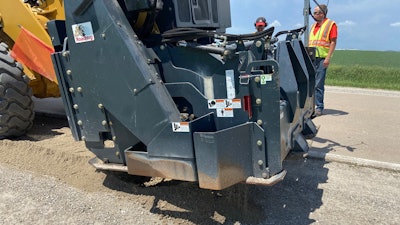
Diamond grinding is a technique used on concrete pavement to restore or improve ride quality, enhance skid resistance, and improve road longevity, among other benefits. As part of the diamond grinding process, water used to cool cutting blades combines with hardened cement paste and aggregate particulates, creating a byproduct is known as concrete grinding residue (CGR), or slurry. Historically, disposal of slurry has been regulated due to environmental considerations associated with the compounds contained within CGR (largely, these are minerals combined with chemical constituents from the cement and supplementary cementitious materials).
The Iowa State University Institute for Transportation has been active over the last several years researching the effect of CGR on transportation infrastructure systems. Three studies have generated results that indicate beneficial uses of CGR and also lay a foundation for further study in a larger number of states and with a greater range of climate, soil, and plant types.
- The first research project, “Concrete Grinding Residue: Its Effect on Roadside Vegetation and Soil Properties,” sponsored by the Minnesota Department of Transportation (MnDOT), examined the effect of CGR deposition on vegetation and soils characteristic of area roadways and published findings in 2019.
- The second, “Use of Concrete Grinding Residue as a Soil Amendment: Laboratory Investigation,” sponsored by the Iowa Highway Research Board (IHRB), focused on CGR as a soil amendment and was executed in 2020.
- The third study has the same problem statement as the second but is a field investigation. Titled, “Use of Concrete Grinding Residue as a Soil Amendment: Field Investigation” and also sponsored by IHRB, this study is ongoing, with results expected in late 2021.
Guidelines of CGR disposal methods in IGGA BMPs.Dr. Halil Ceylan, Pitt-Des Moines Inc. Professor at ISU
However, because the impact of CGR on plant growth and soil properties has not been extensively studied, many states do not have the benefit of clear, localized guidance on CGR disposal methods. This leads to a situation in which CGR disposal is potentially posing unnecessary costs for projects, as well as leaving beneficial effects of CGR underutilized (although several states do allow the recycling and reuse of CGR in some land applications and construction filling).
Guidelines of CGR disposal methods by state. / BMP = best management practices / CGR = concrete grinding residue / IGGA = International Grooving and Grinding Association / TSS = Total Suspended Solids / a = Responses from a survey distributed to DOT engineers. / b = Recycle and reuse CGR in some applications.Dr. Halil Ceylan, Pitt-Des Moines Inc. Professor at ISU
Case Studies & Results
Beginning in 2016, ISU conducted the study, “Concrete Grinding Residue: Its Effect on Roadside Vegetation and Soil Properties,” on behalf of MnDOT, evaluating slurry deposit impact on vegetation and soils. Tests included depositing slurry that had been collected from a slurry tank at a Minnesota construction site onto a controlled field site in Iowa.
As shown in Fig. 1, CGR was applied to test sections of vegetation at rates of 10 ton/acre, 20 ton/acre, and 40 ton/acre; additionally, a control section was maintained. Properties of soils and plants were assessed before the application and at points in time one month, six months, and one year after the CGR application. Key findings from the study were that the application of CGR did not significantly affect soil physical properties. Effects of CGR on soil chemical properties were influenced by application rate, soil depth, time after CGR application, and CGR source, but overall, application of CGR up to 40 dry ton/acre (the maximum amount studied) showed no significant adverse effect on soil or plant biomass.
Figure 1 a.) An aerial photograph showing the layout of the field test plots done for the ISU study "Concrete Grinding Residue: Its Effect on Roadside Vegetation and Soil Properties."Dr. Halil Ceylan, Pitt-Des Moines Inc. Professor at ISU
Figure 1 b) A diagram of the CGR applications as seen in Figure 1 a. The numbers 01 to 16 are designated to sixteen plots; letters A, B, C and D represent the CGR applications rates of 0, 2.24, 4.48 and 8.96 kg/m2, respectively.Dr. Halil Ceylan, Pitt-Des Moines Inc. Professor at ISU
Results of the study demonstrated that as CGR content was increased, the A-6 soil’s plasticity index (the difference between the liquid and plastic limit) decreased, going from an Atterberg limit measurement of 16 for the control group (no CGR application) to a measurement of 8 for the soil that received a CGR application rate of 40%. For soil type A-4, Atterberg limit measurements decreased from 7 (for the control group) to 5 (at the 40% application rate).
