined by the Council on Tall Buildings and Urban Habitat as any building whose height exceeds 984 feet. When finished it will be Chicago’s third tallest building, behind Willis Tower at 1,450 feet and the Trump Tower at 1,388 feet. The construction is all structural concrete and represents the latest in engineering and construction technology.
The vision to build Vista Towers began with discussions between Magellan Development and Jeannie Gang at Studio Gang Architecture. Then Ron Klemencic, the CEO of Magnusson Klemenscic Associates (MKA) based in Seattle, Washington was brought in to help make their concept structurally and economically viable. Klemencic involved McHugh Construction and others to bring together the latest research and technology and up-to-date construction practices. These lead companies have worked well together in the past. They include:
- The Developer and owner: Magellan Development Group, Chicago, Illinois
- Design: Gang Studios, Chicago, Illinois
- Architect of Record, bKL, Chicago
- Structural Engineering: Magnusson Klemencic Associates, Seattle/Chicago
- General Contractor: James McHugh Construction Company, Chicago, Illinois
As the general contractor McHugh has a long history with high-rise building construction, their first one being the iconic 65 floor structural concrete Marina Towers built along the Chicago River in Chicago constructed in 1967. Today high-rise and super-tall building construction accounts for about 60% of their business. David Alexander the company’s president says they have built eight of the twelve tallest concrete buildings in Chicago and five of the ten tallest concrete buildings in the U.S. On this project McHugh is both the general contractor (McHugh GC) and the concrete sub-contractor (McHugh Concrete) which performs all the concrete work, formwork, rebar and post-tension reinforcement, concrete pumping, and the operation of “skip hoists” and tower cranes,
Design
The design that Gang Studios settled on uses geometric shapes called “Frustums.,” In geometry, a frustum is the portion of a solid (normally a cone or pyramid) that lies between two parallel planes cutting through it. For this project frustums are inverted on top of each other so that towers angle outward nearly 5 feet 5 inches in 12 or 13 floors (a transition floor) and then angle inwards for the next transition.
Engineering
During the design and engineering phase supertall buildings undergo wind tunnel testing to study wind shear. Building models are placed in wind tunnels to see how wind flows around the model. Redesign and engineering changes often follow a test to further minimize wind shear forces. One result of the testing according to David Fields, a Senior Principal at MKA, was the inclusion of a “blow through” floor at the 83 level, a floor with no facade to further reduce wind shear. He says the building can be expected to sway about 3-feet in a design-level wind event.
An unusual feature of this building is that the outside columns of the towers stagger from floor to floor, shifting 5-inches from the column below so there is no vertical load path to the ground—the corner columns move in two directions. As a result, MKA engineered the transition level floors to handle increased outward and inward forces due to the weight and shifting support of the structure above.
Before construction
Alexander says that pre-construction talks for McHugh started in 2012, more than four years ahead of ground-breaking ceremonies in August 2016. “We put together a team to work out constructability details with the design architect, Studio Gang, the Architect of Record, bKL, and MKA. We also determined how to make the construction more affordable.”
Concrete with a high modulus of elasticity (MOE) is necessary for supertall buildings to increase stiffness and minimize building sway—building inhabitants feel uncomfortable when buildings sway very much in the wind. Testing high MOE concrete requires certification and special equipment so Flood Testing Laboratories, Chicago, Illinois, was hired. Walt Flood IV, Assistant Engineer for Flood Testing says they worked with ready-mix producer Prairie Material Service, Bridgeview, Illinois, on trial batches and high MOE concrete mix experimentation about one year before construction began. The tests included mixes with MOE as high as 8 million psi but in the interest of cost and production reliability MKA decided to specify 7 million psi MOE concrete and engineered the structure for that. This concrete is used for columns, sheer walls and the core structure of the towers.
Construction
Caissons
Max Levin, the project manager for McHugh Concrete, says there are 124 caissons encased in steel liners and heavily reinforced. Of these 24 are 10 feet in diameter and as long as 115 feet, socketing 6-feet into bedrock. The rest of the caissons are “bell shaped,” meaning that they flare out at the bottom to increase the footprint and decrease the load per square foot on the hardpan soil. These are approximately 85-feet deep.
