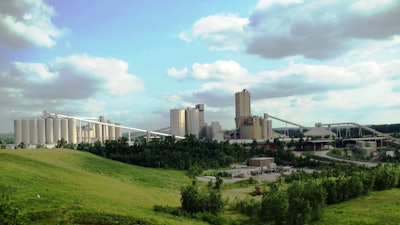
For decades, the key metrics for concrete in construction were durability, reliability, safety and cost. In recent years, however, sustainability has been added to that list by customers seeking to reduce carbon emissions on new projects. This growing customer consideration sets a new performance standard for construction materials – and is one that America’s cement manufacturers can meet.
Cement is the main ingredient in the 400 million cubic yards of concrete consumed every year across the country, and U.S. cement manufacturers -- which are represented by the Portland Cement Association -- are committed to reducing emissions at every turn. From fueling the kiln to the final product, the cement industry’s goal of carbon neutrality isn’t just for reducing the carbon footprint of the cement industry, but for construction projects nationwide.
Toward its goal of reaching carbon neutrality, the U.S. cement industry is focusing on three major priorities in the near future: the adoption of lower-carbon blended cements; using alternative fuels in cement manufacturing as opposed to fossil fuels; and carbon capture utilization and storage (CCUS). These efforts benefit project owners, design teams, and contractors, who need a durable material that meets a project’s sustainability goals.The Alamo Cement Company, located in San Antonio, Texas, launched a solar power system in March 2023. The 45-acre solar panel field (the equivalent of 35 football fields) is estimated to generate up to 15 percent of the plant’s yearly energy consumption while reducing emissions and electricity costs.Portland Cement Assocation | Buzzi Unicem USA
Lower-carbon Cements are Here & Proven
After spending years on the sidelines, portland limestone cement (PLC) has gone mainstream in the United States, hitting multiple milestones in 2023. PLC is a lower-carbon alternative to traditional portland cement that reduces carbon emissions by up to 10% while maintaining quality and durability in concrete structures.
Last year, Type IL PLC became the most common blended cement in the nation for general concrete construction. As a result, working with PLC and other blended cements has become the norm rather than the exception.
And the data backs it up. Statistics from the U.S. Geological Survey showed that by mid-year 2023, the market share for blended cements was 54.5%, and PLC’s share of blended cement was 95%. What is more remarkable is the speed at which PLC has gained this level of market share and acceptance. As recently as mid-2021, the market share for blended cements remained below 5%.
Notably, as of early 2024, all 50 state departments of transportation (DOTs) — major consumers of concrete — have formally approved the use of PLC. This is a milestone in efforts to decrease the emissions associated with our nation’s roadways and infrastructure. In California alone, a 100% shift to PLC for all Caltrans projects could result in 866,000 tons of CO2 potentially saved per year.
Another indicator that the use of PLC will continue to grow: alongside resilience and durability, the current administration has placed sustainability at the heart of its Bipartisan Infrastructure Law goals, including millions of dollars in environmental provisions that specifically call for the use of lower-carbon cements in government construction.
The demand for PLC is rising – but what does production look like? As of March 2024, approximately 50% of the cement produced by PCA members is PLC, with some companies exclusively producing PLC. And PLC is only the beginning. The U.S. cement industry is committed to creating new cements using existing and even alternative materials to reduce emissions.
In August 2023, the Alamo Cement Company's San Antonio cement plant earned the Energy Efficiency Award from the Portland Cement Association for the solar plant project.Portland Cement Assocation | Buzzi Unicem USA
Optimizing Energy
PCA’s second focus area, alternative fuels, is working to unlock more carbon-reduction options for cement producers. Efficiencies in energy use and moving toward renewables lower the embodied carbon of all cements and the concrete made with it.
The industry has made notable strides in this area, and 73% of PCA member companies now use alternative and/or renewable fuels. One example is Buzzi Unicem USA’s implementation of solar energy at its plant in San Antonio, Texas. The company’s 10-megawatt capacity solar panel farm allows the plant to reduce its power use from the grid while increasing its sustainability and energy efficiency.
GRR!’s slogan is, “Solvents to Skyscrapers, we are Fueling Tomorrow’s Construction” because their core business is converting waste into energy to power cement kilns.Portland Cement Association | Giant Cement Holding Inc.
GCHI (Giant Cement Holding, Inc.) replaced coal with natural gas to lighten the environmental impact of cement production at its Harleyville, South Carolina, plant. In 2021 alone, the company replaced approximately 25,000 metric tons of coal with natural gas and reduced CO2 emissions by an estimated 26,000 metric tons. In addition to natural gas, GCHI’s Giant Resource Recovery (GRR!) company provides discarded materials — things that would otherwise end up in landfills or incinerated without any corresponding environmental or energy recovery benefit — as an energy source.
Summit Materials’ Green America Recycling company is a waste treatment, storage, and disposal facility that allows it to replace coal with biomass and other waste-derived fuels. Summit Materials currently has a 42% fuel substitution rate, and in 2019, it used more than 130,000 tons of discarded materials as fuel at its two locations. This approach has two key benefits: reducing landfill waste and significantly cutting net emissions.
More on PCA’s member companies’ decarbonization efforts can be found at cementprogress.com.
The Mitchell Cement Plant, Mitchell, Indiana, features a clinker storage dome built out of shotcrete by Dome Technology. It measures 219 ft. in diameter and 164 ft., capable of storing 169,000 metric tons.Portland Cement Association | Heidelberg Materials North America
Carbon Capture & Us
Carbon capture, utilization, and storage (CCUS) is the heavyweight in getting the cement industry and other manufacturing industries to carbon neutrality. Most of these efforts are still in the research and development stage but hold promise for large-scale emissions reductions.
Recently, Heidelberg Materials North America has received funding from the U.S. Department of Energy to advance the integration of full-scale carbon capture, transport, and storage at the company’s new cement plant in Mitchell, Indiana. The funding will build on prior funding that has been awarded by the DOE toward successfully completing the Front-End Engineering and Design (FEED) work necessary to verify the project’s technical feasibility.
The cement industry is taking a leading role in CCUS pilot projects, with six projects currently underway at U.S. cement plants, providing learnings and blueprint approaches for other manufacturing industries looking to leverage this technology.
The cement industry hasn’t let its goal of carbon neutrality by 2050 out of its sight since launching its Roadmap to Carbon Neutrality in 2021. PCA member companies have reached numerous milestones over the last three years and have their sights set on accelerating progress -- not just for cement manufacturing, but for the industry as a whole.