The study also found that with the addition of CGR, the maximum dry density (unit weight) of the soil went down, while the optimal moisture content went up. As shown in Fig. 2 and Fig. 3, the unconfined compressive strength and California bearing ratio (CBR) of each soil were found to be optimized at a 20% CGR content. The application of CGR did increase soil pH, alkalinity, electrical conductivity, and cation exchange capacity. Improvements in soil strength caused by the application of CGR are attributable to the formation of calcium silicate hydrate gel. The gel formation is a combined effect of flocculation, cement hydration and rehydration, and pozzolanic reactions.
Figure 2 a.) Effects of CGR on unconfined compressive strength of A-6 soil.Dr. Halil Ceylan, Pitt-Des Moines Inc. Professor at ISU
Figure 2 b.) Effects of CGR on unconfined compressive strength of A-4 soil.Dr. Halil Ceylan, Pitt-Des Moines Inc. Professor at ISU
Figure 3 a.) Effects of CGR on California bearing ratio of A-6 soil.Dr. Halil Ceylan, Pitt-Des Moines Inc. Professor at ISU
Figure 3 b.) Effects of CGR on California bearing ratio of A-4 soil after 7-day curing.Dr. Halil Ceylan, Pitt-Des Moines Inc. Professor at ISU
For the ongoing field investigation portion of the IHRB-sponsored research, “Use of Concrete Grinding Residue as a Soil Amendment: Field Investigation,” the first application of CGR was made in the summer of 2020 and is currently undergoing observation. Additional spring and summer 2021 applications will be made and observed. The objective of the study is to strategize the field application process for CGR and evaluate its field performance in pavement shoulder stabilization.
Figure 4 a.) A RoadHog RH60200 cold planer mixing CGR with shoulder materials.Dr. Halil Ceylan, Pitt-Des Moines Inc. Professor at ISU
To set up the field study, two CGR-stabilized pavement shoulder sections (250 ft. by 5 ft.) were constructed in Washington County, Iowa. Two different CGR application methodologies were established: a CGR reclaimed section, constructed by mixing settled CGR residue with the top two inches of shoulder materials, and a CGR application on the top section only, constructed by placing a 1/2-in. layer of settled CGR on the pavement shoulder. A section constructed with Base One (a soil stabilizing agent) was used as a control. CGR used in the test sections was collected at a diamond grinding site, then contained and transported in heavy-duty super-bags. CGR materials were allowed to settle in the bags before draining and dewatering. Figures 4 a (above) and b (below) depict the construction of CGR site in Washington County in Iowa in the summer of 2020. The team was able to take advantage of the laboratory study results, using the 20% application rate that lab studies had shown to be optimal, to achieve maximum soil stabilization in their field testing.
Figure 4 b.) A compacted CGR amended pavement shoulder with mixed shoulder materials in Washington County, Iowa.Dr. Halil Ceylan, Pitt-Des Moines Inc. Professor at ISU
Researchers compared the performance of the Base One treated section to the “CGR on top” and “CGR blend” sections using a lightweight deflectometer. Results showed high elastic moduli after 7 days for CGR-incorporated sections, with moisture playing a vital role in both 7-day and 28-day moduli (weather was a factor in the test cycle, with a lot of rain occurring). Performance measures for CGR-treated sections were very similar to the section treated with Base One, indicating that CGR shows great promise as a soil stabilizer. Dynamic cone penetrometer tests were also performed 28 days after CGR application. The CGR-reclaimed section had lower Dynamic Cone Penetrometer Index values, as well as the highest CBR values.
Work performed by the Iowa State University Institute for Transportation, when viewed alongside earlier study results from other states, allow researchers to conclude that, based on the soil types and plant communities investigated so far (with a maximum limit of 40 ton/acre), CGR roadside application poses no significant environmental drawbacks and may be beneficial in certain circumstances.
About the author
Dr. Halil Ceylan, Pitt-Des Moines Inc. Professor in Civil, Construction and Environmental Engineering & Director of the Program for Sustainable Pavement Engineering & Research (PROSPER), at Iowa State University.
This content is adapted from a December 2020 International Grooving and Grinding Technical Session. The Technical Session can be viewed in full below.