Mat slabs
Fields says there are two mat slabs, one under each tall tower core structure and the thickness is different for each one—8 feet for the shortest tower and 10 feet for the tallest one. A low heat 7,000 psi self-consolidating mix design was used for the mats. The spread of this mix varied between 14” to 27”. The largest of the mats required 3,560 cubic yards of concrete and it took 10 hours to complete the placement. The purpose of a mat slab is to evenly distribute the weight of the building between caissons. There are also locations where building elements were supported by concrete pile caps to distribute the load between caissons.
Core structure
Many or most high-rise buildings today include concrete core structures to contain elevators and protected stairways, allowing for safe exit from buildings in the event of disaster. They are strong structural elements that lessen building sway. But Fields says they are also commonly used to minimize exterior engineered framing on buildings, giving end users a better view outside.
The shear walls for the Vista Towers are as thick as 54 inches of concrete at the base of the structure, tapering off to 18” thick near the top. Core construction always precedes floor construction by at least one floor and it’s common for contractors to use self-climbing core-forming systems today. These systems have decks above the forms to mount concrete placing booms that can place concrete anywhere on floors. When the forms are raised, so is the deck and placing boom.
Floors
Structural concrete buildings have a very significant advantage over structural steel buildings because floors are “flat plate” meaning that the bottom of a slab (the ceiling below) is flat, reducing the floor to floor height and the need for supplemental fireproofing or drop-ceilings. As a result there can be more floors in the total height of a building. Floor forming systems have evolved to make this method of floor construction easier and faster with much of the work safely done from below.
Kevin Morley, McHugh’s concrete superintendent, says that after the parking garages and lower portions of the building were completed the Vista team began a three-day cycle floor construction schedule for each tower—one floor completed every three days in each tower, each being roughly 21,000 sq.ft. This means one deck is placed every day.
In order to construct at this pace workers must be able to walk on a floor approximately three hours after concrete is placement in order to begin layout work, column forming, and floor forming for the next level. Placing rebar, post-tension (PT) tendons, structural steel members (when needed), rough plumbing and electrical, and hardware for anchoring curtain walls and other things follows the next day.
Floor dimensions vary from floor to floor because the building is constantly angling outward or inward and so form requirements change for each floor.
Columns
While interior columns are vertically stacked, the columns nearest the outside edges of the building aren’t. As stated earlier these columns shift 5-inch outward for 12 or 13-floors creating a maximum shift of 5’5” and then they shift back toward the center of the building to the next transition level. Vertical rebar at one side of the column is terminated while rebar is added on the other side of the column where the shift occurs. Fields says additional #9 rebar (1-1/8 inch) is added to the transition floors to manage the additional forces generated there.
The concrete mix design for the columns is different than for the floors but they are both placed at the same time. To ensure there is no confusion concrete for the columns is placed just ahead of the floor placement. It is delivered in buckets by the tower crane and overflows the top of the column a little bit, a process called “mushrooming”—concrete for the floors is pumped and placed shortly afterwards.
Shear walls
Shear walls (also referred to as “silo walls” on this project) on the outside of the building also move in and out with the shape of the building. The walls are sloped to match the building’s façade and aren’t stepped from floor to floor. Self-rising forms are used for this construction. Shear walls provide additional strength to help buildings resist wind and seismic forces.
Concrete requirements
For supertall structures the MOE of a concrete mix has become more important than its compressive strength because building stiffness and occupant comfort becomes a critical parameter. Flood says they started testing concrete mixes for MOE before Prairie Materials had the contract. But now Flood Testing works for the owner of the building, casting 9 cylinders for every 50 yards delivered to the site. Testing of cylinders occurs at 28, 56 and 91 days for MOE. The requirement for the highest MOE mix is 7 million psi as an average, with no individual test below 6.3 million psi.
Nick Beristain, the Technical Services Laboratory Supervisor for Prairie Material, says they have approximately 20 mix designs for the project. This includes 7, 6, and 5 million MOE mixes for different locations in the building, compressive strength mixes of 12,000, 10,000, 8000, and 6000 psi, and 7000 psi low heat development SCC concrete for the mat slabs.
Levin says McHugh has their own constructability requirements for concrete and they include the following:
- Mixes must be pump-able up to the 1190 vertical feet height of the building without damaging the pump or pump lines
- Concrete for floors must be hard enough for workers to walk on within three hours of placement under all weather conditions.
