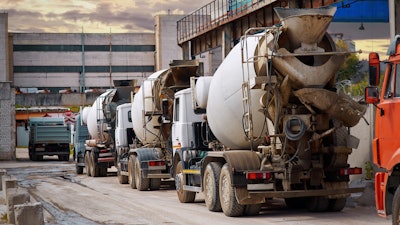
There’s never been a more challenging time to succeed as a concrete contractor. With cement in short supply and the impact of ongoing skilled labor shortages and increased demand for construction projects, many are finding themselves on allocation with even their most long-term, trusted concrete suppliers. Scheduled pours are increasingly being paused, moved back and canceled as concrete is rationed, delaying projects nationwide.
The good news, tough times often spur new product development and adoption. There are many innovative technologies being created today that can offset the dependence on portland, as well as reduce project costs and inefficiencies. Even if trying new technologies was cost-prohibitive for your business in the past, materials that are readily available now and help you work faster are likely a more cost-effective choice.
If you’re feeling the pinch of the cement shortage, now is the ideal time to look for alternative options to traditional portland and prove out their capabilities, as well as new approaches that could boost your efficiency.
Follow these four strategies for navigating the strained cement supply chain.
Substitute Traditional Concrete With Greener Products
Concrete is one of the most widely consumed materials globally (third only to water and air), and it accounts for around 8% of the world’s CO2 emissions. And though it’s only a small fraction of the concrete mixture, portland cement contributes 80-90% of concrete's CO2 emissions. However, there are many alternatives to straight portland cement available on the market today that reduce concrete’s carbon footprint.
A leading method for creating greener concrete is CO2 sequestration, a process that converts CO2 into a mineral that’s trapped into the concrete permanently and offers even greater compressive strength. In addition, there are new technologies that reformulate cement with materials that allow manufacturers to use less portland. One exciting up-and-coming technology utilizes geopolymers as an alternative to portland cement, substituting it with materials such as fly ash, ground-granulated blast furnace slag, meta-kaolin, ground mineral micro-silica or other non-gypsum based minerals to reduce the environmental impact.
When a cement shortage is delaying your projects, opting for a greener concrete that’s available now will help you get back in business faster. Many of these technologies are not widely used yet, but they will become even more common and cost-effective as more contractors adopt them. Plus, building relationships with reduced-carbon concrete suppliers now might put you ahead of the competition once others inevitably move to environmentally friendly options.
More on Shortages & The Supply Chain from ForConstructionPros.com
Construction Industry Experts Discuss How to Solve the Workforce Shortage - What is the construction industry doing to solve a workforce shortage?
Understanding and Overcoming Your Supply Chain Woes - Why is the supply chain crisis gearing up to impinge on contractors' 2022 season yet again, two years into the pandemic? Download this whitepaper on what you need to know about the problem and some ways to combat these challenges with help from your suppliers.
7 Steps to Manage Risks in the Construction Supply Chain - For the time-sensitive construction industry, recent tariffs are proving to be the most acute and painful supply chain risk this year.
Can Robots Fill the Skills Shortage in the Construction Industry? - Robotics in construction offer opportunities to reduce the labor shortage and ensure safer jobsites.
3 Ways Technology Can Ease the Construction Labor Shortage - The construction industry is experiencing a significant labor shortage that will impact its ability to meet infrastructure targets. Here are three ways technology can help.
Implement Multi-use Products
Using products with multiple benefits may not solve the cement shortage, but it can help mitigate the impact it has on your project timelines and budget by cutting multiple, time-consuming steps down to one.
For example, look for versatile solutions such as:
- A cure and seal that also waterproofs and creates an internal moisture membrane, strengthening concrete while giving it longevity.
- A product that bonds to concrete without requiring a new moisture-vapor membrane or “vapor retarder” (for trench filling).
- Fibers that would offer more strength while providing more square yards of concrete. (Known as “fuzzy concrete,” incorporating materials such as nylon, metal or basalt can actually increase compressive strength and elongation, while providing resistance to cracking.)
Consider Precast Concrete Options
Sometimes “making it work” is better than not working at all. If you’re tired of delaying pours as you wait for your next ration of concrete, it might be time to get creative with alternative paths to laying a slab or other project needs.
For example, precast concrete options may be more readily available and a smarter choice for your next project. Not only does precast offer strength and durability, but it can also be installed with greater ease to improve efficiency and save time.
Current precast slab designs have been developed that are being used for rapid highway replacement. These slabs are factory-made with high precision and quality control and are placed on laser-graded aggregate substrates. The slabs are connected to each other using dowel pins or keyway interlocking designs. These panels can be considered as alternatives for slab-on-grade solutions for industrial or commercial buildings. The keyways are then sealed with a self-leveling cementitious or polymer infill. Hollow-core slab either as precast or cast-in-place can also be utilized in this manner to reduce the volume of total concrete in a slab by as much as 50%
Choose Local Suppliers & Materials
When you partner with local, domestic suppliers who aren’t dependent on international ingredients, it will give you the confidence of having just-in-time flexibility, as well as the ability to potentially buy ahead and amass a “safety stock” of your critical components.
Though sourcing materials internationally may be the cheaper option, as the recent supply chain crisis has shown us, you might be unable to get them when you need them — and then find yourself paying for a more expensive option anyway. Instead, look for domestic suppliers as close to your location as possible in order to cut down on transportation expenses, and then build any extra costs into your project estimates.
While the cement shortage has posed many challenges, it has also opened the door for the adoption of innovative new technologies and approaches that will help to move the construction industry forward. Contractors that seize this opportunity to embrace alternatives and adapt to the needs of the moment will set their businesses up for future success.
About the author
Jack Aspenson is the CEO and president of S3 Surface Solutions, a disruptive, client-driven organization that focuses on providing environmentally friendly, simple surface systems that are long-lasting and cost-effective. With more than 25 years of experience in entrepreneurial business development, consulting and sales management, Jack knows how to develop a competitive advantage.