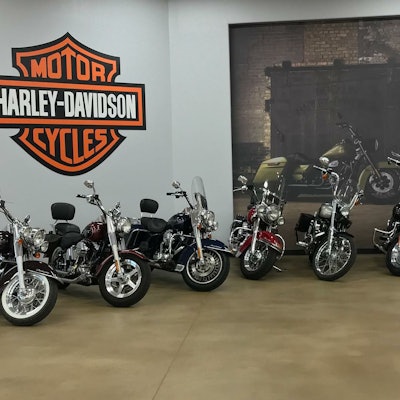
Matt Bowen, owner of Prep Concrete, a decorative concrete floor finisher in El Dorado, Calif., is always up for the challenge, large or small, when it comes to delivering the best solution to a customer’s floor finishing needs. So, when the Harley-Davidson dealership in Rocklin, Calif. presented a large challenge – 14,000 square feet large to be exact – on a tight budget, Bowen was excited.
The project goal was to deliver similar colors to the Harley-Davidson color palette, to produce a medium sheen that would always look good, provide an extremely chemical resistant floor that would also resist scratching and tire pickup. The owners also wanted a surface that could be easily repaired if it was damaged.
Bowen knew exactly how he wanted to deliver a high-quality finish for his client. He proposed using Endurable concrete stains and sealers to achieve the high-end results he knew would give the retail owner the look they wanted, but also stand up to the heavy Harley-Davidson bikes that would be moved across the floor daily.
The preparation
When a concrete floor finisher talks about the importance of preparation, Bowen is adamant about that fact and how important it is to final look and durability of any surface finish. After the carpet covering the 14,000 square-foot surface was removed, Bowen and his crew used a CPS propane-fired grinding machine equipped with 40-grit metal bonded diamond grinding wheels and an Ermator vacuum system to remove all the carpet glue.
“One of the challenges of removing carpet glue is to make sure all of it is removed, and that means chipping it out of low spots and cracks,” Bowen states. “If you don’t go to that extent to remove all the old carpet glue, it may release after you apply fillers or the stains and sealers, and you don’t want that to happen.”
He then went about repairing cracks and holes with Versaflex Quick Mender. Bowen then saw cut all joints and filled them with Metzger McGuire RS 88 Cardboard color, before using 70-grit metal bonded diamond grinding wheels for final surface preparation in order to begin the staining and sealing process.
“It’s not only important to make sure all patch work has been leveled off and blended with the rest of the surface, but to also make sure you’re opening up the entire surface in order to allow stains and sealers to penetrate and bond to the concrete,” he notes.
Grinding and patching took approximately a week and a half to complete, with most of that time spent on patching. But as Bowen knows, preparation is everything in the final finish of a project. So, after completing the final grinding, Bowen’s crew taped all adjoining walls to protect them from the stains and sealers he would use in the finishing process.
Let the staining begin
Bowen used Endurable’s Pronghorn and Milk Chocolate-colored concrete stains to achieve the earthy tan color the Harley dealership owners wanted. Five gallons of the Pronghorn were mixed with one gallon of Milk Chocolate and one gallon of water.
After applying the first coat of stain to the unsealed concrete, Bowen then locked in the color by applying a coat of Endurable sealer consisting of a one-to-one mixture of gloss and matte finish.
“Because of the large surface area, once we finished the initial staining we were able to begin the sealing process on the area we first stained,” Bowen says. “Mixing the gloss and matte sealers provided a finish with a subtle sheen, rather than real shiny or real dull.”
After the first coat of sealer was dry, Bowen went back to apply a lighter second coat of stain to add more depth to the color finish. Then he went back to apply a third coat of stain consisting of 1:1 mixture of Pronghorn and Milk Chocolate with acetone to provide some accent coloring on approximately 40 to 50 percent of the floor surface. Bowen sprayed the accent coat using a fine conical tip that only disperses .05 gpm, allowing him to have absolute control over the amount of accent he wanted to create.
“I was applying the accent in a fast manner, creating a marbled effect,” Bowen says.
Following the accent application, Bowen then applied two more coats of sealer using a conical tip that dispersed .10 gpm of material.
Bowen points out that after the Enduable sealer is properly applied and allowed to harden, you can always add more of the Endurable stains mixed with either water or acetone over the top of sealer. This capability provides greater variation of colors or the ability to hide or repair defects in the concrete.
It took Bowen’s crew two days to stain and seal the floor and a third day to allow the finish to completely dry and harden before the owners moved their shiny Harley's onto the surface.
“The low luster mottled-color finish really showcases the bikes,” Bowen says. “I like the versatility and range of color finishes I can achieve with the Endurable line. I never use 100 percent of one color. I always use a variation of colors to create a unique finish. I’ve been working with it for seven years and I’m always impressed with what I can achieve.”
Taking care of business
For Prep Concrete, versatility in delivering unique results is important to the varied client base it serves. From residential garage floors to breweries and Harley-Davidson dealerships, providing a unique and durable finish is what Bowen has relied on to build his business. Bowen handles a variety of floor finishing requests, from diamond polishing projects that can cost from $5 to $10 a square foot, to staining and sealing projects that can cost $2.50 to $3 a square foot up to $5 to $6 per square foot.
“We’re a small crew of up to five or six people capable of handling a 200 square-foot project up to a 20,000 square-foot project,” Bowen says.
“My experience has shown that water-based polyurethane finishes provide more durability,” Bowen adds. “And all customers want the finish to be chemical resistant, as well as resistant to tire pickup. The Endurable line of stains and sealers has been my go-to solution. If you prepare the surface by sanding, etching or diamond grinding it to open the pores of the concrete to allow the stain and sealer to bond with the surface, you will be successful in achieving a quality finish.”
For Bowen, that approach has served him well for the past 12 he’s been finishing concrete floors. With Endurable stains and seals, customers simply need to maintain the finish with dust mopping and occasional wet mopping, along with walk-off mats at entry points to the floor.
“You don’t need to use harsh chemicals to clean the floor,” Bowen says. “You can wax the surface or re-seal them if you think they’ve lost the sheen you want. That’s it!”