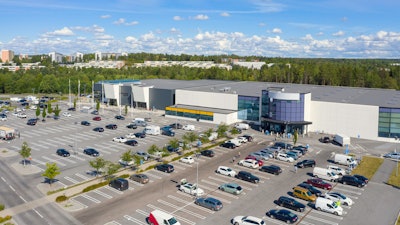
In 1962, retailers began building large suburban stores surrounded by parking lots, and the “big-box” store was born. Since then, supercenters and megastores have continued to achieve success in the retail environment. Aside from their eponymous big and boxy design, big-box stores have several identifying features: they are usually single-story structures with warehouse-style construction, have few interior columns (thus maximizing floor space), and have a concrete slab foundation.
One of the largest online retailers…has added a requirement for ACI commercial/industrial flatwork finishers on every project.
The concrete slabs often measure 100,000 sq. ft. or more and require sophisticated construction methods compared to conventional floors. Floor flatness is a critical consideration because the floors must accommodate ultra-high-density, tall-rack storage. Warehouse sections within big-box buildings may have the additional demands of narrow aisles. Robotic equipment, ultra-high-density, and buffering systems, as well as wire-guided lift trucks, may need to operate along pre-defined paths. Also to be considered are the demands from extreme loading via heavy installed equipment in addition to loading from stocked items.
Finish
Many retailers choose to install polished concrete finished surfaces in big-box facilities. These floors are aesthetically pleasing, have lower first and maintenance costs, and have a lower potential liability for slips and falls. However, if the floors are not flat enough, the polished surface makes imperfections such as humps and dips very noticeable. Many of the retailers closely link store branding with floor aesthetics, so the quality of concrete finishes is very important.
Flatness
Floors that are not flat enough will not only need extensive repairs during their service life but will place stresses on robotic and other equipment. This translates to unnecessary costs and lost time for facilities managers, maintenance staff, and project owners. Furthermore, some of the benefits of flat floors are not immediately tied to construction concerns. For example, when lift trucks and other moving vehicles can travel easily over floors that are not marred by roughness, cracks, or unevenness, they can handle materials faster, leading to greater facility productivity. They can even navigate tighter spaces, allowing for more consolidated storage and reducing the square footage required for a facility’s operation.
For the purposes of commercial and industrial floors, floor flatness (FF) measures departures from a theoretically flat plane—i.e., a floor’s bumpiness. Floor levelness (FL) is defined as deviation from a horizontal plane. ACI's Fmin values represent a separate system from traditional FF and FL. An Fmin number is used to define the lowest acceptable flatness on a superflat floor that has defined traffic patterns (where the vehicle wheels are always in the same wheel path).
The Role of Certification
Another extremely large retailer has plans to build approximately 60 distribution facilities in the U.S. They have stated their intention to specify advanced flatwork certified personnel (in addition to regular certified personnel, who have been required for more than 15 years) for the construction of both distribution facilities and stores.
Many local, national, and international building codes already require personnel who are certified by the American Concrete Institute (ACI) for various construction roles. But it can be advantageous to have ACI-certified workers for positions beyond just those required roles. Therefore, project owners—including owners of big-box stores—are requiring a greater number of certified personnel on their jobsites as well as requiring certification from a wider range of ACI programs.
The program “ACI Specialty Commercial/Industrial Concrete Flatwork Finisher/Technician” was designed to establish a higher minimum standard for all commercial/industrial concrete flatwork and to teach in-depth knowledge of concrete codes and standards. Program participants gain an understanding of various aspects of concrete construction, helping save time and effort on the jobsite. Jobsite communications are also improved among certified individuals, since there is a shared understanding of proper procedures, reducing excessive rework and making the overall project go more smoothly.
During a typical two-day program, held through various supporting organizations, certification seminars present information on the following. Special attention is called to commercial and industrial flatness requirements. Seminar content draws heavily from ACI CP-11(08), “Craftsman Workbook for ACI Certification of Specialty Commercial/Industrial Concrete Flatwork Finisher.”
- Site preparation and the placing environment
- High-quality concrete flatwork-related materials
- Preplacement setup, concrete placement and consolidation
- Application of surface treatments and finishing various classes of floors
- Surface tolerance issues
- Curing
- Special considerations for silica fume
- And more
Concrete flatwork finishing certification is offered in the following categories, with associate (technician), finisher, advanced finisher (finisher/technician) designations differing not only in the knowledge required to gain certification but in the level of hands-on skill required.
The three categories themselves represent the various types of finished flatwork installation.
- Concrete flatwork certification focuses on proper procedures and equipment to place, consolidate, finish, edge, joint, cure, and protect concrete flatwork.
- Decorative concrete flatwork certification focuses on placing, finishing, curing, and protecting decorative concrete flatwork.
- Specialty commercial/industrial flatwork certification addresses additional areas of concern and has several riders, or add-ons, available: The high tolerance floor construction rider requires an applicant to know how to manipulate fresh concrete to achieve floor tolerances meeting predefined numerical levelness and flatness measurements; The surface treatments rider includes information on items such as applying and embedding aggregate hardeners; The silica fume rider requires applicants to place, finish, control evaporation, and cure silica fume (also called micro-silica) concrete.
Those who wish to obtain their ACI certification as a Specialty Commercial/Industrial Concrete Flatwork Technician must take a written examination and complete a performance examination, constructing an actual superflat slab using a vibratory truss screed and/or riding trowels, straight edges, check rods, channel floats, finish blades and various hand tools.
Don't Lose Out on a Bid
Soon after the initial offering of “ACI Specialty Commercial/Industrial Concrete Flatwork Finisher/Technician” in 2008, specifiers for big-box stores and other commercial/industrial facilities began to require that flatwork crews have at least one ACI commercial/industrial-certified finisher. In the more than 13 years since, requirements for certified personnel have grown significantly. For example, one of the largest online retailers, who previously required the use of ACI flatwork finishers, has added a requirement for ACI commercial/industrial flatwork finishers on every project. Considering that the retailer has more buildings currently under construction than any other private entity—with over 200 in the U.S. alone—this represents a great increase in demand for ACI-certified flatwork specialists. In many of these facilities, there are thousands of robots, whose efficient operation depends on extremely high-quality concrete floors with respect to flat and level floor tolerances as well as minimal cracking and defects. Shutting a facility down for floor repairs is not acceptable.
Another extremely large retailer has plans to build approximately 60 distribution facilities in the U.S. They have stated their intention to specify advanced flatwork certified personnel (in addition to regular certified personnel, who have been required for more than 15 years) for the construction of both distribution facilities and stores. Yet another extremely large retailer has specified regular certified personnel for a similar period of time and also expects to soon require advanced finishers and commercial/industrial finishers.
Architects, engineers, and owners of big-box stores are driving improvements to project quality by specifying a greater number of ACI-certified workers on flatwork crews. Certified crew members are finding that jobsite workflows are improved, time is saved and rework is reduced. After all, it is in everyone’s interest to promote quality and maintain the highest industry standards.
About the authors
John W. Nehasil is the Managing Director, Certification, American Concrete Institute.
Bryan Birdwell, FACI is the Senior Floor & Paving Consultant/Principal, Structural Services Inc. and Chair ACI Committee C640 and others.
Jerry Holland, FACI, is the Vice President/Director of Design Services/Principal, Structural Services Inc. and ACI Committee C640 and others.