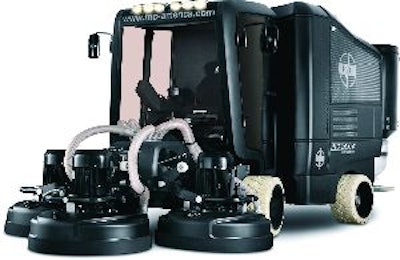
Harry Spaulding
The project opportunities for grinding systems range from enormous assignments like warehouses and sports arenas to smaller residential tasks like living rooms and two-car garages. Over the last few years, the market for polished concrete floors has risen dramatically. This popularity is due in large part to the amazing multi-functionality of today's concrete grinders. Current interior design trends and production facility requirements have also helped increase the demand for these systems.
Today's grinders are available with an enormous array of tooling options that allows them to complete a multitude of projects including coating removal, surface preparation, glue and adhesive removal as well as polishing.
The overall design of floor grinders has not changed drastically, but there have been some incredible technological advancements recently. A planetary grinder typically consists of three or four "satellite heads" 10 or 11 in. in diameter mounted on a large "planetary head" 30 to 32 in. in diameter. In the planetary head, diamonds are set in either metal or resin matrixes in different densities. The planetary head spins one way and the satellite heads with their diamond bits rotate in the opposite direction. This causes the diamond bits to travel in random patterns within the diameter of the planetary head. Coarse grinding steps are completed with metal matrix diamond pads while the finer processing steps are accomplished with resin matrix pads.
Until recently, polished and processed concrete floors have been used mainly in industrial facilities, manufacturing plants and warehouses, but they are now becoming increasingly popular in residential and retail settings. Formerly, polished concrete coloring was limited to grey, but today it is frequently seen in a wide range of colors and designs. By using integral color and surface colorants including dyes and staining, designers now have many options to choose from.
Industry growth
Planetary head grinders deliver the best surface finish compared to alternative grinding machines. This is because the movement of the grinding discs over the floor is less dependent on operator skill compared to non-planetary machines.
Planetary grinders surpass the performance of those in the past "by having multiple heads and a true planetary rotating drum that spins opposite of the three or four grinding heads; not to mention remote control, automatic laser leveling systems and fully self-contained large industrialized grinder/polishers," explains Henrik Rosencrantz, president of HTC, Inc.
Rosencrantz believes the trend toward polished concrete promises to continue to grow. "Some clients are not looking for, nor will they pay for, a very flat highly polished floor but want the low maintenance advantages of a polished concrete floor. So now you will see manufacturers putting fully adjustable flex heads and/or flex plates to allow the diamond tooling to simply grind/polish in and out of the high and low spots. Now clients have all the advantages of a normal polished concrete floor minus the levelness," he explains.
The HTC 2500 iX is ideal for projects in large industrial spaces. It is a completely integrated system with a particle filtered diesel motor allowing for indoor use. It features a hydrobox mounted cabin, an integrated heavy-duty dust extraction system for handling grinding waste, and a joystick and touch-screen for simple functionality and ergonomics with computerized articulated frame steering for enhanced flexibility. The 2500 iX has three height adjustable grinding heads and adjustable grinding pressure. Available options include air conditioning, radio, CD, DVD and communication radio.
Besides providing aesthetic appeal, part of the draw of polished concrete is its environmental friendliness. "Polished concrete as well as grind and sealed concrete are being written into specs every day, and it is really opening some people's eyes to all the possibilities that these floor options can bring in almost any environment,' says Dave Padgett, vice president of CPS. "Also the opportunity for LEED points to be obtained through the use of these 'green' flooring options is a major plus. Architects everywhere are leading the way in providing sustainable options to clients that are investing in the future of our planet. Sustainable polished concrete is an excellent example of the forward thinking necessary to provide a safe and lasting future," he says.
The new CPS G-320 and G-250 planetary grinders, as well as the G-320XT and the G-250XT, will be unveiled at the WOC 2008 show in Las Vegas. These machines are engineered to be a mixture of power, durability, convenience and safety. They feature newly designed pulley boxes rated at over 50 hp and solid gear design planetary drive system as well as the new patent pending SlipClutch technology designed for safety of both the operator and the machine. The CPS systems also include new frame designs for easy break down and use.
