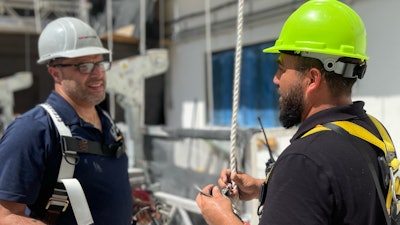
According to estimates from Moody's Analytics, Hurricane Idalia has left a trail of destruction across Florida’s Gulf Coast and is expected to cause between $12 billion and $20 billion in damage and lost economic activity. The work on clearing and restoring services in some areas has already begun, with a shortage of labor and material delays - it may take several weeks or months for reconstruction for a full recovery of the affected areas.
Amidst the Atlantic hurricane season (June 1 to November 30), Concrete Contractor reached out to capture the perspective of an industry insider. One that's worked through one or two hurricanes themselves and helped reconstruct buildings and homes afterward. We inquired about his experience with material shortages, how he has embraced technology and addressed inefficiencies with paperwork, as well as insights into trends.
Greg Batista, PE, CGC, CEM, LEED AP, founder, president, and CEO of G. Batista Engineering & ConstructionG. Batista Engineering & Construction
The combination of his 30+ years of experience with high-rise construction, engineering, and repairing, as well as being the engineer of record provides him a unique point of view within the construction industry. His accomplishments include having taken the stand as an expert witness for more than 200 cases, sat on the board of unsafe structures for Broward County, and offered his insight into the Champlain Towers South/Surfside Building collapse for a handful of interviews.
Q. What can you tell me about your work with hurricane reconstruction?
I've worked with AshBritt for many years; the owner is a personal friend of mine. They are a disaster recovery firm. We would go to a Hurricane Charley or Hurricane Irma and help the municipalities to bring the people their properties and buildings back to working order. When Maria went through my home country Puerto Rico, I went over and helped them with their hurricane recovery efforts. I have had a few federal contracts after the Haiti earthquake in 2005.
It's not necessarily rebuilding buildings as opposed to putting roofs back on them. For example, I remember Hurricane Charley which came through Punta Gorda quite a few years ago. Half of the roof of the Emergency Operations Center had been blown off. We were tasked to try to put the roof back on a pre-engineered metal building. [The hurricane] basically took the roof and started to roll it. Imagine a huge can opener just opening it up with the roof just rolling in on itself. Half the building was exposed. The entire sheriff's office of Charlotte County was located there. We got there the very next day. The sheriff's office was basically closed... a lot of the evidence that they had for pending cases, like, drugs, money, and things that were used as evidence was completely open.
We actually reroofed the municipal building in about a week. We had to bring in a helicopter to bring in materials. A lot of what AshBritt does in disaster recovery is picking up branches and trees and things that have toppled the light poles and electricity lines - taking them off the road. Because if that is not done first, then the people bringing in materials and contractors can't do their job. We're basically used to being the first line of defense.
More on ForConstructionPros.com
The Challenges of Repairing Sanibel Causeway After Hurricane Ian - Listen to Brandon Noel on the Digging Deeper speak with Central Florida Divsiion Manager Ryan Harmrick about the difficulty faced with a job like the reconstruction of the Sanibel Causeway.
G. Batista Engineering & Construction
Q. Construction across the country is challenged with limited skilled labor. Can you comment on Florida's state of construction workers?
It's a nationwide thing. There are several reasons and there are some idiosyncrasies to Florida that I can talk about. Let's talk about the 10,000-ft. level. Right now, there's basically a labor shortage and it's not as much a labor shortage as there's a lot of work. Because interest rates were low for a very long time, the Fed was pumping money into the economy, and there was just cheap money out there. People had money for various reasons - that's what allows people to go out and spend in restaurants and on building. It allows developers to build more buildings. If there's a lot of money in the system, automatically there's a lot of construction work going on. The money that's in the system allows people to spend and the more they spend, the more need there is for labor to fulfill that need. In that being the case, yes, there is a labor shortage in that sense.
Second, you've got the pandemic. That's another thing that I, personally have been affected in my business. The pandemic has taught us that we've got all this technology, why don't we take advantage of it? A lot of people have. They call it "the great resignation." People are taking more into consideration the work-life balance and they're leveraging technology to their advantage.
