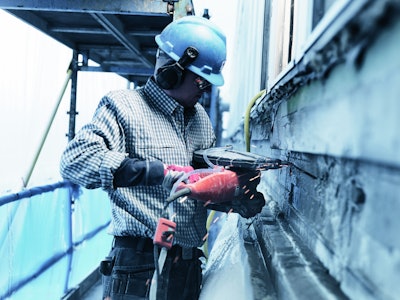
Concrete cutting and drilling is by nature a dusty business. It can also be a risky one if precautions are not taken to minimize the amount of concrete dust floating around your jobsites.
Many types of concrete, masonry and other materials contain silica, a basic component of sand, quartz, brick clay, granite and other minerals and rocks, notes Adam Hanks, industrial product manager at STIHL Inc. Crystalline silica generated as dust during the cutting or drilling process can prove hazardous to the health of operators and other workers in the area.
"There are several risks involved when exposed to cement dust," says Mike Ward, product manager for Power Cutters, Husqvarna Construction Products. "These include irritation to the eyes, nose, throat and the upper respiratory system. Skin contact may result in moderate irritation, thickening/cracking of skin or severe skin damage from chemical burns.
"Severe injuries can result from the cutting of concrete, brick, block, rock and stone products due to the crystalline silica released into the air," he adds. "Inhalation of crystalline silica has been linked to lung injuries, including silicosis and lung cancer."
Excessive dust can be harmful to cutting equipment, as well. "Concrete dust is a very abrasive material that can cause significant wear to any equipment exposed to it," says Hanks. "Engine failure due to dirt ingestion is the worst-case scenario for gasoline-powered equipment. In this case, concrete dust bypasses the air filter system and is introduced into the engine cylinder, causing wear on the piston and cylinder, loss of compression and bearing failure. Another typical wear point on gasoline-powered equipment would be starter ropes and starter assemblies."
Even pneumatic-powered drills aren't immune to dust's effects. Concrete dust has a tendency to stick to moist surfaces, such as greased areas. "That then makes the grease become more of an abrasive paste than a lubricant, accelerating wear," says Todd Jurjevic, Minnich Mfg.
It can also harden on the machine if it gets wet. "If it rains, that concrete gets hard and then you have trouble with nuts and bolts, etc.," Randy Stevens, E-Z Drill, points out. "We do try to encourage [operators] to keep [drills] fairly clean so they can make all of the adjustments that they need to make." This includes blowing dust off with an air hose every day after use.
Other equipment in the vicinity can be affected by the dust, as well. "For instance, the air compressor that powers the drill can have issues with the dust in the filters and engines," Jurjevic indicates. "Once the dust settles, the next vehicle that drives over it stirs it back up and into its system."
More incentives to take control
In some applications, the risks extend beyond workers or equipment.
"I think everyone in the industry recognizes that silica dust is a health issue, but people do not always realize the other hazards caused by dust," says Jurjevic. "Think of a cloud blowing across a lane of traffic that is already out of the normal pattern because of the construction zone. Or the worker who has decreased visibility while trying to operate equipment on a congested construction site. Consider a machine covered in dust, making all of the warning labels hard to see, let alone read.
"We have actually sold more dust suppression equipment to prevent dust clouds crossing traffic lanes or active runways than for concerns of silica inhalation," he adds.
Indoor cutting or drilling is another scenario where concerns can extend to other aspects of the job. "When we first were getting calls about providing a dust collection system, most of the time it was because they were working in a confined space or indoors, where the dust would cause a lot of problems — not just for the operator, but it may have been in a warehouse where they had shelves full of parts and they didn't want dust covering everything," notes Stevens. "One particular application was in a parking garage, and they didn't want to have dust on [the cars]."
Environmental considerations can influence the need for dust control, as well. Stevens cites an example where a contractor was working over water building on bridge piers. "They didn't want any of the concrete dust falling into the water... so they had to collect the dust as they drilled," he says.
Increasingly, dust control requirements are being written into bid specs. "Some of the jobs require it due to environmental or safety issues — safety with traffic or safety with operators," Stevens states.
He adds, "In years past, there were a lot of times where [dust control] didn't come up because they were working out in big, open spaces... It just wasn't an issue. But it's become more of one now."
Suppression and collection
OSHA should be your primary source of information pertaining to dust suppression and containment on the jobsite. However, there are some basic steps you can take to minimize airborne concrete dust on your projects.
According to Ward, "There are several tools/equipment on the market to help aid the contractor in containing dust during the cutting and drilling process. Wet cutting and vacuum dry cutting are the most common types of dust [control]."
The type and size of the job will determine which system is best to use. "Costs can run from several hundreds [of dollars] for smaller machines to elaborate dust suppression units running into the thousands," Ward states. "These costs can and should be put into the bidding process, as safety of the operators should be the No. 1 priority."