Coatings and colors
Manufacturers of thin coating systems, including waterproofing and epoxies, are finally recognizing diamond grinders as the wave of the future in territory long held by shot blasting.
"The coatings industry, as far as manufacturers go, has been slow moving in accepting diamond grinding as a legitimate form of prep for thin coating systems," says Marcus Turek, North American sales manager for SASE Company. " There has been positive progress made recently by forward thinking coating manufacturers stemming from positive pull test results from diamond ground preparation on concrete floors."
The SASE Diamatic 780 Pro Diamond Grinder Professional Planetary Grinders are designed for every type of concrete, coating removal, prep work and concrete polishing. It features Floating Head Technology that allows the machine to follow the contour of the floor. Combining horsepower, torque and a solid, all-metal construction, SASE Diamatic utilizes both metal and resin bond diamonds that can be used either wet or dry for concrete grinding and polishing. For dust free grinding and polishing, SASE Company has a comprehensive selection of Dust Collection Systems.
"It is well established that proper surface preparation must be carried out prior to applying floor treatments, and epoxies are no exception," says Paul Robb, Blastrac product manager - grinding and polishing. "Without proper surface preparation, coatings can fail and detach from the surface, ultimately costing the contractor more time and money. Grinders are a preferred method for thin mil and translucent coatings because they can achieve a homogeneous profile and appearance."
SASE's new designs in grinders have helped its customers increase efficiency and thereby productivity. "They're becoming more dependable and that depends on design," says John Gormley, president of StoneCare of Texas. "Before these high efficiency grinders were developed, it was impossible to economically polish concrete. That's what made me look at it."
For homeowners, polished concrete floors provide an affordably elegant alternative to expensive floor treatments - a look designers and decorators are implementing creatively in projects ranging from traditional to contemporary styles. Recent advancements in diamond grinder technology has also created a user-friendly environment for color to be added to polished concrete floors using acid stains and dyes. Additional use of overlays and decorative line cutting can create an elaborate tile pattern or a marble effect.
Smaller grinders are ideal for use in homes. For example, Ward Pedley Jr., president of Concrete Construction Corp., recently used the CPS G240 when working on a client's living room floor. "It's a 40-year-old floor that I ground and polished and put down a 3 by 3 tile pattern," explains Pedley. "It seems like the decorative market is going to continue to grow. As opposed to replacing worn out concrete, you can now polish it."
Safety and maintenance
Advancements aren't limited to how well the machines grind and polish. These systems are now considerably safer and cleaner to operate.
"The previous electric powered equipment was an offshoot of terrazzo grinders," says Ben Timmerman, owner and vice president of Blason Industries. "That type of equipment required 480 volt three-phase, and it's intrinsically more dangerous. There's been a trend in the last three to four years that the equipment has become more user-friendly." Timmerman says of his company's Blastrac grinders, "The design of these machines is the most efficient diamond grinder that I've ever seen."
"Dust collection equipment needs to be maintained properly," adds Rosencrantz. "Most all of the high end grinders have fail safes now for a projectile hazard like a grinding head or tool flying off the machine."
"In general, diamond grinders are very safe machines," says Turek. "SASE recommends the use of all standard OSHA approved safety equipment: hard hat, eye protection, ear protection, steel toed boots, appropriate respirator and any other locally required or recommended safety equipment or precautions when operating any equipment on a jobsite."
Opportunities arise
What's next? The potential for industry growth is huge. With forethought and education, even more opportunities can open up for grinder owners.
"One thing that I find often is that there has been a huge influx of popularity in concrete polishing yet most overlook the fact that the concrete grinders can be used for demolition work, coating removal and preparation for all sorts of coating and overlayment systems," says Rosencratz. "That is easy money and people or companies will pay well for a properly prepped floor to make their coating perform correctly."
"Polishing concrete takes a craftsman no matter what machine he or she uses," says Padgett. "Knowledge is the key to doing it right every time when every slab is different and reacts differently than the previous one. If the personal interaction is cut off before the knowledge base matures enough on its own, it could affect the current market to shift to companies more prepared to do so."
Harry Spaulding is a Boston-based freelance writer with more than 10 years experience in the building industry.