I've had my company for 20+ years, and I've never had anybody ask me, "I want to work from home." In the last 6 to 8 months, I must have interviewed five people and all of them say that they want to be able to work from home. Because of the pandemic, people have gotten into this mentality of wanting more of a work-life balance. A lot of people do a lot of freelance work, a lot of people move out of the country and are able to work productively doing things that traditionally you would have had to have been in an office setting - coming to work 9 to 5 and sitting in an office with a bunch of other people.
We live in a capitalistic society where you go the path of least resistance to make the most money. If employers are out there and see that their employees are happy working from their house and probably more productive or whatever, then fine. But at the same token, you've got people who don't necessarily want to go to work because that that mentality has changed. I think that that plays a little bit of a role also.
Let's go down to the more local level.
Ron DeSantis signed a law, I think it started July 1, when a lot of the immigrant workers were deemed illegal all of a sudden because they had to go through the e-verify system. A lot of immigrants have left.
It's sort of onerous to the construction industry because we recognize that, especially here in South Florida, the majority of the workers who do landscaping, masonry, and carpentry are immigrant workers.
It affects the business. I know other owners of other construction companies that have been affected by that. It doesn't help. That just worsens the labor shortage, especially down here in South Florida. And then storms like hurricanes come through and just make everything worse.
Inside the offices of G. Batista Engineering & Construction.G. Batista Engineering & Construction
Q. You mentioned people leveraged technologies during the pandemic, what technologies did you use?
Before the pandemic...a lot of people didn't use Zoom. Now, it's sort of the de facto way that you're going to have face-to-face conversations. I've had several interviews where it's been over Zoom. I've had interviews with prospective employees over Zoom. A lot of my meetings that I have with the different boards are over Zoom. It's become more mainstream now. It lays the groundwork for more flexibility as far as your time - to stay home and be with your family instead of being on the road and traffic.
I've been developing a system to streamline and make everything electronic. For example, after the collapse of the Champlain Towers, I wrote several books about it. And I've been involved in one way or another with putting forth recommendations so that a tragedy like that doesn't happen again.
For example, 40-year certifications were once only done in Dade and Broward County. Because of Champlain Towers, they're:
- required statewide on buildings that are 40, or 25, or 30 years old,
- that all the buildings get inspected by an engineering firm, or architecture firm,
- and then they're required to get repaired, along with many more recommendations.
I looked into the future and said, "We need to be prepared for this tsunami of engineering talent, of engineering work that's going to be coming down the pike." I've used technology to form a system whereby if somebody calls and needs an inspection, everything's done electronically. In two minutes, the person gets their proposal. They sign the proposal electronically. As soon as they sign the proposal, they get an automatic email that they can pay. Once they pay, everybody gets a notification. The inspection gets assigned to one of my inspectors.
Everything is automatic. I'm also developing a system where all the inspections are done on an iPad or a phone, instead of paper and pencil. Everything gets transferred through the cloud. Everything is streamlined.
This is something that's possible only in the last few years because of technology. People have been adopting it more and more. I'm very excited because we've been beta-testing it for the last couple of months and it's been a huge success. We're ready for the onslaught of work that's going to come down because of the imposition of these new inspection laws.
I see these systems, tools, and technologies available. I see that this work is coming down the pike. It's only natural that I married both of them. The more efficient we are, the more money we're able to make and - at the same time - we're able to help more people.
More on ForConstructionPros.com
Which Technologies Spurred by Pandemic are Boosting Construction Profitability Most? - In this episode of the Digging Deeper podcast, Ronen Ven Gosh, general manager of Egnyte’s construction division shares insights derived from the change in contractors’ adoption and use of software since the onset of the COVID-19 pandemic.
Telemedical Service Delivers Managed Healthcare Directly to Construction Jobsites - Dr. Dan Carlin tells how his company, JobSiteCare, is delivering physician-led managed healthcare directly to injured or ill workers on the construction site.
