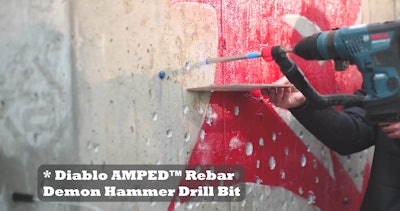
When it comes to concrete drilling, the number one challenge contractors face is bit durability. The number two challenge is dust.
As a solution provider for concrete contractors, Diablo Tools took those challenges to heart.
Four years ago, the industry-leading manufacturer of cutting tools, abrasives, and power tool accessories for trade professionals, launched the Rebar Demon four-cutter, full-carbide head solution that addressed the first of these concerns. That improved productivity on the jobsite by reducing downtime and slashing replacement costs.
Now, Diablo is doing it again.
At World of Concrete 2024, the company launched the AMPED™ Rebar Demon™, which attracted influencers and contractors alike to their often-packed booth. The AMPED™ Rebar Demon™ dust extraction hammer drill bit system has a sleeve over the drill bit that the company’s research shows reduces dust by up to 97% compared to traditional drilling applications. The result is a system that pulls the silica and concrete dust away from workers and the work environment.
“Our motto and our goal here at Diablo is ‘Best in the world. Best for our world,’” says Steve Penn, Director of New Product Development. “We're removing that dust so our contractors can work safely, get home to their loved ones at the end of the day, and continue to be able to work longer with less exposure to harmful debris on the job site.”
This new dust extraction drill bit solution also creates new revenue streams for contractors hoping to work in more sterile, closed environments like hospitals and tech centers.
The bits in the AMPED™ Rebar Demon™ system can withstand heat up to 1800 degrees Fahrenheit, while traditional bits fail at 800 degrees Fahrenheit. The goal is to provide a product that exceeds expectations so that its use continues with the contractor as their work and needs grow, including drilling into new materials and working in conjunction with new tools.
The four-cutter, full carbide head and all-in-one dust extraction system also helps with the bottom line. “It improves productivity because today end-users have to use multiple different types of accessories or vacuums, or they're finding all different ways to work around how to contain that dust,” Penn says of the AMPED™ Rebar Demon™ dust extraction system. “Existing bits today that are out there get clogged. Now you're trying to unclog the bit. While you're unclogging the bit, you're not drilling. (With the AMPED system) we can remove the sleeve, clean the bed, and continue to drill. As soon as we’re done drilling that hole, it is ready to fill. It's clean and ready to go. Users can now produce clean holes, ready for epoxy and anchor placement. This innovation virtually eliminates the "Blow-Brush-Blow" cleaning method and overall need for rebar cutters.”
Cost has long been a concern for concrete contractors, but especially now. The AMPED™ Rebar Demon™ system eliminates the need for a separate, costly dedicated rebar cutter and wasted labor time of finding and switching bits during work. Put simply, “now it’s one drill bit, not multiple accessories.”
The AMPED™ Rebar Demon™ is selling now via industrial distributors and big box home improvement stores. For more information visit www.AmpedRebarDemon.com.