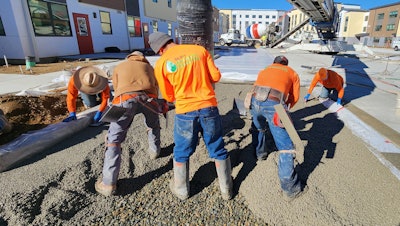
Pervious concrete has come a long way in the last 20 years, with several significant developments along the way. Pervious concrete now has its’ own ACI Committee (522). The first ACI specification for pervious concrete was issued in 2008, with the latest version of the specification coming in 2020. There is also an ACI Report on Pervious Concrete - PRC-522-10, and this report should have an important official update in early 2023, including a much-improved section on how to design pervious concrete mixtures and the most recent information on quality installation practices. Along with the specification, pervious has several specific ASTM standards with the two most common being C-1701 for hardened infiltration rate and C-1688 for fresh unit weight. (Additional specs from ACI: Spec-522.1-20: Specification for Construction of Pervious Concrete Pavement, Spec-522.1-13 Specification for Pervious Concrete Pavement)
Also, there is a well-established certification program for contractors who install pervious concrete pavements developed and administered by the National Ready Mixed Concrete Association. Contractors placing pervious pavements are required to have a minimum number of their placing crew certified through this program to meet the requirements of ACI 522. In addition to the certification program, NRMCA has published an excellent document on the maintenance and cleaning of pervious concrete pavements (free to download) to provide owners of pervious pavements good information about maintaining the infiltration rate of their pervious concrete over the service life of the pavement.
Another important change in the last 20 years is the demand for permeable pavements of all types, especially in urban areas. Increasingly stringent regulation around stormwater is the primary driver of this demand, along with a much-heightened awareness of treating stormwater as a resource rather than nuisance. A significant percentage of urban pavements will be permeable as we move further into this decade—pervious concrete is well-positioned as a material to serve this market.
Project Design
Long-lasting pervious concrete pavement systems start at the design phase of the project. Early pervious pavements often had a very unrealistic pervious-to-impervious ratio, with small areas of pervious receiving large volumes of runoff from adjacent impervious pavements. This, combined with a near total disregard for even basic maintenance practices related to the pervious, led to pavements whose infiltration rates rapidly declined due to clogging from sediment in the runoff from those adjacent pavements. While each pavement system is unique in terms of this ratio experience has shown that a ratio of 1 to 3 works well in many circumstances and provides the owner with reasonable maintenance intervals for the life of the pavement system.
Designers also must pay attention to managing the flow of water from adjacent non-paved areas onto pervious concrete surfaces, and they need to think differently about potential clogging sources from adjacent landscaping and trees. In areas subject to freezing, designers also need to ensure that pervious pavements will not hold liquid water in large rain events. This is a primary factor in determining the amount of base stone to put under pervious concrete, and there should be positive drainage at the top of the base stone storage area to insure that water will not rise back into the pervious pavement where it would be subject to freezing.
Pervious Concrete Mix Design
Successful pervious concrete installations revolve around good mix designs. Early pervious mix designs were extremely unfriendly to placement and resulted in many project failures, with the most common problem being pavements that shed the gravel from the top layer of the pavement. This is called raveling and the primary cause is placing a mix that is too dry, often combined with insufficient curing. Modern pervious mixes are dramatically more workable, and they allow contractors to achieve much higher production rates without undue risk of raveling surfaces. Mix designs are primarily the responsibility of the ready mix producer but the best mix design is the one that producers and contractors work on collaboratively. Unless you are placing pervious using slip-form pavement equipment, a modern pervious mix is what you want—this mix will come down the truck chute without any assistance from you, and the paste in this mix will have a yogurt-like consistency that produces durable pervious concrete pavements, without closing the voids in the mix as you place and compact the mix.
Photo courtesy of David Liguori, Bay Area Pervious Concrete
Most experienced pervious contractors agree that the use of hydration stabilizers is essential for all pervious mixes and I am certainly in that camp. Fibers are also common components in pervious concrete mixtures and they are on my personal "must use" list. Fibers provide benefits in both the hardened and plastic pervious concrete and they extend the contractor’s window of success in terms of consistency during placement of individual truck loads. There are many other additives and admixtures that can be used to dial in the strength and performance of pervious concrete. These include water-reducers, super-absorbent polymers (SAP’s), viscosity modifiers (VMA’s), silica fume, nano-silica products and many others depending on the particular application.