- Concrete for floors must have a minimum strength of 3000 psi by the morning following placement under all weather conditions so that PT can be tensioned
- Maximum concrete delivery temperature is 90ºF
- All mass concrete (concrete over 5 feet in thickness) must not exceed 158ºF at any time during its curing cycle
- Concrete in floors areas that support the tower cranes must have a minimum strength of 5000 psi within 24 hours of placement
- Concrete must have a placing slump between 6 to 8 inches. Only Prairie Material is allowed to increase the slump and only by adding an admixture, not water.
- Prairie Material must meet the volume requirements for each day in a timely manner.
Most of the concrete is pumped through one vertical pipe the height of the building.
At the time of this writing 81,000 cubic yards of concrete (10,000 truckloads) have been delivered to the jobsite.
Forming
McHugh involved Doka USA, Little Ferry, New Jersey, early in the process. Formwork technology continues to change jobsite productivity and self-rising systems are especially important to high-rise construction. Deian Ivanov, Doka’s Midwest Account Manager, says one of the challenging aspects of this construction is the increasing and decreasing angles of the unique building surface for their self-climbing scaffold systems, especially as the scaffolds maneuver around the transition floors. Their service to a project includes supervision when forms are first assembled, training, certification of workers, and frequent site visits. Here are the systems being used on the project.
Core Forms. “Super Climbing” system. Four hydraulic cylinders lift the inside and outside forms from one floor level to the next. A platform anchored to the top of the forms holds a concrete placing boom which automaticlly lifts when the forms are raised. Workers can store rebar on the formwork too, close to where ironworkers need it for placement.
Shear-wall (Silo Wall) forms. McHugh is using Doka’s SKE 50 and 100 self-climbing form systems. The outside wall forms are hydraulically lifted but the inside closeup forms are crane set by McHugh. The shear walls follow the angle of the building.
Perimeter scaffolding.
SKE self-climbing scaffold platforms with Doka’s “X-Bright” screening system surrounds the top floors. It prevents tools and materials from accidently falling to the ground, it provides shelter from the wind when concrete is being placed, and is used to enclose floors for temporary heating. Ivanov says the scaffolds are crane lifted and are attached to the concrete with embeds. A second set of SKE platforms is being utilized for the window wall system installation several floors below.
McHugh is using Peri’s MultiFlex decking system with their MultiProp system to form all the floor slabs for the project.
BIM and cell phones
Building Information Modeling (BIM) matches three-dimensional drawings with data bases that provide detailed information about every construction element. BIM is standard now and larger projects employ fulltime people to manage BIM drawings on site. McHugh uses Tekla software for their BIM work because it’s particularly good for designing structural concrete work. Morley says they have taken this new technology to a new level by providing jobsite foremen access to BIM details through their cellphones. McHugh set up “hotspots” to ensure good cellphone reception everywhere in the building. Foremen are provided with links to the parts of BIM that affect their work so that they can immediately refer to the latest detail drawings as they are needed. For example, complicated rebar designs in BIM can be viewed by foreman in close up detail where they are working. Cody Hague, McHugh Concrete’s BIM detailer for this project can also notify jobsite personal of plan changes on their cell phones.
Morley thinks the day will soon come when jobsites will go “paperless” due to this technology and likes the idea. Levin agrees but says he still likes paper plans—still used for some work.
Supertall buildings
Compared to high-rise construction supertall buildings pose greater challenges. Engineers must focus much more on wind shear and occupant comfort. Building sway during construction requires contractors to invest in and learn more advanced layout technology. Keeping costs in line is more difficult, a small example being the increased transportation time on skip lifts getting labor to and from their work areas. Weather is more problematic; it can be nice at ground level but snowing at the top of a building. The level of risk goes up for all partners too.
There are three reasons why building structural concrete supertall buildings have become cost competitive with other structural methods; the development of highly efficient concrete pumping systems, advances in cost productive technical forming systems, and concrete mix designs that can meet all the special needs for these buildings. Concrete construction is faster, more efficient and productive, and the cost is more and more affordable.
When complete the Vista Towers will include 5 floors of parking, a 12 story hotel, 81 floors of apartments and condominiums, 3 mechanical levels, and 2 floors of damping tanks to help reduce building sway.
Few of us will ever be involved in the construction of a supertall building but we can all appreciate the increasing ability to engineer and build structures that pushes the limits of our knowledge.