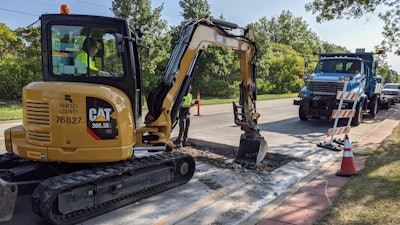
While concrete is a durable, long-lived pavement solution, some conditions—such as expansion and contraction due to temperature change, or deviations in mix ingredients—represent real-world challenges for any pavement, regardless of its material composition. Pavements are carefully engineered to accommodate the forces at work during their service life. But it is still important to regularly inspect roads, assess the extent of any pavement distress, and implement a fully adequate response.
Preventative maintenance is so named for a reason. Single problems can have a “domino effect” and, if left unaddressed, can eventually be responsible for multiple problems. Therefore, it is important to understand first the goals and best practices for the initial design and construction of concrete pavement, and second, how maintenance schedules and activities should be conducted to maximize the pavement’s life.
Transverse cracks often require dowel bar retrofit to prevent faulting. Here, a crew from Ramsey County, Minnesota, is drilling holes for dowel bars for a full-depth repair job with a 36-in. Minnich A-1 single gang drill.Concrete Paving Association of Minnesota | Matthew J. Zeller
Pavement Design & Construction Considerations
Concrete pavement distresses at times can manifest as cracking, broken slabs, buckling, or roughness, and these distress categories should be considered during a pavement’s design and construction phases.
Contraction joints are one critical consideration because reduced slab thickness along the line of a joint is intended to permit controlled cracking when the concrete shrinks. (For this reason, this type of joint is often called a “control” joint.) But joints can become filled with debris, or “incompressibles,” creating an overly rigid system that allows expansive stresses to build up. The compressive forces resulting from these stresses can cause cracking to occur in other areas of the pavement. Temperature ranges of more than 100 degrees F during a given year can translate to expansion- and contraction-related changes of approximately 2/3 in. in a 100-ft .stretch of pavement.
Modern transverse contraction joints are typically spaced no more than 15-ft. apart based on the thickness of the section. If each joint successfully cracks throughout the depth of the slab below it, the pavement will function as designed and can accommodate weather-related expansion. However, if some of the joints fail to crack—for example, if the pavement cracks only at every second, third or more joints—this makes the effective length of each panel much greater than 15 ft. Consequently, when panels contract, they are opening the joint wider than was intended, allowing more incompressibles into the space. When expansion next occurs, there is less volume for the concrete to expand into due to the imcompressibles filling the voids. After several years of this cycle, as improper transmission of forces occurs, the pavement can buckle or break in its weakest points.
In Minnesota, for example, one strategy that has been used at the time of construction to prevent future problems associated with joint function include driving heavy loads (such as full water trucks or dump trucks) along the pavement shortly after joints have been sawn. This helps activate the joints, ensuring that a majority of them successfully crack, in turn keeping each crack tighter and more resistant to infill. Using joint sealant can also help keep incompressible materials out. It should also be noted that lengthening spacing between joints at the time of construction, which is sometimes done as a cost-saving measure, is not recommended.
It's common for crews to saw cut and remove broken slabs or buckling pavement panels and replace it with an asphalt patch. However, one of the most important points when it comes to concrete pavement is to repair concrete with concrete. Here a crew from Ramsey County, Minnesota is placing new concrete.Concrete Paving Association of Minnesota | Matthew J. Zeller
Tips for Lengthening the Service Life of Concrete Pavement
Examining pavement about every ten years and performing small repairs at these intervals will save time and money over the life of a concrete pavement. Knowing not only what type of distress to look for, but a few key details about how the distress is presenting, will improve the efficiency and effectiveness of maintenance and repair procedures. For example, when it comes to concrete cracking, if there is a concern that a longitudinal crack will widen and allow the pavement to separate, cross-stitching can be performed to arrest the movement. On the other hand, many longitudinal cracks do not require repair at all. Meanwhile, transverse cracks often require dowel bar retrofit to prevent faulting and the development of a rough ride. For both longitudinal and transverse cracks (even those not severe enough to require repair), it is recommended that joint sealant be applied to minimize the intrusion of water and protect against water-related spalling, base or subgrade softening, dowel bar corrosion, pavement joint blow-ups and/or materials-related distress.