Wet cutting is the recommended method for controlling dust when saw cutting concrete or masonry. "The water binds the dust and significantly reduces the amount of airborne particles," Hanks explains. "Wet cutting reduces the amount of airborne dust created by cutting concrete and can help increase the longevity of equipment."
While many concrete saws come with some form of wet cutting system or kit, concrete drills take a slightly different approach. For example, E-Z Drill offers an optional dust suppression kit.
"It's a spray system — [it has] a spray nozzle that they can bolt on and install on the machine with a valve. All they have to provide is the water," Stevens explains. "It sprays down by the bit as it's drilling to knock the dust down."
The kit costs roughly $400 per drill. "So if you had a single drill, it would be $400 for the kit," he states. "If you had a gang drill with four drills that [produce] four holes at a time, it would be $1,600."
Dust collection systems, on the other hand, are designed to remove dust as it is generated. "Our drills are pneumatic, so we offer a dust collection system, or vacuum system, that runs off the same air compressor," says Stevens. "We have what's called a 'boot' that goes around the end of the bit guide where the bit is actually penetrating the concrete. When the vacuum is running, it sucks the dust right out of the hole and then dumps it into a bag."
Minnich has been offering optional dust collection systems for its drills since the 1990s. Initially, it purchased the systems and fitted them to its machines. "Then, in 2005, we designed our own and have been working to improve upon it as technologies advance," Jurjevic states. The system has gone through NIOSH testing twice. "We make every customer interested in a drill unit aware that dust collection is available."
The cost of dust collection can vary depending on the required equipment. For example, the contractor working on the bridge piers used its own vacuum system; E-Z Drill simply provided the boots. At around a couple hundred dollars each, this can be a relatively inexpensive option. "If a contractor has his own vacuum system, he can hook the hose right to this boot, so all he has to do is buy the boot that bolts onto our drill," says Stevens.
The cost goes up as equipment needs increase. "If they want us to provide the whole turnkey operation, we have one that starts around $4,300 on a single drill and on up to about $11,000. That depends on the number of drills they're using," says Stevens.
Designed with control in mind
Of course, manufacturers of concrete cutting and drilling equipment aren't leaving dust control entirely to chance.
"Dust ingestion can be a problem with any saw that has an internal combustion engine," notes Taccogna, "and a lot of work has been done by the manufacturers of these tools to improve air filtration. A watering system that allows wet cutting is a great way to reduce this problem because, with adequate water, most of the airborne dust can be prevented."
Most cut-off saws come with or can be retrofit with some kind of wet-cut kit that flows water onto the blade. For example, STIHL has developed an electronic water control system (EWC) for its TS 410 A (EWC) and TS 420 A (EWC) Cutquick cut-off machines. "The system uses an electronic water valve along with a conveniently mounted control pad that make controlling the flow of water to the machine easier," Hanks asserts.
ICS offers its saws with a built-in water system, as well. "All ICS concrete chain saws come with an integrated water system with a shutoff valve," says Taccogna. "Water flows through the saw and into the guidebar, so that water is actually flowing through the chain as it is cutting." Hydraulic models have an integrated water valve that is actuated by the same trigger as the hydraulic valve, so water is not flowing unless the saw is running.
Adequate filtration is also essential. "Dust ingress will wear out the moving parts of concrete saws or drills faster and therefore cause premature failures," Ward points out. "Most highly durable equipment is designed to produce as little debris as possible when cutting, drilling, grinding, etc. Advanced filtering systems and dust collection systems are also designed to safely suppress and remove dust and debris." Husqvarna's power cutters feature Active Air Filtration system, which increases filtering efficiency.
"STIHL cut-off machines are equipped with the X2 air filtration system that significantly improves filter life by removing larger particles of dust before the air reaches the air filter," adds Hanks.
Similar steps are being taken to ensure the longevity of concrete drilling equipment. "We are constantly working on ways to seal the units from dust," says Jurjevic. "We have filters in the air systems, breather vents on the valves and have even designed our rails to be on a diamond configuration so the dust vibrates off, instead of square where the dust can lay and act as an abrasive to cause premature failure."
Minnich does offer water kits, as well. "But they are hard on the drills and there are concerns where the runoff ends up," Jurjevic notes. "It is also impractical to have enough water on a job for a day's worth of drilling." That's why the company offers a wireless control unit for its equipment. "Our wireless controlled drill units do not get rid of the cloud, but do allow the operator to stay out of the dust. The best is a wireless machine coupled with a dust collection system."
The goal of these and other features/options is to deliver the optimal combination of safety and longevity. "Most equipment is designed to redirect debris away from the operator," Ward states. "The bottom line is that when purchasing equipment, safety and durability are important to remember."