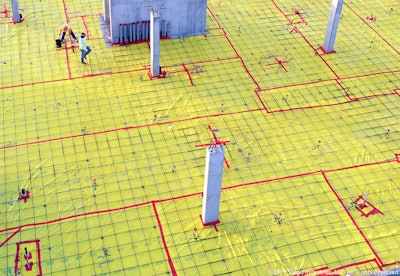
The placement of a water vapor retarder directly below concrete floor slabs on the ground has become common practice for buildings where floor coverings or coatings are to be installed. Such use has also found its way into the design and construction of “big box” warehouse structures where moisture-sensitive materials are to be stored directly on the slab, or the floor coverings or coatings to be installed in the future are unknown.
This is because building owners and developers are increasingly concerned about how their floors will perform over time. They don’t want problems associated with low permeance floor finishes, indoor air quality, product damage or “down time.” Owners are also concerned about having to deal with slab sweating, efflorescence and continued slab curling. Having an effective vapor retarder in place helps ensure a successful transition to any floor covering or coating material in the future.
Selecting the right material for a vapor barrier is essential. Shown here is a piece of membrane that couldn’t endure the high pH of the concrete and sustained contact with the ground, eventually degrading over time.Peter Craig
Homeowners also are turning to vapor retarders as residential homes become more energy efficient and “tighter.” Owners have grown concerned about controlling mold growth, radon gas, greenhouse gases and high humidity caused by ground water vapor moving inside the building envelope (the migration of moisture from the ground is a primary way moisture gets into homes). Installing vapor retarders during home construction is the first line of defense, and a range of materials are used by manufacturers to make their products—primarily plastics of varying combinations, character and quality.
Vapor retarders can have an immediate effect on slab curling because free water in the slab can only be lost from the top down. Ideas as to where the vapor retarder should be located below a slab-on-ground have changed over time. For many years it was thought they should be covered with a minimum of 4 in. of compactible fill material to reduce the effect of initial slab curling and to protect the membrane during construction. However, experience shows that placing fill material over the membrane can trap water over time and lead to more curling. A layer of fill over a vapor retarder can also act as a conduit for moisture to enter and migrate below the slab from any tear, puncture or unsealed penetration in the material.
Today, best practice suggests that membranes should be placed directly under the concrete to provide the highest level of moisture protection for moisture-sensitive materials and environments. Many of today’s vapor retarders have sufficient puncture resistance to handle the rigors of construction abuse.
Vapor Barrier or Retarder
Bret Houck, vice president of business development and marketing for Stego Industries of San Clemente, Calif., says the term “vapor barrier” has been in use for many years to help differentiate between products’ abilities to impede water diffusion, known as their permeance levels or ratings. “The terms vapor barrier or vapor retarder have a tendency to be used interchangeably, but what is important is the tested permeance level and whether it will protect the flooring materials, stored goods and indoor air quality of the facility,” he explains.
Recognizing this fact, the American Concrete Institute (ACI) and ASTM committees are considering being more consistent, changing the term “vapor barrier” to “vapor retarder” in order to be more factual.
Materials
Vapor retarders are rated by their permeance, which refers to the degree a material will allow water vapor to pass through it. Peter Craig, president of Concrete Constructives, Greene, Maine, says the technical definition for permeance is: the mass rate of water vapor flow through 1 sq. ft. of a material of one grain (1/7000 lb.) per hour induced by a vapor pressure gradient between two surfaces of 1 in. of mercury. But permeance is usually reported as a number, and when comparing one product to another, it is important to note whether the reported units of measure are the same.
There are different materials used in the construction of vapor retarders, including polyethylene resins, aluminum sandwiched between protective materials, and others. Houck says the quality and performance of a membrane is impacted by many factors such as resin quality, composition and manufacturing processes. He adds that manufacturers often blend different resins together to produce a finished vapor retarder with all the desired qualities.
There are three primary requirements for vapor retarders:
- They must prevent almost all water vapor movement through the membrane;
- They must be strong enough to resist the abuse of forming, placing and finishing the concrete floor on top of them;
- They must be able to perform over time, as withstanding sustained contact with the ground and the high pH of concrete is challenging.
To do this, ASTM E 1745 (Standard Specification for Plastic Water Vapor Retarders Used in Contact with Soil or Granular Fill under Concrete Slabs) defines three classes of membranes: A, B and C. These classifications relate to the toughness of the membrane. Contractors should choose the class of membrane that best fits the abuse they expect during construction.It’s best not to penetrate vapor barriers with form stakes, so the contractor for this job used a product that rests on top of the membrane. Rebar reinforcement is also supported on “dobies” that rest on the membrane surface.Stego Industries
Class A is the strongest in terms of tensile strength and puncture resistance, while Class C has the least resistance. If you are constructing a large warehouse floor, for example, and plan to drive ready-mix trucks over the vapor retarder to place concrete by direct deposit, use laser screeds on wheels that maneuver in and out of position, or place rebar reinforcement on top of the membrane, it would be wise to use a Class A vapor retarder. But if you are placing concrete with a boom pump and aren’t planning to use a laser screed, choosing a less expensive Class B or C membrane may be acceptable.
