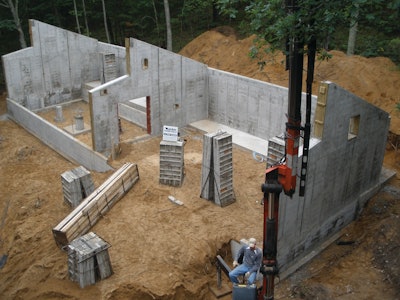
Very few concrete projects are challenge free. Kelder LLC of Scottville, Mich., recently completed a project that posed two challenges: building energy efficient, environmentally friendly walls and building one of those walls into a hill.
The project at hand was a workshop for a wood craftsman who wanted a structurally sound and environmentally friendly building. The building was designed to be built into a hill, with a large bay of windows on the front, south-facing wall. The windows allow for natural heating of the building through sunlight.
With the back wall built into the hill with 4 inches of exterior foam insulation and the front wall mostly windows, the exposed side walls were the only ones that needed another source of insulation.
To create the energy efficient side walls, Kelder turned to Thermomass insulation, says Jeff Barnett of Kelder. Thermomass is an insulation product that contractors embed between two layers of concrete. "A Thermomass wall has concrete on the inside and the outside with the insulation in the middle. You're basically utilizing the concrete on the inside wythe to hold the heat or the cold temperature," Barnett says.
The Thermomass system is made up of extruded Dow Styrofoam polystyrene insulation and fiber composite connectors. "The connectors hold the two pieces of concrete together and keep everything bound to the foam. That concrete and insulation acts as one solid component," Barnett says.
To successfully complete this pour, Kelder did four separate pours just for the walls.
First, Kelder poured the crawl space footings. That was followed by 4-foot crawl space and frost walls. Next, a large footing was poured followed by the above-grade center wall inside the shop with the two matching Thermomass walls, Barnett says.
Kelder placed the Thermomass into the forms as each was being set up, adding rebar during this process. Because of minimal access to the location, Kelder used a boom pump truck to pour the concrete on all four pours, Barnett says.
When using Thermomass Barnett says you need to use a high strength mix with smaller aggregate. "With the amount of rebar and the amount of the fiber connectors in the wall this mix allows the smaller aggregate to flow better within the wall and get to all the voids and cavities," he explains.
Adding to Kelder's challenge was the fact that the walls are sloped. Barnett says they slope from 17 feet 6 inches down to 11 feet in height. Thermomass precut the Thermomass foam to fit the sloped walls, saving time on the jobsite. Kelder also used a laser to ensure the walls were at the same height throughout the slope.
Barnett installed electrical and air runs into the walls by embedding sleeves in the wall and footings and screwing faceplates onto the panels. Once the concrete was poured and cured, he removed the faceplates and was left with an embedded box for electrical runs.
Barnett has been using Thermomass for two years and estimates he has used it on approximately 10 projects. He likes the green aspects of the product, the temperature and moisture control aspects, and the ability to use it toward LEED certification.