How Wirtgen America Stayed Close to Customers in a Pandemic - Companies all over the world had to adapt quickly when the pandemic hit. Jessica Lombardo, editor-in-chief of Asphalt Contractor magazine talks to Matthew Graves, director of Marketing at Wirtgen America, about the lessons they have learned over the past year.
Pennsylvania Contractor Poole Anderson Construction Shares Lessons Learned From the COVID-19 Pandemic - Listen to this Digging Deeper podcast with Stephanie Schmidt, president of Pennsylvania-based Poole Anderson Construction, to hear about the challenges her company encountered during the pandemic-related shutdown in her state and how the company positioned itself to move ahead both during and after the shutdown.
G. Batista Engineering & Construction
Q. How do hurricanes affect construction workers in the industry?
Having worked in and after several hurricanes, I can say from first-hand knowledge that there are people from different states who are already on-call. They have their trucks, they have their equipment because it takes special equipment to be able to, you know, pick up trees and garbage and to bring in the equipment required to do recovery efforts.
There are people on call from places like Alabama, Georgia, Tennessee, Louisiana, and Texas. They see a storm coming, they're already there. AshBritt has a whole nationwide network of these contractors. So, to that extent, you have a network of contractors that supplements the workforce in the state but still, it puts another pressure on the already thin local workforce.
It absolutely doesn't help that whenever there's a hurricane or something, people tend to gravitate to those areas just because they can make a quick buck knowing that there are desperate people who need a tarp on their roof or an emergency repair.
Q. What situations have you run into around material shortages?
It's not as bad as it was before, but we're still seeing a little bit of a trickle of that of that issue.
Material shortages are one thing. Supply chain issues are another. A supply chain is something very complicated. As a chain, some links are very strong and some are very weak. If a weak link breaks, the supply chain collapses.
For example, a lot of raw material comes from China like aluminum. From the moment aluminum is mined, to the moment it fabricates an actual window into a job, it has to go through many hands. During the pandemic, because of the labor shortage because of the pandemic, there were a lot of issues getting aluminum to come into the port in California. If you watched the news, you saw hundreds of ships ready to come in and nobody was there to discharge the cargo. That was a weak link nobody really thought of, if we don't have the labor to take the stuff off the trucks, the entire nation automatically has a quote, unquote, aluminum shortage. There wasn't an aluminum shortage it was just a weak link in the supply chain.
We had a job, where, where we were replacing a $6 million window job. I'm used to getting windows in four months after everything's approved. I called the window manufacturer, and because of the shortage and the things that happened with the supply chain, I wasn't able to get the windows for another 10 months.
The effects roll downhill. The jobs become more expensive, and there are more and more issues.
That's just one example. There used to be a problem in getting paint, waterproofing materials, and things of that sort. It's not as bad as it was before, but we're still seeing a little bit of a trickle of that of that issue.
Q. How can situations like a hurricane make delays like these worse?
The big problem is the labor.
Well, right now, at this moment the big problem is the labor. Like I said, we're sort of out of that blowback from the really serious problems of the supply chain.
My friend contractors tell me, "I can't find anybody." They can get the materials, but it might be a challenge as they may be more expensive because of the inflation. But, we can deal with that. You can throw money at that problem and it will go away, right? But right now, it's a matter of finding, finding people to actually do the job.
About 6 weeks ago, I went over to Puerto Rico because I was looking for workers. It's been so bad over here that I had to bring people over and now I'm trying to find a couple of engineers. They said, "You're looking in the wrong place. We have our own shortage of skilled professional labor workforce - white and blue collar." It seems that it's a national thing. Puerto Rico has their own reasons adding to their labor woes.
Q. Why do you think people aren't going into the construction industry?
This is a theory that I have. I've been doing construction since 1989 and I've seen how the general interest to not gravitate towards building things with their hands and getting to know a trade. It's my personal experience that kids would grow and follow in their father's footsteps if he was a carpenter, or they would go to a trade school. Now, it seems as though people don't necessarily want to get into being a welder or a mason. This has been a gradual thing that's been happening over many years.
The need for skilled tradespeople is becoming more and more noted in the industry.
I don't know what the solution is. Maybe teaching the young children and younger adults that there is value; you can make money being a welder. I know a lot of welders that make more money than a lot of engineers if you're if you're skilled in that.