Base Preparation
Pervious needs a stable, free-draining layer of base directly underneath the pavement. In most areas this will be crushed stone and it is important that this material be washed—no dense grade! The depth of the gravel layer is primarily dependent upon the amount of water that the designer needs to store in the base but will often range from 6-24 in. or more. For thicker gravel layers, use a large stone (1 1/2 in. or larger) for most of the depth and compact this stone as it placed. The last 3-4 inches should be a 1-in. stone (like a #57) and this should also be compacted. This will minimize rutting of the base as loaded trucks deliver the concrete, and it will prevent potential settlement especially in deeper base courses.
Compaction of the dirt underneath the gravel base should be limited to maximize infiltration of the water into the soil. If the project calls for a geotextile fabric it MUST be a non-woven fabric.
Photo courtesy of David Liguori, Bay Area Pervious Concrete
Forming & Placing
Forming for pervious is essentially the same as for conventional concrete. With modern pervious placement methods (now called the 1-step method in the NRMCA certification course) it is not necessary to install thin strips on top of your forms so forms are placed to the desired finish elevation of the slab. One key difference is that all stakes must be driven below the top of the form so the roller screed can ride on the forms without being interrupted.
- Placement is generally done with a roller screed, although it is possible to use slipform equipment or laser screeds.
- Roller screed placement is best done in strips, often from 10-24 ft. widths.
- Typical thickness for pervious concrete is 6 in.
- The preferred placement method is tail-gating from the truck. Pervious cannot be pumped so if truck access is not possible, the use of a buggy or a placement conveyor is typical.
Ask your producer when they created their pervious mix design. If it’s more than five years old it is likely not modern.Photo courtesy of David Liguori, Bay Area Pervious Concrete
Placement procedures are different than for conventional concrete. Modern pervious mixes have made placement easier, faster, and more reliable but it is different, especially in the amount of time the fresh pervious concrete is exposed to ambient weather conditions. The certification class instructs installers that all pervious must be raked, screeded, compacted, and covered within 10 minutes of hitting the ground. This is absolutely possible, even for inexperienced crews, with the right approach. Placement crews need to work in close proximity to the discharge chute and not get more concrete on the ground than can be handled within that 10-minute window. The best crews get into a continuous placement rhythm with one or two people spreading and raking, two people operating the roller screed, two people edging and pulling the plastic, and one or two people cross-rolling or pan-floating. Cross-rolling can be done directly on the pervious surface or on top of the plastic while pan floating must be done directly on the pervious surface, prior to covering with the 6-mil clear plastic. Cross rolling or pan floating is the essential final step of compaction, and covering with plastic immediately protects the pervious from evaporation and loss of moisture.
Photo courtesy of David Liguori, Bay Area Pervious Concrete
Joints & Curing
As noted in the previous section, 6-mil clear plastic is specified for the initial curing of pervious concrete and that curing should begin within 10 minutes of the pervious hitting the ground. Curing should continue uninterrupted for a minimum of seven days, sometimes longer in cool weather, before the pervious concrete is opened to traffic. Some areas of the country use materials such as soybean oil or some type of spray cure on the surface of the pervious, and some mix designs include internal curing agents (like SAP’s). All of these materials have benefits but none of these materials can substitute for that minimum seven day curing period with 6-mil clear plastic.
Most contractors today have shifted to using saw-cut joints instead of tooled joints, especially for pavements that will have vehicle traffic. I am firmly in this camp for several reasons. However, this does complicate maintaining the 7-day curing period. The best practice for pervious seems to be saw cutting the day after placement to guard against raveling of the saw-cut joint while removing the smallest amount of plastic possible to allow for the saw-cutting process. Some contractors will cut the plastic and peel back each edge just far enough for the saw to operate and keep the pervious wet during the sawing process. After sawing is complete, the plastic covering is immediately restored using a thin strip of additional plastic to cover the seam.
Contractors definitely need a plan for keeping the plastic in place for the full seven days. (Throwing a few rocks on the edges does not constitute a plan.)
In summary, modern pervious concrete mixes have dramatically improved in terms of placeability and speed of placement. These same improvements offer significant benefits to the hardened pavement (and their owners) for longer service life. Installation practices have also been refined and are critical for achieving high-quality pervious concrete pavements.
About the author
Alan Sparkman, CAE, LEED AP, CCPf, is the Executive Director of the Tennessee Concrete Association.