One of the most important points when it comes to concrete pavement is to repair concrete with concrete.
Where broken slabs or buckling require panel repairs, it is all too common for crews to saw cut and remove the damaged pavement and then replace it with an asphalt patch. However, one of the most important points when it comes to concrete pavement is to repair concrete with concrete. The recommended procedure is to remove all deteriorated concrete and use full- or partial-depth repair (depending on the depth of deterioration), often with dowels installed to achieve load transfer. When concrete pavement is repaired using asphalt as anything more than a temporary solution, the flexible bituminous material allows expansion and causes significant pavement movement. This movement can add up to several inches over the course of a few years and, in turn, can result in distressed areas across many square yards of the pavement surface with distresses only worsening over time. When asphalt is used to patch only the partial depth of a panel, the concrete remaining at the bottom is compromised and is likely to buckle when under a heavy expansive load.
How Much Concrete Pavement Should You Remove?
To ensure the success of full-depth repair, it is critical to determine the size of the section to be removed and replaced. Repair boundaries should extend beyond any affected areas. The most commonly used design methodologies recommend full-lane-width replacement for structural stability purposes, and typical minimum lengths vary from 3-6 ft. If patches are too small, they can rock under heavy traffic and punch into the road’s subbase. Depending upon the boundary conditions and location of the repair area, combining two small patches into one large patch area may reduce costs; however, the longest patch length should not exceed the pavement’s longest slab without reestablishing the transverse contraction joint when repairing jointed plain concrete pavements and jointed reinforced concrete pavements.
—International Grooving & Grinding Association's Full-Depth Repair fact sheet, June 2020
Another scenario in which a “band-aid” solution to concrete maintenance results in more extensive, and costlier, repairs later can be seen when dealing with concrete damage that has arisen from the improper alignment of a dowel bar or basket during construction. Improper transfer of loads across the doweled joint can cause pieces of concrete to break out. If the damage is patched with asphalt instead of using a technique that restores load transfer, stresses will continue to build, having an effect across many square yards of pavement.
A final consideration when it comes to pavement maintenance is smoothness. During construction, concrete pavements can achieve IRI (the International Roughness Index) measurements of 30 in./mile or less, creating a very pleasant driving surface. After 8-10 years, however, the variance in moisture content and/or temperature between the top and bottom of a pavement slab can possibly cause some degree of curling given the right conditions. This can create roughness, adding as much as 20-40 in./mile to the IRI. Diamond grinding is the concrete pavement preservation (commonly known as CPP) technique that will restore smoothness to concrete pavement. It can lower the IRI of a pavement by 50 in/mi. and can result in IRI values as low as those achieved during original construction. It is cost-effective and requires minimal traffic disruption. In addition to providing better ride quality and improving motorist safety, keeping a pavement smooth extends its life by minimizing impact loads. Furthermore, smooth pavements improve vehicle fuel efficiency, making smooth pavement more sustainable…not to mention passing savings along to the public in the form of reduced fuel and vehicle repair costs.
In answer to the question, “to maintain or not to maintain,” the answer is yes. Well-designed and -constructed concrete pavement can last many decades. But to ensure that it reaches its full-service life—and has optimal rideability during each year of its life—agencies should develop a preventative maintenance plan.
Small, regular interventions save time, money, and effort in the long run.
About the author
Matthew J. Zeller, P.E., is the Executive Director of the Concrete Paving Association of Minnesota.
Resources
Cross- and Slot Stitching, IGGA, https://www.igga.net/wp-content/uploads/2020/08/Aug2020_Cross_and_Slot_Stitching_1_pager.pdf
Dowel Bar Retrofit, IGGA, https://www.igga.net/wp-content/uploads/2020/06/FSJUNE2020_Dowel_Bar_Retrofit_Rebuilt_to_Last.pdf
Full-Depth Repair, IGGA, https://www.igga.net/wp-content/uploads/2020/06/FSJune2020_Full_depth_repair_FDR.pdf
Partial Depth Repair, IGGA, https://www.igga.net/wp-content/uploads/2020/07/FSJuly2020_Partial_Depth_Repair_PDR.pdf