Craig says it is important to select vapor retarder products made only from virgin quality resins. Products constructed of recycled materials are subject to deterioration in the ground and may not maintain their original level of permeance when subjected to the conditioning tests required by ASTM E1745.
Vapor retarders also come in different mil thicknesses, typically ranging from 6 to 20 mils. Specifiers often equate mil thickness to puncture resistance. Craig, however, believes that it is better practice to review the manufacturer’s published data for puncture resistance than to simply select a product based on mil thickness. In his and others experience, a 15 mil or greater class A vapor retarder is needed if ready-mix trucks, concrete pumps, laser screeds, concrete buggies or pump lines travel across the membrane.
Radon Gas
Aside from preventing moisture vapor from the ground from getting inside a building envelope, vapor retarders can also keep out hazardous gases such as methane, radon and other greenhouse gases.
Radon gas is a natural, chemically inert but radioactive gas resulting from the decay of uranium in the Earth and the second leading cause of lung cancer behind smoking in the United States. Left unchecked, the gas, like water vapor, moves through the ground and into buildings where it accumulates. It is of special concern for residential homes, especially more energy-efficient ones, because the gas can reach dangerous levels.
During the construction of a home, it is relatively easy to mitigate these gases with the proper installation of vapor retarders. For this reason alone, residential housing should include quality vapor retarders under their concrete floors.
How to Install Vapor Retarders
Standard practice for the placement of vapor retarders is described in ASTM E1643–18a. Contractors should follow those guidelines as well as the manufacturer’s instructions. Here are some additional considerations:
Compaction. Even, proper compaction is important for supporting a floor slab, but it also helps protect vapor retarders by pushing sharp aggregate below the surface and providing a stable surface that doesn’t stress the membrane. Well compacted subgrade means that ready-mix trucks shouldn’t be able to deform the subgrade surface beyond showing tire tread marks. Compaction should be tested and approved when completed because there isn’t a second chance after vapor retarders are installed.
Placement. After the material is placed there should be minimum 6-in. overlap at joints and the material turned up at the face walls and foundations. It is also good practice to lap joints so that the laps face away from the direction of concrete placement.
Vapor retarders should be attached to the face of concrete walls and foundations with manufacturer approved mastic, sealant, adhesive, adhesive strips or mechanical fasteners.
The membrane must also be sealed around any protruding electrical conduit or plumbing pipes. The goal is to create a monolithic membrane.
Reinforcement. If rebar is installed over a vapor barrier, it should sit on chairs that rest on the membrane without damaging it. Iron workers must be careful when using tie-wire to prevent it from poking holes in the membrane during construction. Houck notes that steel fiber concrete mixes shouldn’t cause damage to high-quality membranes.
Inspection. The condition of the vapor retarder should be monitored the entire time concrete is being placed. If small punctures occur during placement they should be taped, overlapping the puncture by at least 6 in. or as recommended by the manufacturer. If there are large tears in the vapor retarder, new material should be cut to cover the damaged area, overlapping the existing membrane by at least 6 in. and then taped all the way around. Contractors should avoid punching holes with stakes to secure forms.
Choosing a Protection Level
The prime reason to specify a vapor retarder is to control water vapor movement from the ground and into floor slabs. While the primary function is to protect moisture sensitive finishes and products for the present and the future, keeping gases such as methane and radon gas from collecting inside building envelopes is also a prime consideration. Vapor retarders placed directly below concrete floor slabs can also help reduce the potential for slab sweating to occur in unconditioned big box warehouses and reduce the potential for additional floor curling to occur over time.Because the contractor placed concrete from the back of ready-mix trucks, they didn’t select a vapor barrier with enough puncture resistance to remain intact under the wheels of the trucks.Joe Nasvik
However, there is strong evidence that vapor retarders made with non-virgin materials can deteriorate over time. Common, low-density polyethylene plastic sheeting fits into this classification because almost all of these plastics include significant amounts of recycled non-virgin material.
When a specifier includes an ASTM specification for the vapor retarder, contractors are currently in compliance if they use products with a 0.1 permeance level. This means that vapor retarders with a permeance level below 0.1 are not legally required. However, today there are floor covering materials that have permeance levels well below 0.1. With multiple manufacturers offering reasonably priced below-slab vapor retarders with permeance levels of 0.01, it is advisable to specify products with permeance levels of 0.01 both before and after the conditioning tests set forth in ASTM E1745.
There is only one chance to choose the level of protection for a project, and that is before the slab is placed. Ideally, the permeance of the vapor retarder should be less than the permeance of the finished surface on the top of a floor. Unfortunately, most surface finish products don’t currently provide their permeance numbers, so for now, the best advice is to choose vapor retarders that meet 0.01 levels and below.