I think it's a matter of education. When I was when I worked for Turner Construction, I instituted here in Miami, an organization called Youth Force 2000, back in the late 90s. Turner saw that there was a tendency for people not to want to get into trades. They saw that it was important to begin training young people.
As an engineer myself, I used to go to middle schools; I used to be part of engineering clubs and high schools and stuff like that. We need more of that if this labor shortage is gonna get better
When I worked at Turner Construction, they were the largest construction company in the world. They had the resources to be able to do those kinds of things and make their mark on the world. I would love to do something like that because I've always been involved in the community in one way or the other and giving back.
Q. Are there any lessons learned for contractors from hurricane reconstruction efforts?
There are lessons regular people who are not in the industry can learn: put in hurricane-proof windows, weatherproof their houses, to take care of themselves, to follow safety protocols, have inspections from engineers, and be proactive as far as protecting your house in case a storm comes along.
I don't know if there's anything that contractors can learn. Our contractors that have been doing this for a long time already have the mentality "I'm going to do the work, and I have to travel three miles to my office and come back." Contractors already know that that it is part of your job, that you always have to go to the work - the work is never going to come to you.
Maybe one month you have a job that's that's a mile away from your house. And maybe the next year, you'll have a job that is a two-hour travel. It's the nature of the beast. Contractors are in that mode...you have that mentality that you're going to go and you're going to you're going to get the job done. You're going to have your contacts, of suppliers, vendors, renters, or labor force prepared so that when the time comes to do the job, that you do it.
And when the time comes to do the job, whether it's because of hurricane pass, or whether it's because that job that you were you were waiting for the contract for a year, all of a sudden it's been signed. It's go time. You need to be on your toes.
I don't know if there's anything that contractors can learn from the fact that there's a hurricane, but there are lessons regular people who are not in the industry can learn: put in hurricane-proof windows, weatherproof their houses, to take care of themselves, to follow safety protocols, have inspections from engineers, and be proactive as far as protecting your house in case a storm comes along.
There's a lot of lessons to learn. There's so much information out there that it's almost negligent [to not weatherproof/hurricane-proof their house and prepare themselves]. It exposes themselves and their their loved ones. I think that's the most important lesson. Whether it's concrete or whatever, you've got there's a lot of professionals out there such as myself that do this for a living. And all it takes is one phone call.
It's like what happened in Champlain Towers. They called me out to take care of a waterproofing problem on their pool deck. I talked to them. I talked to the board in 2017 and told them, "This is not a waterproofing problem, you have a concrete repair problem."
The point is that you've got professionals that are out there that that that do this for a living and they give good advice. Build on that. Give good advice that you know people should take into consideration.
Any contractor that has been doing this for a long time is already prepared with tools, contacts, a network of vendors, etc. - whether it's a hurricane or whether it's a contract that's been waiting to be signed for a year, all of a sudden "it's go time" - you have to be ready to go.
If there are any lessons to be learned, it's on the people at the legislative level to put laws together that protect people. It's on the people. It's on the insurance companies.
Use your contacts. The people who make the most money in the storms are contractors who have a good network of workers, of professionals, of vendors, and of suppliers or people who rent equipment. Those are the people that do good in the storms. But they already have it down. They just wait for the storm and boom, there we are.
G. Batista Engineering & Construction working on the Alexander Towers construction in Hollywood, Florida.G. Batista Engineering & Construction
Q. As an insider in the industry, what new technologies or construction methods have piqued your interest lately?
I've been through a lot of technologies. In the 30+ years I've been doing construction. Every once in a while, you get somebody who comes into the market with "We can do it cheaper, we can do it better, we have this material that's cheaper, that's going to last longer, that's going to have a million years of warranty." I've seen them come and go. I'm very leery of these new technologies that come down the pipe as far as building materials and methodologies.
I am intrigued by 3D printing just because of the savings in labor. You can just let it go and it basically builds itself. I'm leery about the details. Because in construction, every experienced contractor will tell you that there are a lot of things that come into play. What are you going to do about the weatherproofing? What are you going to do about the outlets? The windows? Insulation? How the roof is going to get attached? The list goes on and on.
A lot of I've seen a lot of people getting storage containers. I've seen an uptick in that. But I don't think that it's something worth the money. I've been involved in a couple of projects where people have hired me to convert these containers into something that's livable, and the least in Florida, it doesn't work. Because costs you more to rehabilitate.
Q. What trends are you seeing in construction right now?
One trend that I think is going to take off, actually: using cathodic protection methodologies for existing buildings.
In construction as a whole, I'm seeing a lot of a lot of people doing more rentals...building condos that all you can do is rent them. That's a big, that's a big trend that I've seen in the past. Why that's happening? I don't know and this comes from a guy who has built quite a few high-rises. None of them were rentals. But as you drive around...a lot of these are rentals.
I see one trend that I think is going to take off, actually: using cathodic protection methodologies for existing buildings. My bread and butter is basically repairing buildings. When you walk up to a building that's on the ocean side like Chaplain Towers was, you get spalling where the reinforcing steel inside a column, beam, or floor gets rusted. When you have a piece of steel inside of concrete, it expands and grows because there's an ocean nearby, you get lots of fluoride in the air and that gets entrained into the concrete. As this reinforcing steel inside the concrete grows, it eventually busts out the concrete. So, you see a big chunk of a column gone and you see a piece of steel inside that's actually rusted. That's what I saw a lot of in Champlain Towers before the collapse. I warned them.
Rusting is basically a chemical reaction. And that chemical reaction can actually be stopped if you put a sacrificial node like a cathode or an anode in the concrete. Basically, it's a zinc pellet. It looks like a hockey puck that you attach to the steel that's [potentially] rusting. We call it a sacrificial node because the puck is the one that gets rusted. And the steel that's inside the concrete stays as it is. It's an actual methodology and we're instituting that in a big job for a large, multinational company.
They're spending a lot of money to put these sacrificial anodes in their concrete to stop the actual steel rusting in place. Once these anodes get really rusted, they're changed out. And it can be changed out and used indefinitely. This is a technology that has been private [but] been available for many years. It's gaining traction because of all these things that have happened. And we're starting to do a lot of work with those.
More on ForConstructionPros.com
Construction Building & Infrastructure Trends for 2023 - This Digging Deeper Podcast episode features Ron Stupi, the Senior Vice President, Chief Operating Officer at the North American Division of Building and Infrastructure at Bureau Veritas, where we discuss the headwinds that impacted construction in 2022, the challenges contractors had to overcome, and the new opportunities going forward.
Material Handling Equipment Trends for 2023 & Beyond - Constantino Lannes, president and CEO of Sennebogen, spoke to us at CONEXPO. Lannes, an industry veteran, told us about the trends his customers demand—and how Sennebogen is meeting needs.
The Hottest Topics in the Construction Industry at CONEXPO 2023 - Check out this quick discussion between Tony Fassino, Caterpillar group president, construction industries, and Equipment Today's Erica Floyd during CONEXPO 2023.
Trimble’s Williams Talks Construction Field Technologies - This Digging Deeper episode features an interview with Portfolio Manager at Trimble, Bryan Williams as he and Jonathan Kozlowski uncover the technologies that can help minimize construction project delays.
Get the younger generation interested in trades. I see that becoming more and more of a problem.
Q. Aside from monetary donations, what's the best way contractors can help restorative construction efforts? How can they get involved?
A lot of people [that] show up from out of state probably know somebody locally and they just get involved. I suppose that it's getting involved as far as getting work.
A lot of it has to do with the network. If you're the kind of person who wants to "chase storms," you have to have some sort of network. That's the first line of defense and being able to establish yourself as somebody who wants to get work and help out with the hurricane relief efforts is to have that network.
Q. Any final message for the construction professionals?
To the same extent that I was involved in Youth Force 2000, get the younger generation interested in trades. I see that becoming more and more of a problem.
In my recent jobs, it's common to say, "Hey, put this cabinetry together" and then really be concerned that they really know what they're doing. When I first started in my industry, when you hired a carpenter, a welder, or mason, you weren't as worried that they were going to do a bad job. You didn't have to babysit them that much. It's not just me saying that, it's other people. If this trend continues, it's gonna be it's gonna be a bigger problem than it is now.